
DutchAero has manufactured complex parts for the aircraft industry for 50 years. With support from parent company KMWE, production engineers developed a measuring device – using 17 Heidenhain-Acanto touch probes and modular MSE 1000 electronics – fulfilling present quality assuarance tasks and equipping DutchAero for the future.
After 20 years of accurate and reliable service, at it was time to replace DutchAero’s measuring devices.
“Failure of the measuring device would have seriously endangered our production,” explains Ben Dekkers, production engineer in the sheet metal processing shop at DutchAero. “Since there are hardly any more spare parts for the old devices and associated computers, we wanted to forestall this worst case at all costs.”
Dekkers found support from colleagues in KMWE. With their collaboration, he launched the demanding project and developed the device that will accurately and reliably monitor the quality of manufactured aircraft parts for years to come.
Accurate, future-proof
“The measuring device should have at least the performance of its predecessor and also be equipped for new tasks. Apart from that, we wanted automatic acquisition of the measured values of the products to be inspected,” Dekkers explains.
KMWE engineers handled measurement device development and programming the corresponding software. Heidenhain and Acanto provided the hardware.
“The Acanto touch probes measure two different high-tech aircraft parts manufactured in series by DutchAero for the nozzle of a jet engine. The MSE 1000 acquires the measured values, produces a complete electronic report and provides easy process monitoring,” Dekkers says.
At present, nine touch probes are responsible for one part and the other eight measure the other part. In the future, however, all 17 Heidenhain-Acanto touch probes are to be used simultaneously.
“The touch probes in our measuring device work with an accuracy of ±2µm. We do not need such a high level of accuracy yet, but it gives us a margin for the future,” Dekkers notes.
The measuring device is already being used in production, and in parallel, DutchAero is testing the repeatability and reproducibility of the setup – a complicated procedure with extensive test series.
A reliable combination
Measuring tasks required by DutchAero demand special capabilities – incorrect measurements must be avoided while evaluable additional data need to be available at every machining step. Heidenhain-Acanto touch probes offer fast, reliable, and accurate measurements without requiring a reference run for every request for an absolute position value. This rules out measuring errors from excessive plunger velocity from bouncing or strong vibrations that can occur with incremental encoders during dynamic measuring tasks on test stands.
Multipoint measuring stations are becoming increasingly important in industrial measuring technology. In these applications, there is electronic control of the simultaneous acquisition of multiple measured values on one or more test pieces – with complex measuring tasks often part of a defined inspection life cycle. Modular MSE 1000 electronics make it possible to simultaneously acquire data from up to 250 measurement channels across a variety of interfaces.
Heidenhain engineers, when designing the MSE 1000, focused on simplicity for installing modules and connecting them to measuring devices. Modules can be mounted to DIN rails for tidy, compact measuring stations. System configuration of the modules is detected automatically and the user only needs to define the specific measuring channels.
Simple connection
When using EnDat encoders users do not need to configure the measuring device – it provides all the data required for operation and is immediately ready to measure. MSE 1000 electronics enable EnDat encoders to be connected in their entire functionality, giving users predictive maintenance functionality for their measuring systems. The functional reserve of absolute and incremental tracks can also be depicted from the online diagnosis functionality of EnDat devices. Users can access other operational criteria such as illumination condition, signal amplitude, and position value calculation, optimizing operational availability and system safety.

Apart from the EnDat protocol for absolute encoders, MSE 1000 supports all standard incremental encoders and provides other connection options for analog position sensors such as LVDT and HBT. Modules with switching inputs and outputs enable interaction with other actuators in the encoder.
A dynamic link library (DLL) resource is included with the MSE 1000, representing the range of MSE 1000 features on the software side and enabling operators to develop their own testing programs. For testing processes that require additional actions depending on the measuring result, it is possible to connect more inputs and outputs. This programming capability of MSE 1000 partly eliminates the need for additional control equipment.
Heidenhain Corp.
DutchAero B.V.
KMWE
Get curated news on YOUR industry.
Enter your email to receive our newsletters.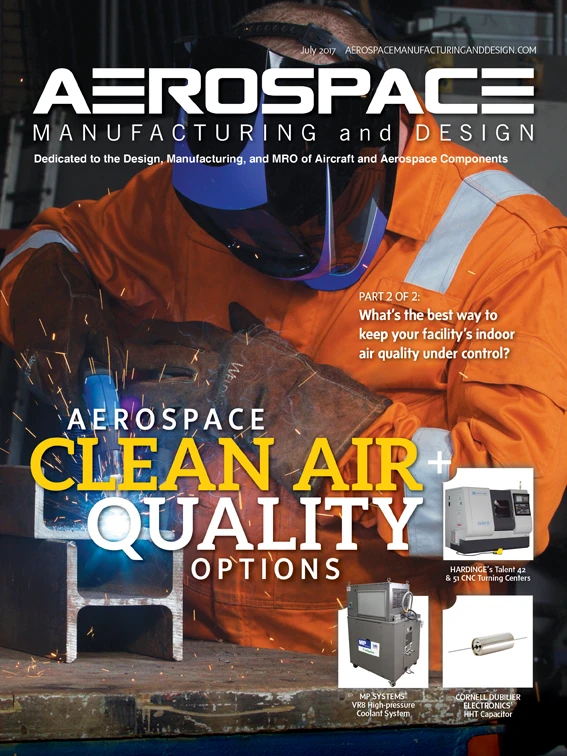
Explore the July 2017 Issue
Check out more from this issue and find your next story to read.
Latest from Aerospace Manufacturing and Design
- Address the challenges of machining high-temperature aerospace components
- Elevate your manufacturing operations with April’s Manufacturing Lunch + Learn
- America Makes announces IMPACT 3.0 Project Call worth $4.5M
- Updated parting and grooving geometries from Sandvik Coromant
- AIX showcases the future of air travel
- Sunnen Products' PGE-6000 gage
- #41 Lunch + Learn Podcast - SMW Autoblok
- Revolutionizing aircraft design without sacrificing sustainability