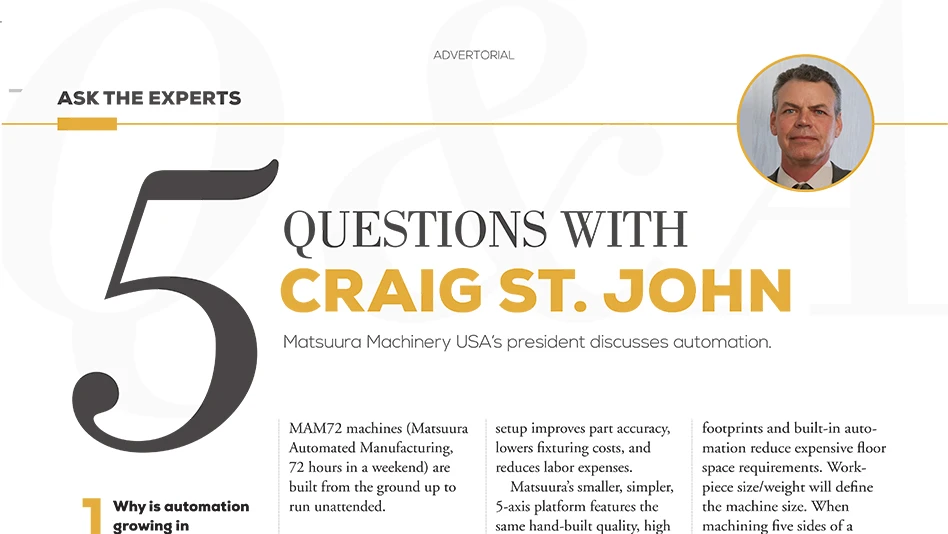
GIE Media

1) Why is automation growing in aerospace?
Aerospace companies are pressured to reduce operational costs. Successful job shops are removing as much labor as possible to maximize unmanned machining times. With the shortage and the cost of skilled labor to operate CNC machines, automation provides the opportunity to expand production and increase profits.
Automating small lot-size production common in aerospace is challenging. Eliminating setup time becomes the primary goal. Shaving a few seconds or minutes of cycle time when making 20 or 30 parts is insignificant. Reducing setup time by hours and running parts unattended overnight and on weekends generates savings.
Automation in the aerospace world requires palletization, simplified workholding, foolproof tool management, part probing, large tool changers, and usually 4- or 5-axis machining centers. Matsuura’s MAM72 machines (Matsuura Automated Manufacturing, 72 hours in a weekend) are built from the ground up to run unattended.
2) How can a shop implement automation?
Can you afford not to streamline your business and reduce labor costs? If you make parts the same way you did 5 years ago, business expansion and profits will not be in your future. You may not have the work to justify palletized systems today, but another automation strategy is to combine operations.
Machining five sides of a part, along with angled holes and surfaces, is effectively automation compared with flip-flopping the same part through separate operations. Reducing setup time, reducing labor content, and combining operations does not need to be expensive or time-intensive to implement.
Today’s 5-axis machines are simpler, less expensive, and easier to program. You may never do simultaneous 5-axis contours, but you are going to machine all sides of that billet. Machining five sides in one setup improves part accuracy, lowers fixturing costs, and reduces labor expenses.
Matsuura’s smaller, simpler, 5-axis platform features the same hand-built quality, high speed, and sustained precision as its fully automatic machines. The two newest machines in the MX series provide productive, versatile, and affordable unmanned 5-axis production.
3) What applications/processes benefit the most from automation?
High-volume, simple parts are obvious targets for automation. However, in aerospace and defense, manufacturing lot sizes are small, and parts are complex, with close tolerances and excellent surface finish requirements. Combining operations with 5-axis machining centers and unmanned pallet systems is the most efficient way to manage small lots.
4) How do I select the automation solution best suited to my operations?
Consider: floorspace, workpiece size/weight, lot sizes, and machine flexibility.
Machines with smaller footprints and built-in automation reduce expensive floor space requirements. Workpiece size/weight will define the machine size. When machining five sides of a part, look at fixtures and tool lengths. Matsuura or your Matsuura distributor can run a simulation using your solid model to confirm the right machine size.
Machine flexibility can allow shops to satisfy different customers without major retooling. If your shop needs the ability to handle multiple parts, flexibility is vital.
5) What growth do you see for automation in aerospace?
Aerospace manufacturing is not a fad, it is a super trend expected to stay strong for many years to come. Low volume/high-mix is the rule in this industry. Successful shops are already implementing small lot-size automation and these innovative companies are hard to compete against using conventional approaches and machines.
For more info: http://matsuurausa.com
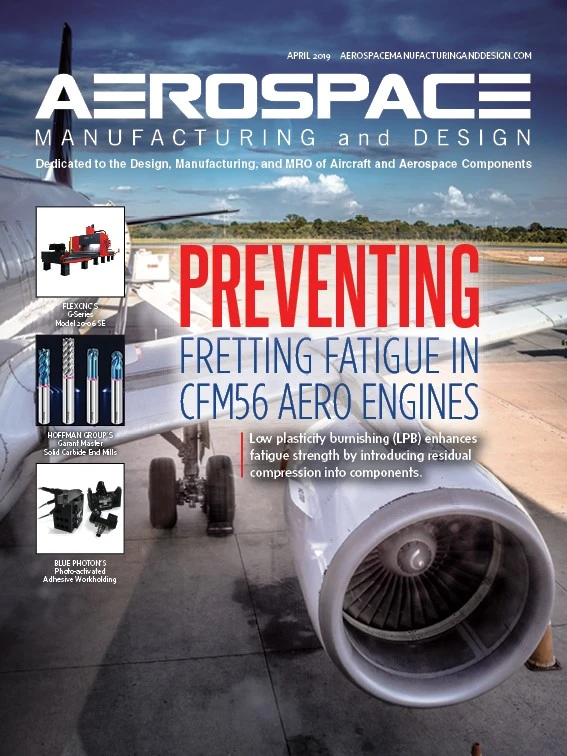
Explore the April 2019 Issue
Check out more from this issue and find your next story to read.
Latest from Aerospace Manufacturing and Design
- Drop in for an interactive webinar on automation in manufacturing
- SW’s wing rib technology for the aerospace industry
- Mach Industries launches Mach Propulsion
- Murata Machinery USA's MT1065EX twin-spindle CNC turning center
- Electra reaches 2,200 pre-orders for its Ultra Short aircraft
- Heule's DL2 tooling for deburring of small bores
- Ralliant to establish global headquarters in North Carolina
- Philatron MIL-DTL-3432 military cables