
Part 2 of 3: Part 1 of the Automation for Beginners series in the January-February issue of Aerospace Manufacturing & Design discussed robotics and end-of-arm tooling. Part 3, scheduled for the April/May issue, will deal with safety, workholding, and ancillary processes.
Infeed is the generic term for bringing incoming parts into an automated cell, and outfeed is the term for bringing finished parts away from the cell. The infeed system also presents the incoming part, oriented so the robot can pick it up. The infeed system needs to locate the parts in a repeatable position or pattern that allows the robot to find and pick the parts. An alternative to having the infeed system locate the part in a specific position is to utilize a vision system, which uses a camera to locate the part.
The challenge is coming up with an infeed/outfeed strategy that will:

- Provide the appropriate number of parts
- Is easy to load up with raw blanks
- Is easy to unload
- Will fit within the space allotted
- Is affordable
Infeed/outfeed strategies
Infeed and outfeed systems can be the same unit, such as a tray which is conveyed into the cell to bring the parts in and then conveyed back out to bring the parts out. Or it can be separate, such as one conveyor for bringing parts in and one conveyor for bringing parts out.

There are several things to consider when choosing the infeed/outfeed method. The first is size – how big should the infeed/outfeed system be? The larger the infeed system, the more incoming parts you can queue up, supporting a longer unattended run time. It is tempting to have a system as large as possible, but there are several things to consider.
First, look at the machining process you are supporting. How long will the tooling last? There is no reason to buy an infeed/outfeed system that holds enough parts to last all day if you are stopping the cell every four hours to change tools. Part quality is also a consideration. There is no reason to purchase a large system if you are checking parts and making frequent offsets. How much room is available? Belt conveyors can get long and may not be the best choice in limited space. Another consideration is flexibility. Will your cell be designed around one part or possibly a family of parts? Flexibility is nice, but it tends to add cost. Finally consider the amount of work required to load up the infeed with parts and to unload the outfeed. Bulk feeders such as a vibratory bowl feeder are great for handling large volumes of parts. Loading them up is as easy as dumping in a bucket of raw blanks, but they can be more expensive than other forms of feeding and are not flexible.
Types of infeed/outfeed systems
Conveyors can come in many forms. A flat-belt powered conveyor is a relatively cheap and flexible method for bringing parts into and out of a cell. By using a set of moveable lane guides, the user can adjust the incoming lanes to handle larger or smaller parts. Conveyors with adjustable lane guides work better for geometric shapes such as cut-up barstock. Blue steel-type roller, non-powered conveyors have a series of small rollers that use gravity to convey parts along the conveyor into or out of a cell. Constructed of spring steel, the conveyor’s sides can be configured with bends to bring parts to a specific position.

Pallet conveyors. Similar to flat-belt conveyors, they convey pallets into and out of the cell. Pallets often have customized pockets to hold the parts in place. They can be large and hold a number of parts or smaller and hold just one part. When holding a large number of parts, they are laid out to allow robots to find parts easily and usually allow the pallets to easily travel back out of the cell. Popular configurations are oval, side-by-side with a transfer, or over/under with the top being the infeed and the bottom the outfeed.
Drawers, or series of drawers can be cost effective. Inside the drawer, similar to a pallet conveyor, is a plate or pallet with customized pockets to hold the parts. With a single layer of drawers, the drawer is opened out to the operator for removing the finished parts and restocking with raw parts, keeping the operator away from the robot. In a stack of drawers, the drawers tend to open on both positions – out to the operator for stocking, and in toward the robot for servicing. Multiple drawers allow the operator to work on one set of drawers while the robot is servicing another.

Vibratory feeders are bulk-type feeders that feed a lot of parts quickly. They can be a bowl type or a hopper, and are easily fed by simply dumping parts in. They tend to be inflexible, and thus are generally used when the cell is designed for one part, or a series of very similar parts.
Chutes are an outfeed-only device, which is simply a quick method for dumping finished parts out of the cell. They are very popular when used in conjunction with an infeed-only device, such as a bowl feeder. A chute will dump the finished parts into an easy-to-change bulk type container located outside of the cell.

Accumulation tables are another outfeed-only device that allows the parts to exit the cell in a more orderly fashion instead of dumping them in a bin, which may not be desirable for parts that are delicate. Parts are conveyed onto a slowly rotating round table. With each rotation, the last row of parts is gently nudged toward the center, making room for the next group of parts.
Methods Machine Tools Inc.
About the author: John Lucier is automation manager at Methods Machine Tools Inc. and can be reached at 978.443.5388 x5426 or jlucier@methodsmachine.com.
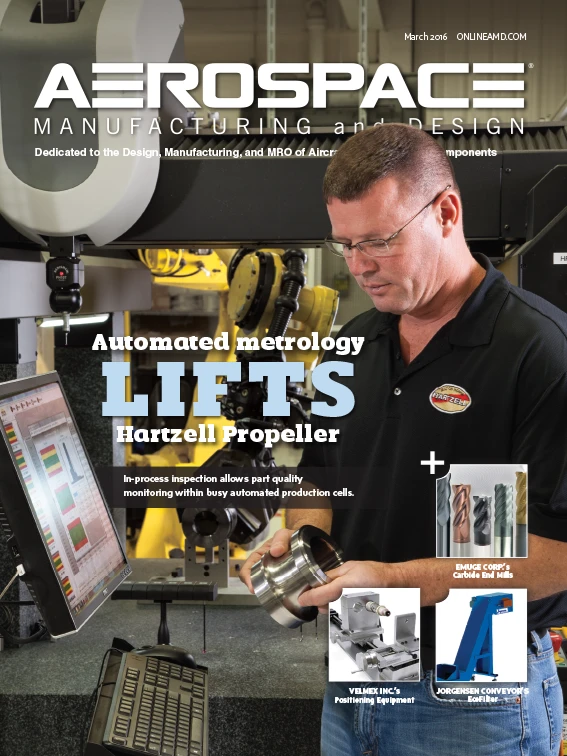
Explore the March 2016 Issue
Check out more from this issue and find your next story to read.
Latest from Aerospace Manufacturing and Design
- Safran Defense & Space opens US defense HQ
- Two miniature absolute encoders join US Digital’s lineup
- Lockheed Martin completes Orion for Artemis II
- Cylinder CMMs for complex symmetrical workpieces
- University of Oklahoma research fuels UAS development
- Motorized vision measuring system
- Everyone's talking tariffs
- Boom Supersonic to launch Symphony engine testing in Colorado