
Drilling system
The B700 Drop Bed machine can drill high-precision features on large and irregularly shaped aerospace components such as landing gear struts. It can also process medium-sized, more uniform workpieces and offers minimal changeover from one to another.
The machine’s capabilities include complex deep-hole machining necessary for aerospace axles, beams, control rods, and components for actuators. Internal contouring is available via an optional servo bottle boring axis.
The machine offers a preloaded drive system, high horsepower, and a controlled in-process feedback system for real-time monitoring. A 250gpm coolant flow reduces heat, evacuates chips, and improves surface finish.
In addition to standard BTA drilling methods, B-series drills are also capable of counter-boring, trepanning, skiving, and roller burnishing processes.
Unisig

Portable display for inductive probes
Developed for the manufacturing shop floor, the TESA Twin-T10 portable display for inductive probes offers ease of operation and a clear and immediate graphical display of data. The unit is suitable for straightness, runout, form, or geometry evaluation during fine adjustments, alignments, or the assembly of mechanical parts. The hemispherical form of the analog scale with 200 segments allows for a clear analog and numeric reading of form variations. Data of measured values can be transferred to a computer for further analysis.
Hexagon Manufacturing Intelligence

Anti-vibration tools
The EWN & EWD Smart Damper precision boring heads with damping system eliminate vibration in deep-hole finish boring. They are designed with the CKB modular boring system for deep-hole boring and for extended-reach milling with both inch- and metric-pilot shell mills and face mills. The Smart Damper solution is equipped with either the EWN analog boring head series, or the digital technology in the EWD series. The EWN heads feature a dial with 0.00050"/div setting accuracy (0.00010" w/Vernier). The EWD heads have a large digital screen that shows adjustments to 0.00005", helping minimize operator errors and removing the need for complicated Vernier markings. The digital display can be reset to zero at the push of a button and has an auto power off function, while the current position of the cutting edge will be shown automatically again due to direct path measurement when the tool is switched on.
The Smart Damper is compatible with Big Kaiser’s modular CK/CKB system, which means that the length of tool combinations can be freely selected up to a maximum of 10x the diameter, and are capable of being run on nearly every major spindle interface.
Big Kaiser Precision Tooling Inc.
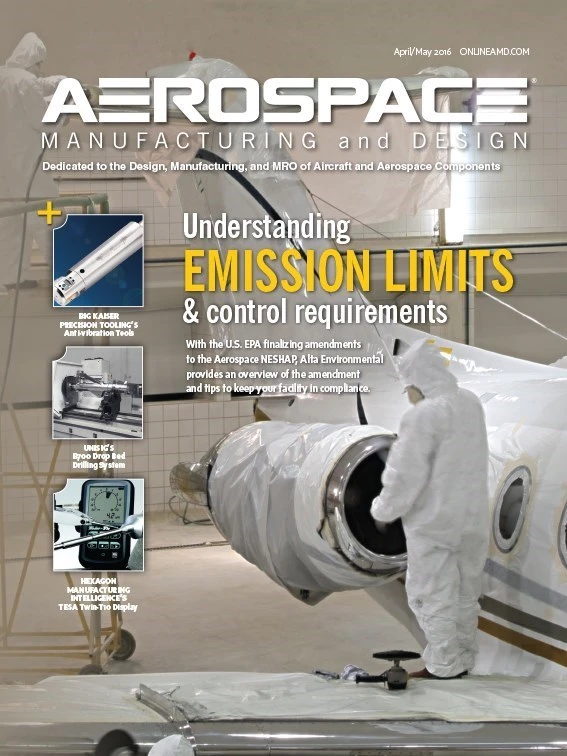
Explore the April May 2016 Issue
Check out more from this issue and find your next story to read.
Latest from Aerospace Manufacturing and Design
- Mach Industries launches Mach Propulsion
- Murata Machinery USA's MT1065EX twin-spindle CNC turning center
- Electra reaches 2,200 pre-orders for its Ultra Short aircraft
- Heule's DL2 tooling for deburring of small bores
- Ralliant to establish global headquarters in North Carolina
- Philatron MIL-DTL-3432 military cables
- Beyond Aero refines its hydrogen-electric light jet
- Americase's advanced protective solutions