
The grinding wheel spins up to speeds, contacts the surface it’s treating, and sparks fly. Why? What’s happening when the wheel or belt makes contact with the workpiece that sends shards of glowing material into the air? How does an abrasive actually cut material to make those sparks?
Creating sparks?
Many manufacturing processes use abrasives to achieve required finishes because of the material used or need for lower cycle times. And, while the visuals are different, sparks coming off of a grinding process are effectively the same thing as chips coming off of a cutting process.
When a cutting tool traverses a piece of material, whether it’s a high-speed steel end mill working along a block of steel or a carbide insert traversing a shaft on a lathe, the material coming off the workpiece can clearly be seen. The cutting tool penetrates the material and removes a curled chip determined by the size of the cutting point or tool area.

New or recently sharpened cutting tools form chips easily, and those chips often have a metallic color. As the tool continues to run, chips get darker – usually a deep blue or black. As the cutting edge of the tool starts to wear and become dull, penetrating the work surface becomes more difficult, requiring more energy to make chips. Duller tools generate more heat through friction, causing the chips to change color.
Increasing frictional heat from dull tools can deteriorate workpiece finish, causing it to lose form or geometric accuracy. At this point the tool must be re-sharpened or replaced.
Abrasives can accomplish the same thing as a conventional cutting tool – making chips and removing material. The sparks coming off the workpiece are the same sorts of curled chips encountered with a lathe or mill, just much smaller.

Fundamental differences
Conventional cutting tools travel at relatively low speeds compared to abrasive cutting tools – Surface speeds are typically used when referring to both types of cutting tools and even if a knee mill’s spindle is running the same revolutions per minute (rpm) as a grinder’s spindle, the surface speed will most often be different (see Table 1).
Most conventional cutting tools have smaller diameters than common precision grinding wheels, so their surface speeds would be a few hundred feet per minute versus several thousand for a larger grinding wheel (see Table 2).
Surface speed directly affects stock removal. The more often a cutting point contacts the material, the quicker the stock comes off or the higher the stock removal rate will be.
An abrasive cutting tool has more cutting points than a conventional tool – For large, indexable conventional tools with replaceable or resettable inserts, the number of cutting points contacting the work is limited to a single point. On a standard end mill tool, the cutter is making contact with the part on a very limited area, usually a single flute. Abrasive cutting tools or grinding wheels make hundreds of cutting point contacts at once, allowing an abrasive tool to better penetrate the work material and work more efficiently.

Abrasives are typically 2x to 6x harder than the steels and carbides used in conventional tools – Modern aerospace materials are lighter, stronger, and more difficult to machine due to wear-resistant properties, so cutting tools need to withstand those properties. Difficult materials can cause excessive and premature wear on conventional tools, but today’s abrasives are designed to hold up to these materials, effectively making chips, removing stock, and machining newer materials (see Table 3).
Depth of cut (DOC) – Abrasives in precision grinding applications may achieve 0.005" or smaller depths of, where cutters can reach 0.25" cutting depths. Although some specialized grinding operations can hog material, conventional cutting tools hold the advantage over abrasives in DOC. The tradeoff is conventional tools taking large, deep cuts leave very poor, rough surface finishes. Taking the deepest cut possible with an abrasive cutting tool, the finish will generally be better because more cutting points are in contact with the work.

Abrasives also offer very high material removal rates from optimally applying many more cutting points to material in the contact zone. Modern grinding wheels use advanced grains and bonds which improve stock removal, reduce cycle time, and/or extend wheel life.

Also, traditional cutting tools with inserts still need to be taken out of production to have inserts indexed or sharpened. Abrasive cutting tools or grinding wheels can self-sharpen, so they are only briefly out of production for occasional truing or dressing to restore a profile or face condition.
Making chips
As an abrasive grain contacts a workpiece surface, it immediately meets resistance. The work to be ground tries to prevent the abrasive from penetrating the material and making a chip. To overcome that resistance, the system must generate sufficient force, and the machine operator must apply downward forces to make the abrasive penetrate the work surface, or sliding or friction will result.

The wheel speed and machine horsepower must also be sufficient to cause the abrasive to create a chip. Tougher materials require higher horsepower – the higher the tangential forces, the higher the horsepower needed.
The battle occurs where the abrasive meets the material. The force applied by the grain trying to create a chip is fighting against the resistance of the material. If the applied forces are equal to or less than the resistant forces, grinding is minimal or non-existent, resulting in a lot of friction and heat, loss of finish and accuracy, and metallurgical damage.
However, if applied force exceeds resistant force, chips form more readily and grinding occurs. If the force applied by the abrasive is too high, the grain and bond holding it together may break down and cause premature wear of the abrasive cutting tool. To avoid this, pay attention and find the right balance between required grinding forces and chip size.
As the abrasive rubs against the workpiece, there’s a natural tendency for the abrasive to dull. When the abrasive begins to lose its sharpness, it’s more difficult to penetrate the work surface and forces intensify. This condition can accelerate abrasives dulling, increase forces, deteriorate finish, diminish accuracy, and cause metallurgical damage (burn). Most grinding problems can be traced to a dull abrasive remaining in the wheel, belt, or disc too long.

The most efficient grinding (or sanding) occurs when abrasives are sharp so it’s important to:
- Use abrasives with more mild/friable grains that fracture readily, don’t easily dull
- Use appropriate bond type and grade (hardness) to release abrasive grain before dulling
- Use coolant, other agent to reduce friction, slow dulling process
- Physically remove dulled abrasives before problems occur
- Ensure operational factors are appropriate to optimize abrasive; speeds, feeds, etc. set to maximize performance, life
- Abrasive products are made with a variety of abrasives and bonds so the products can be matched to the grinding forces and conditions encountered in a given operation.
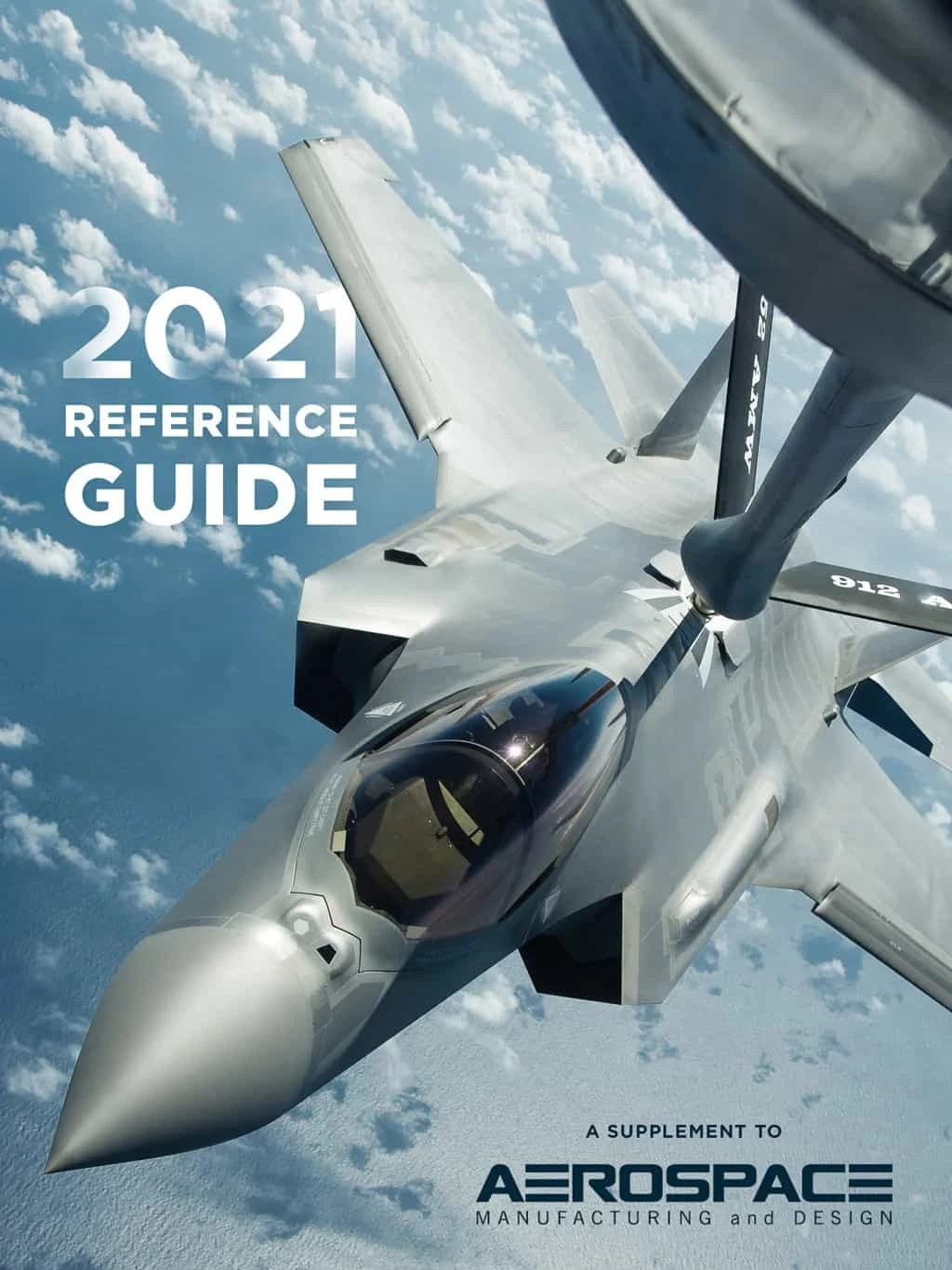
Explore the AMD Reference Guide 2021 Issue
Check out more from this issue and find your next story to read.
Latest from Aerospace Manufacturing and Design
- Ohio creates Youngstown Innovation Hub for Aerospace and Defense
- Tormach’s Chip Conveyor Kit for the 1500MX CNC Mill
- How to Reduce First Article Inspection Creation Time by 70% to 90% with DISCUS Software
- Jackson Square Aviation orders 50 Airbus A320neo aircraft
- Beckhoff's motion control automation solutions
- #40 - Lunch & Learn with Fagor Automation
- Air Methods to purchase up to 28 Bell helicopters
- AMADA's laser marking capabilities