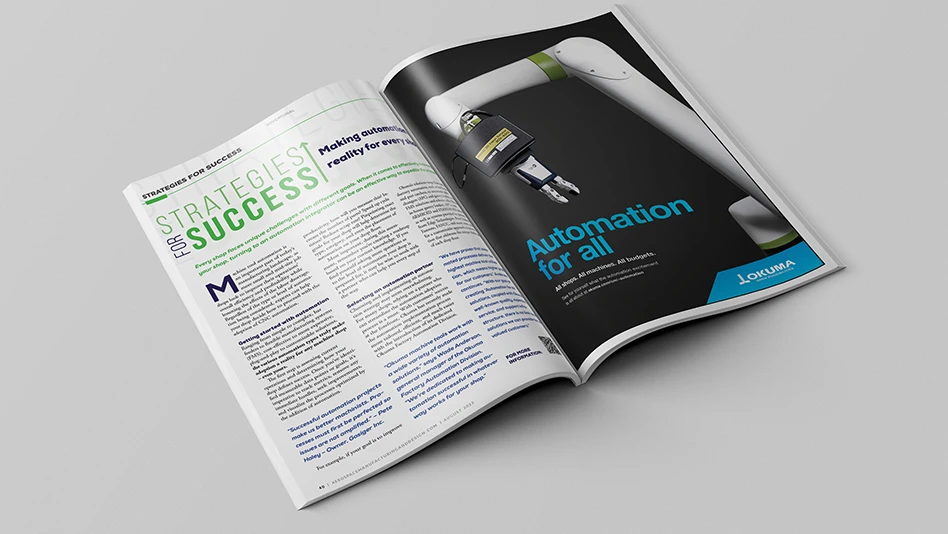
Machine tool automation is an important part of today’s manufacturing landscape, as more small and mid-size job shops look to improve their operations’ overall efficiency and profitability while lessening the effects of the labor shortage. Regardless of the type or level of automation being considered, experts can help your shop decide how to proceed with the adoption of CNC automation.
Getting started with automation
Ranging from simple to complex, bar feeders to flexible manufacturing systems (FMS), cost-effective to more expensive, plug-and-play to customizable solutions, the various automation types truly make adoption a reality for any machine shop – even yours.
The first step is assessing current operations and determining how your shop defines success. Once you’ve identified measurable data points or goals, it’s imperative to track metrics, remove any immediate hurdles, seek improvements, and visualize the processes optimized by the addition of automation.
“Successful automation projects make us better machinists. Processes must first be perfected so issues are not amplified.” – Pete Haley – Owner, Gosiger Inc.
For example, if your goal is to improve productivity, how will you measure this? Increase the number of parts? Speed up cycle times? Reduce scrap rate? Pinpointing exact goals for your shop will help determine the type, category, and even the placement of automation on your shop floor.
Most important, during this assessment, remember you’re creating a roadmap based on your current knowledge. If you find yourself asking more questions as to the level of automation your shop is prepared for, it may be wise to work with a partner who can help you every step of the way.
Selecting an automation partner
Choosing and implementing an automation strategy may seem overwhelming. For many shops, relying on a partner who can streamline the automation adoption process is a must. With customers’ success at the forefront, Okuma has recently made the automation implementation process more tailored, efficient, and much easier with the introduction of its dedicated Okuma Factory Automation Division.
“Okuma machine tools work with a wide variety of automation solutions,” says Wade Anderson, general manager of the Okuma Factory Automation Division. “We’re dedicated to making automation successful in whatever way works for your shop.”
Okuma’s solutions range from introductory automation, such as bar feeders and part catchers, to automatic pallet changers (APC) and gantry loaders, to full FMS solutions and robotic cells. Okuma’s in-house gantry loaders, APCs, and ARMROID and STANDROID robotics, as well as systems provided by partners from Edge Technologies, Bucci Industries, Fastems, FANUC, and many more, allow for a customizable approach to automation that addresses the unique challenges of each shop floor.
“We have proven that automated processes deliver the highest machine tool utilization, which means higher profits for our customers,” Anderson continues. “With our goal of creating ‘Automation for All’ solutions, coupled with Okuma’s well-known quality, expertise, service, and support infrastructure, there is no limit to the solutions we can provide for our valued customers.”
Get curated news on YOUR industry.
Enter your email to receive our newsletters.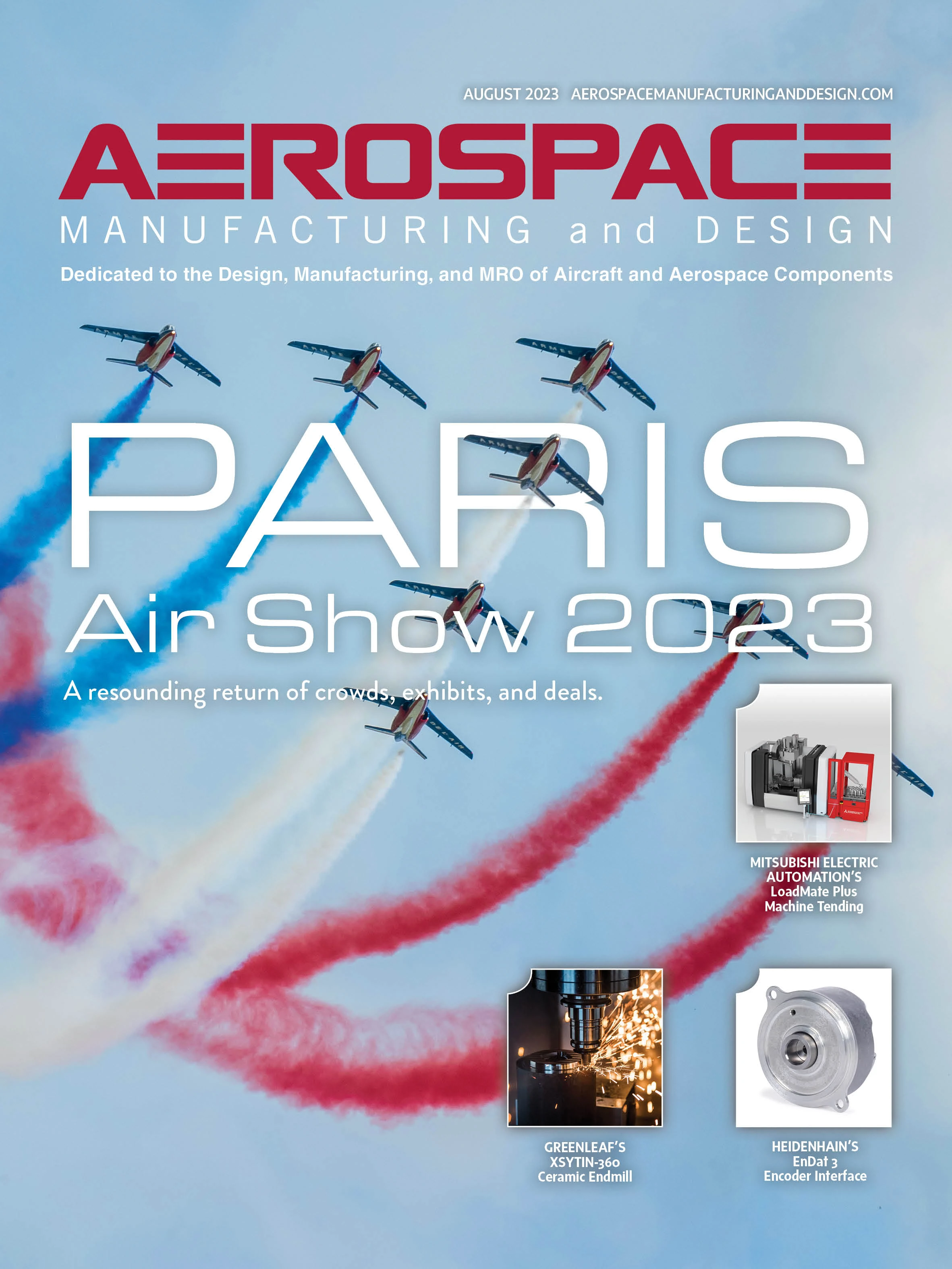
Explore the August 2023 Issue
Check out more from this issue and find your next story to read.
Latest from Aerospace Manufacturing and Design
- GE Aerospace secures Air Force engine contract
- Thomson Industries' online sizing and selection tool
- #53 - Manufacturing Matters - 2024 Leaders in Manufacturing Roundtable
- Join us for insights on one of the hottest topics in manufacturing!
- You can still register for March’s Manufacturing Lunch + Learn!
- Ohio creates Youngstown Innovation Hub for Aerospace and Defense
- Tormach’s Chip Conveyor Kit for the 1500MX CNC Mill
- How to Reduce First Article Inspection Creation Time by 70% to 90% with DISCUS Software