
Aerospace manufacturing faces several challenges impacting traditional machining operations. Demand for more complex, higher-precision parts, ship sets instead of long-running part contracts, cost and lead time reductions, and a shortage of skilled operators make it essential to re-think production of machined components.
The manufacturing industry is addressing some of these issues with process changes based on artificial intelligence (AI), machine learning (ML), advanced software, automation, and robotics, while multi-axis capabilities enable greater precision and part complexity.
However, more significant strides are possible. The key is adopting a holistic approach to CNC machining that simultaneously targets various aerospace manufacturing challenges.
MX – Machining Transformation – a concept developed by DMG MORI, is founded on process integration, automation solutions, digital transformation, and green transformation.
Aerospace manufacturing evolves from conventional to cutting-edge
Traditional machining involves multiple pieces of equipment performing sequential steps that can include turning, milling, gear cutting, measuring, and additive manufacturing. Typically, there’s substantial work in progress (WIP) as these parts travel across various types of equipment, increasing overhead and decreasing efficiency and return on investment (ROI). Each machine requires significant setup time as parts change.
The MX approach presents a groundbreaking solution by integrating various functions within a single machining center, operated by one person and programmed centrally. The benefits are reduced staffing requirements, decreased employee time on routine tasks, and increased opportunity for staff to engage in value-added operations. Yet, the advantages extend further. Centralizing all functions enhances machine utilization while reducing overall energy consumption and carbon emissions compared to running multiple machines. Support functions such as maintenance and testing are also streamlined through process integration.
DMG MORI has taken the lead in supporting customers with MX by offering various equipment options that feature process integration. For instance, Ouroboros Space and Defense, a U.S. company specializing in machining high-precision components for rocket engines, has taken the first steps in its machining transformation journey. Ouroboros uses several DMG MORI products including the DMU 95 monoBLOCK for 5-axis milling and the NTX 2000 for integrated turning and milling, to achieve unprecedented part accuracy and reduce lead times.
To support customers, DMG MORI has a team of aerospace experts capable of delivering a wide range of services, from feasibility analysis to equipment installation.
Extending process integration
The latest automation and digitization technologies further expand the benefits of MX. Automating machine operation can reduce staffing needs and allow lights-out machining. The major benefits of automation include reduced idle time, increased productivity and spindle hours, and faster fulfillment. Digital tools such as DMG MORI’s CELOS DYNAMICpost allow full digital twin integration instead of actual test cuts and help optimize the machining process. Digital monitoring via DMG MORI Messenger provides feedback and outputs, including data on machine uptime, remote diagnostics, and easy-to-read, exportable capability charts. Meanwhile, my DMG MORI serves as a remote service portal simplifying the service process at no cost to customers.
MX supports sustainability through energy and carbon reductions that ultimately increase customer profitability. MX eliminates unnecessary WIP and intermediate inventory to conserve resources.
Find out how MX can elevate aerospace machining by enhancing productivity, streamlining workflows, addressing staffing shortages, and promoting energy efficiency and emissions reduction.
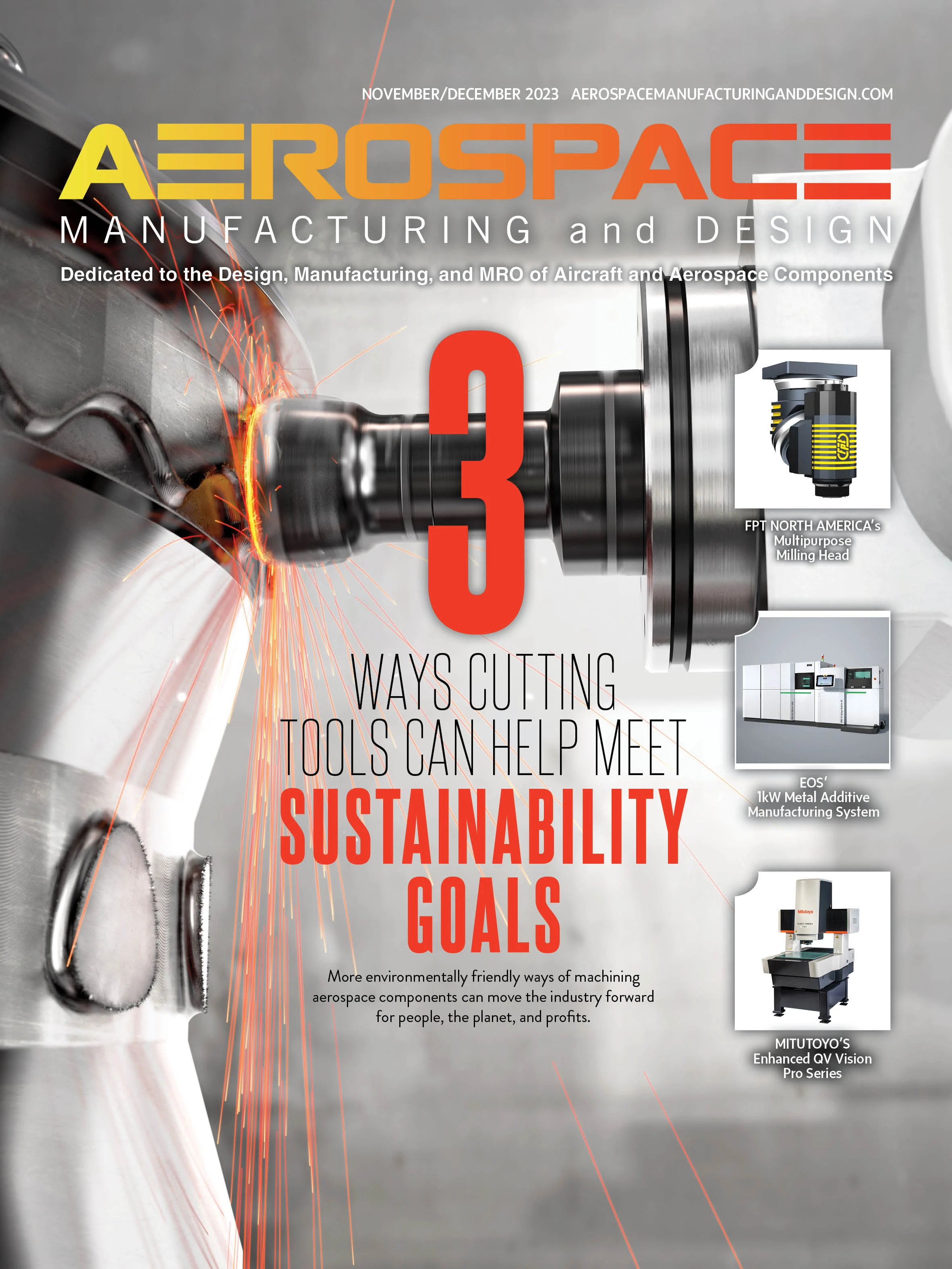
Explore the November December 2023 Issue
Check out more from this issue and find your next story to read.
Latest from Aerospace Manufacturing and Design
- 2024 Favorites: #9 Article – 5 tips for upskilling your aerospace machinists
- 2024 Favorites: #9 News – Siemens acquires Altair Engineering
- 2024 Favorites: #10 Article – How 3D-printed aviation parts can accelerate return to air
- 2024 Favorites: #10 News – Boom Supersonic completes Overture Superfactory
- OMIC R&D hosts Supporting Women in Manufacturing Day 2024
- 4D Technology's AccuFiz SWIR interferometer
- Seventh Lockheed Martin-built GPS III satellite launches
- KYOCERA AVX's CR Series high-power chip resistor