
Operating and supporting an in-house machine shop can be a substantial benefit to a metal fabricator specializing in aerospace maintenance equipment. As an alternative to sub-contracting out machine work, an in-house machine shop streamlines the ability to address customers’ needs. Additionally, project bids and lead times can be kept more competitive, adding to the shop’s overall capacity.
Fabricators have better control of the finished product with an in-house machine shop. They can be more accurate and precise, leading to greater productivity. Fabricators can fine-tune tolerance requirements, ensuring the customer is getting the highest quality part without depending on a third party to maintain standards.
Finally, there are the cost-cutting benefits a fabricator can offer its customers. Now, more than ever, budgets are tightening. Having a machine shop under the roof allows fabricators to be more aggressive in bidding.
Capabilities
To maintain an in-house machine shop, fabricators need to be very nimble, reacting quickly to customer needs. Many aerospace-focused custom metal fabrication shops are not manufacturing a single product line. The same part with the same specifications is not being machined every day, so the ability to develop practical solutions on a regular basis is key.
In a custom fabrication shop, capabilities are more important than capacity. However, one can’t say definitively that this is the case in any shop. While some buyers are looking for capacity, more capabilities can generate shorter lead times for custom fabricators in aerospace.
One way a machine shop can grow its capabilities is through equipment. Machine shops that support a fabrication facility should always be evaluating how to efficiently produce more in-demand products. Fabrication shops do not want to tell the customer that something cannot be delivered in a reasonable time frame, or worse, cannot be done at all.
Staying ahead
Understanding the aerospace market and finding ways to take advantage of market demand are critical. A waterjet can make sense for an in-house machine shop. However, this is predicated on the kind of fabrication work the shop is doing. Many companies use plasma or laser cutters because it makes more sense for the work they are performing. As a waterjet cuts out shapes without applying heat, it consistently produces the same results.
If a fabricator has higher minimum requirements regarding a production rate, a plasma cutter may be ideal as it operates at a faster pace. However, if a fabricator is looking for applications with more versatility performing one-off custom work and has the space and funds for the investment, a waterjet may be the optimal choice.
Regardless of equipment specifics, it’s critical to stay on top of the technology available. There could always be a breakthrough in waterjet or plasma cutting technology on the horizon, allowing the fabricator to improve lead times and reduce costs in the long run.
Part of the challenge is keeping an eye on the product mix. For example, if a fabricator takes on a large job that is 90% machining, it will significantly tie up resources inside the machine shop. Depending on what other jobs may be on the way, the shop may need to add capacity.
On the other side of the equation, a fabricator needs to be sure that the machine shop is not experiencing too much downtime. It’s a considerable financial investment to bring a machine shop online and maintain it, so it can’t be sitting idle during peak production hours.

Personnel
Another critical factor in running a successful in-house machine shop is employee skills. For example, it is important to have an optimal mix of machinists and machine operators. A machine operator runs the parts through and operates the equipment. However, a machinist has expertise in programming the equipment, ensuring it performs as expected. Machine operators operate and perform setups. A machinist creates and edits programs. And with most professions, advanced machinists can do it more effectively and efficiently.
In some scenarios, it may make sense to add a dedicated offline programmer to the mix. However, if machinists are creating their own program, and there aren’t long dedicated runs of products to be manufactured, it doesn’t always make financial sense to have an offline programmer. It all depends on the needs of the fabricator. As a fabrication shop grows, the optimal mix of personnel may need to be tweaked to maximize production capabilities and reduce costs. It will depend on the products being manufactured. For example, if a fabricator is running a machine shop that doesn’t need to edit programs on the fly, it may work best with multiple machine operators, one machinist, and one offline programmer.
Investment
With the significant monetary investment that must be made in skilled labor, equipment, and space to operate an in-house machine shop, it is critical to get the most out of it. However, between waste reduction, improved quality control, and additional capabilities, the benefits can outweigh the associated costs.
WB Industries
https://w-bindustries.com
Get curated news on YOUR industry.
Enter your email to receive our newsletters.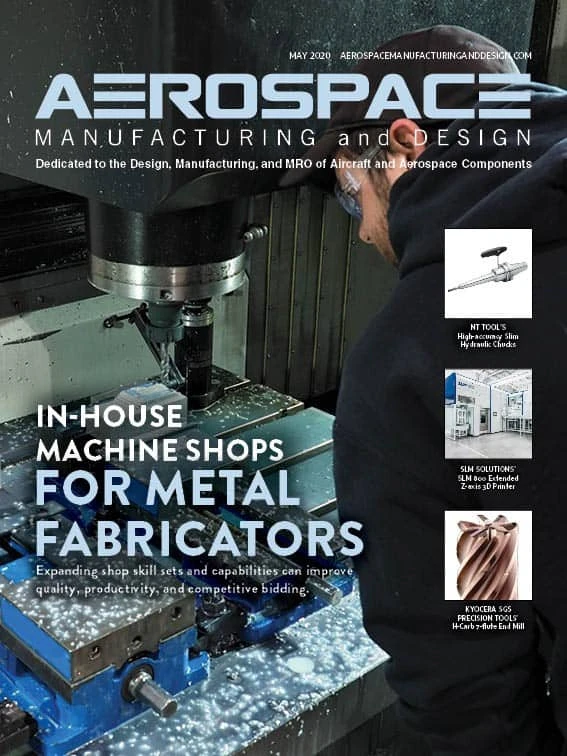
Explore the May 2020 Issue
Check out more from this issue and find your next story to read.
Latest from Aerospace Manufacturing and Design
- Ralliant to establish global headquarters in North Carolina
- Philatron MIL-DTL-3432 military cables
- Beyond Aero refines its hydrogen-electric light jet
- Americase's advanced protective solutions
- Social media - what are your thoughts
- GE Aerospace secures Air Force engine contract
- Thomson Industries' online sizing and selection tool
- #53 - Manufacturing Matters - 2024 Leaders in Manufacturing Roundtable