
Materials grown and self-assembled by living cells could produce advanced specialty paints for corrosion protection; lightweight, high performance optics for sensing on drones; and part production and repair systems for expeditionary forces through simpler, greener, and rapid adaptation.
The Army Research Laboratory (ARL), Lockheed Martin, and Army scientists will develop rapid prototyping methods using bio-production and self-assembly to create the building blocks of novel materials for defense optical technology and protective coatings. The research is intended to advance the use of biological systems for on-demand synthesis of materials and embedding biological products into materials.
“Cells efficiently create all sorts of materials, such as a spider’s silk or a butterfly’s iridescent wings. We want to harness nature’s process to better protect people,” says Melissa Rhoads, senior research manager and Lockheed Martin lead for the project. “Biodesign exists today, but it doesn’t exist at the scale and to the quality of defense standards.”
Telescope lenses filter out unwanted light to get a clearer image. However, a squid lens can filter and focus light in compact package due to molecule-based design and varied refractive index.
“Harnessing the power of self-assembling materials is sustainable, affordable, and can be much faster to produce than artificial methods,” Rhoads says.
“The functional coatings work proposed in the agreement for electro-optic and electromagnetic technology has potential impact on conformal antenna work in automotive, aerospace, and drone technology that is under development for security, product delivery, and other applications,” says Dr. James Sumner, chief of the ARL’s biotechnology branch.
The research could lead to production of toxic-free paint with anti-fungal/anti-mold protection and biomedical applications such as reducing the size, weight, and cost of diagnostic and surgical devices.
The $10 million, 5-year agreement uses the name Self-Assembly of Nanostructures for Tunable Materials and will leverage the Army’s Open Campus model to enable collaboration between university, small-business, Army, and Lockheed Martin scientists and engineers.
“ARL is providing the synthetic biology expertise, and facilities needed to gain an understanding of biological assembly through combined efforts in genetic control, material-based screening, and modeling. Lockheed Martin is bringing design and experience in manufacturing and systems expertise through interdisciplinary scientists across its many business units,” says Dr. Dimitra Stratis-Cullum, ARL research chemist and an Essential Research Program manager.
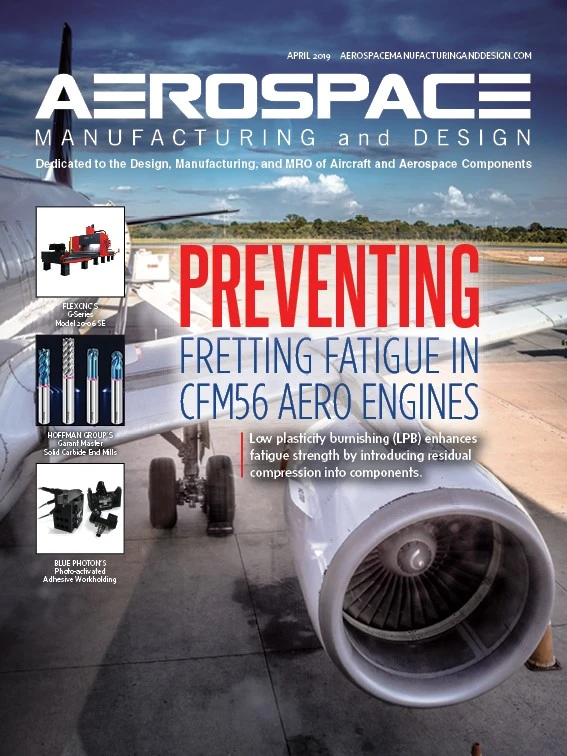
Explore the April 2019 Issue
Check out more from this issue and find your next story to read.
Latest from Aerospace Manufacturing and Design
- 2024 Favorites: #8 Article – Beyond uptime
- 2024 Favorites: #8 News – NASA, Lockheed Martin reveal X-59
- 2024 Favorites: #9 Article – 5 tips for upskilling your aerospace machinists
- 2024 Favorites: #9 News – Siemens acquires Altair Engineering
- 2024 Favorites: #10 Article – How 3D-printed aviation parts can accelerate return to air
- 2024 Favorites: #10 News – Boom Supersonic completes Overture Superfactory
- OMIC R&D hosts Supporting Women in Manufacturing Day 2024
- 4D Technology's AccuFiz SWIR interferometer