
The relentless drive for energy efficiency in power generation and propulsion places immense value on the development of high-performance materials. Turbine engine efficiency and reduction in carbon emissions are directly related to engine operating temperature. With increasing temperatures, materials start to change in shape or size – a process known as creep – which eventually limits the materials’ performance.
An article appearing in Nature Communications shares results of the study “Phase Transformation Strengthening of High-Temperature Superalloys,”(1) led by The Ohio State University’s Materials Science and Engineering Professor Michael Mills; faculty colleagues Wolfgang Windl, Hamish Fraser, and David McComb; and graduate students Tim Smith, Bryan Esser, and Nik Antolin.
“Increased performance in aircraft engines and land-based power generators require the development of a new generation of high-temperature structural materials that are resistant to creep,” Mills says.
This study addresses a deficit in the quantitative, comprehensive understanding of deformation mechanisms for various alloy compositions in high-temperature, high-stress conditions in advanced engine designs.
The quantitative analysis combines atomic-resolution imaging with density functional theory (DFT) calculations, led by experts such as Robert Williams at Ohio State’s Center for Electron Microscopy and Analysis (CEMAS) and Anna Carlsson of FEI/Thermo Fisher Scientific. This coupled approach resulted in the discovery of a high-temperature strengthening mechanism, which the research team refers to as phase transformation strengthening.
“Through advanced imaging and DFT calculations we found that increasing the concentrations of the elements titanium, tantalum, and niobium in superalloys inhibits the formation of high temperature deformation twins significantly improving the alloys’ high temperature capabilities,” Mills says.
“Research such as this perfectly illustrates the power of CEMAS to help drive discovery in new materials and processes,” says CEMAS Director David McComb.
According to Mills, this mechanism may be further manipulated through alloying and processing to further improve the high-temperature properties of next-generation superalloys for critical structural applications.
The study also benefitted from industry insight provided by GE Aviation Lead Materials Engineer Andrew Wessman.
The Ohio State University Center for Electron Microscopy & Analysis
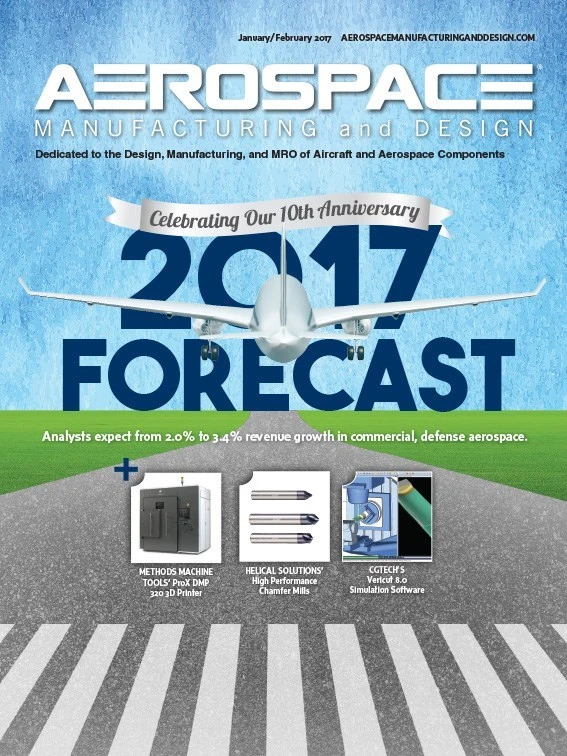
Explore the January February 2017 Issue
Check out more from this issue and find your next story to read.
Latest from Aerospace Manufacturing and Design
- Revitalizing the Defense Maritime Industrial Base with Blue Forge Alliance
- Safran Defense & Space opens US defense HQ
- Two miniature absolute encoders join US Digital’s lineup
- Lockheed Martin completes Orion for Artemis II
- Cylinder CMMs for complex symmetrical workpieces
- University of Oklahoma research fuels UAS development
- Motorized vision measuring system
- Everyone's talking tariffs