
Electric aircraft and the promise of autonomous air taxis are advancing quickly. Aerospace original equipment manufacturers (OEMs) and their supply chain partners face intense pressure to be first to market with a safe and reliable product. Many practices that worked 20 years ago no longer suffice due to today’s complexities and challenges. Therefore, OEMs are rethinking their approach to product development, which begins with systems engineering. As companies explore the tradeoffs between hundreds of design configurations and prepare for the challenges of certifying electric aircraft, systems engineering is critical to their success.
Companies often struggle with the complexity of autonomous systems, flight controls, and system integration when relying on document-centric processes for systems engineering. Requirements might be in one database, spreadsheet, or document while system modeling might be in Microsoft Visio or SysML. System safety analysis might be spread across a variety of tools. Verification and test data often end up in yet another spreadsheet. Everything is disconnected, often occurring in isolated work silos. In the rapidly evolving area of future-forward aircraft, as new requirements and system architectures are established, these document-centric approaches don’t scale, and it’s nearly impossible to manage traceability when trying to address thousands of systems interactions.
A digitalized approach that connects all aspects of concept, design, manufacturing, and maintenance is the answer.
MBSE in electric aircraft
Companies leading the way in developing electric aircraft realize the importance of model-based systems engineering (MBSE), which is growing in popularity because of its disciplined approach to systems engineering. It brings a new level of integration and efficiency to complex systems and processes across many multi-domain challenges future-forward aircraft manufacturers confront. When companies move to MBSE they collaborate more easily across domains and throughout the entire supply chain.
The MBSE approach is more than functional or logical modeling. It serves as the digital backbone that unites engineering, manufacturing, supply chain, and program management activities to create a comprehensive digital thread – a composite of interwoven and interconnected digital strands, creating an ecosystem for program execution excellence.

MBSE can satisfy electric aircraft manufacturers with:
Support for the entire lifecycle of product development – MBSE allows teams to troubleshoot, explore, and pinpoint the ideal outcome. Because of the MBSE digital thread, what happens in one domain gets shared throughout the entire product lifecycle. For example, the electric motor is different from the traditional turbine engine. The center of gravity is in a different location and has a different weight. Before the engine is installed on an aircraft, engineers must consider the weight and balance trade-offs, and how they will impact downstream activities.

Another challenge is to determine where to place the batteries as they add significant weight to an all-electric aircraft. Using MBSE allows teams to purposefully design and build around a structure that includes increased electrification. Batteries, and more importantly power density, are key design challenges in an electric aircraft (Figure 1, below). As these challenges are met, product risk is lowered and certification becomes easier.
Certification – Increasingly, MBSE is gaining widespread use as companies seek to certify more complex and highly integrated systems. The Federal Aviation Agency (FAA), the European Union Aviation Safety Agency (EASA), along with other regulatory agencies are requiring more organized systems engineering for OEMs and their partners. The U.S. Department of Defense (DOD) also recognizes the need for MBSE to communicate requirements more effectively to the OEMs and have a process in place to check that all requirements have been satisfied. A robust MBSE digital thread enables companies to accelerate their product development and certification processes, while improving communications with various regulatory agencies.
And it’s not just an electric aircraft’s propulsion system that’s different, it’s the entire vehicle configuration. There are FAA rules for fixed-wing aircraft, rotorcraft, and tilt-rotors – all adding another layer of complexity to the certification requirements – which makes MBSE critical in aircraft certification.
Managing the product architecture – Product architecture needs to ensure OEMs are managing all product interfaces, including the electrical system, flight control system, and propulsion system. All these functions represent interfaces that must be managed. With MBSE, teams have a good process for managing requirements and tying together the project’s models. This also gives the OEM a good verification plan. Engineers can verify at the component level, the subsystem level, and at the aircraft level knowing all requirements have been satisfied. An MBSE digital thread connects requirements to model, design, analysis, and ultimately, to verification processes and artifacts. Automating these data hand-offs with a digital thread provides full traceability. Other key areas include thermal management and addressing electromagnetic interference.
Embracing digital transformation
An MBSE digital thread connects multiple domains within the digital enterprise. In addition to an MBSE digital thread, there are digital threads from each essential domain. Through the tight integration of an MBSE digital thread, teams from all domains can test and push the boundaries without jeopardizing downstream work or timelines. When companies transition from system modeling to using a digital thread, they can use any system modeling tool and connect to the entire data and information lifecycle to certify, deliver, and maintain new products. From the conceptual design through to service, all pertinent data needs to be easily accessible by a comprehensive digital thread, and it should be built on a flexible and open ecosystem that can accommodate various tools for requirements and system modeling while ensuring customers can carry their architecture and legacy tools forward as they develop their MBSE capability.
Making the move
Many in the industry believe requirements engineering or system modeling is MBSE. To some extent this is true, but MBSE is also system safety, software engineering, verification – all linked closely to product design, optimization, manufacturing, and product support. Aerospace companies involved in electric aircraft are implementing the Siemens MBSE digital thread to accelerate product development and be first to market. They are moving faster than the competition and are meeting program budget guidelines. They are reducing the risk of design changes. When there is a change, they have a better understanding of how to make that change and how to deal with the ripple effects that could follow. MBSE is the right choice to lead our industry forward.
Siemens Digital Industries Software
About the author: Dale Tutt is the vice president of aerospace and defense industry for Siemens Digital Industries Software. He can be reached at dale.tutt@siemens.com.
Get curated news on YOUR industry.
Enter your email to receive our newsletters.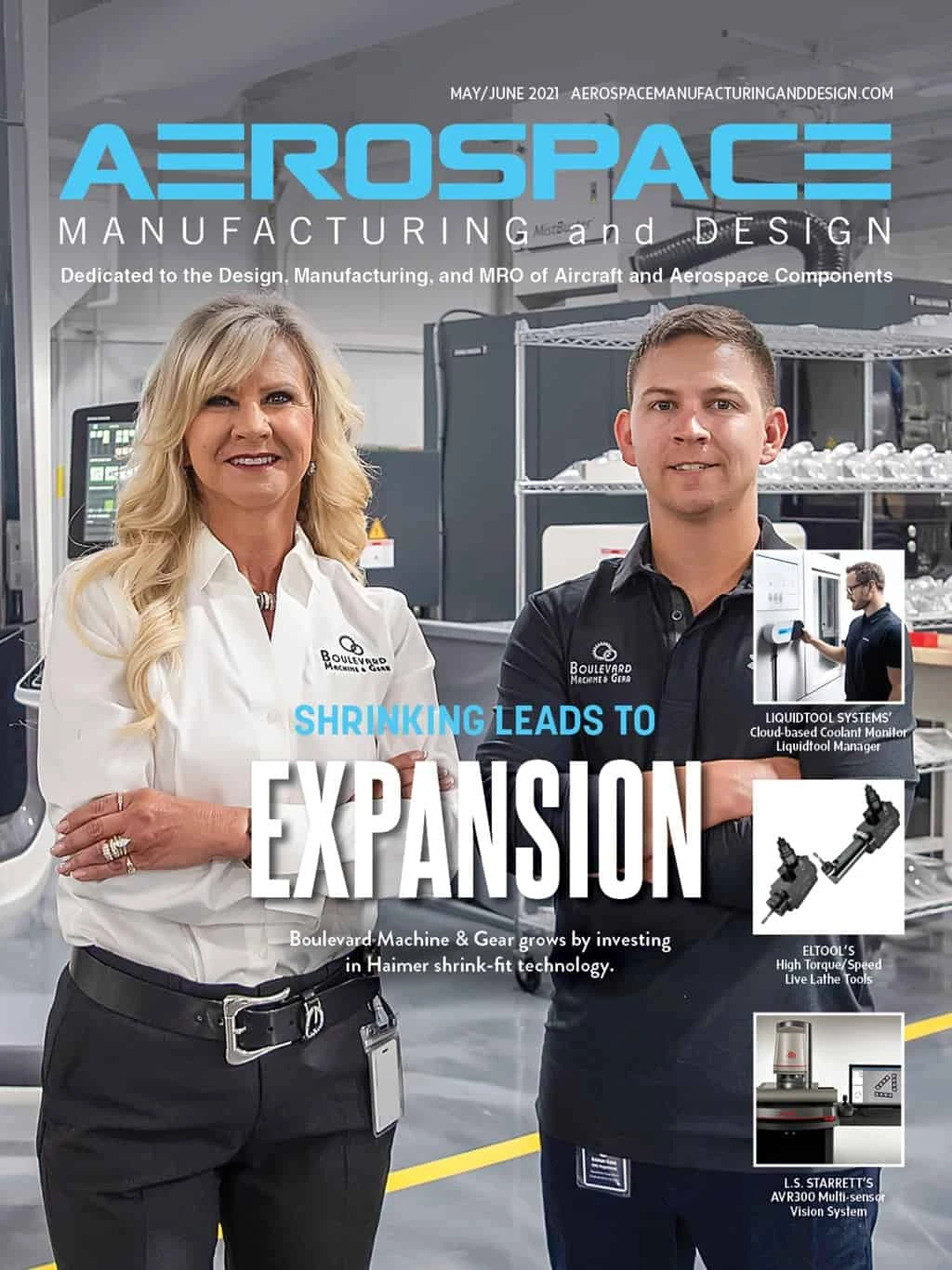
Explore the May June 2021 Issue
Check out more from this issue and find your next story to read.
Latest from Aerospace Manufacturing and Design
- Address the challenges of machining high-temperature aerospace components
- Elevate your manufacturing operations with April’s Manufacturing Lunch + Learn
- America Makes announces IMPACT 3.0 Project Call worth $4.5M
- Updated parting and grooving geometries from Sandvik Coromant
- AIX showcases the future of air travel
- Sunnen Products' PGE-6000 gage
- #41 Lunch + Learn Podcast - SMW Autoblok
- Revolutionizing aircraft design without sacrificing sustainability