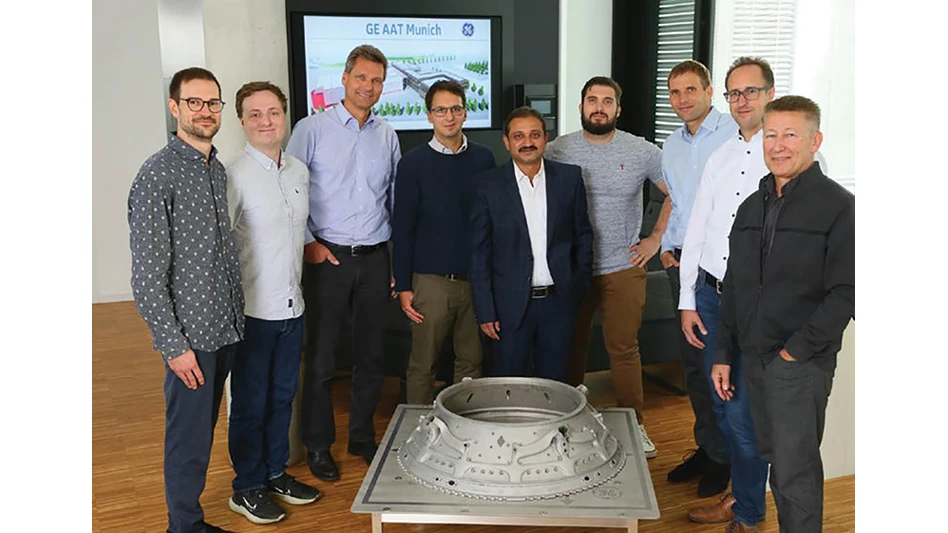
GE Aerospace

GE Aerospace Advanced Technology (GE AAT) Munich team is designing and manufacturing a large-scale metal additive manufacturing (AM) component for the EU-funded MOnACO project – the Advanced Additive Integrated Turbine Center Frame (TCF) casing. This includes the design and production of coupons and critical parts, validation and qualification, and the final delivery of the full-sized metal 3D-printed casing.
After almost six years in research, development, and engineering, the large-format TCF casing design using GE Additive’s Direct Metal Laser Melting (DMLM) technology in nickel alloy 718 was recently unveiled by the consortium. The TCF casing is one of the largest additively manufactured parts made for the aerospace industry.
The additively manufactured TCF casing is designed for narrow-body jet engines where the part’s approximately 1m or more in diameter. Having this single-piece design solution to produce this kind of large format engine hardware with reduced cost, weight, and manufacturing lead time delivers a competitive business advantage.
“We wanted to reduce the weight of the part by 25% but also improve the pressure losses of the secondary air flow as well as a strong reduction in part count to improve maintenance,” says Dr. Günter Wilfert, GE AAT Munich’s technology and operations manager. “The team can be proud of the results. With the final print of the full casing, they proved the values. Those targets were achieved and surpassed. We reduced the weight by ~30% in the end. The team also reduced the manufacturing lead time from nine months to two-and-a-half months, a near 75% reduction. More than 150 separate parts making up a conventional turbine center frame casing have been consolidated into one single-piece design.”
To ensure all the engineering requirements were met, including a performance benefit of 0.2% in specific fuel consumption, the design was reviewed by experts from across the team for Technology Readiness Level (TRL) and Manufacturing Readiness Level 4 (MRL4), and multiple manufacturing trials were performed to meet hardware quality and incorporate the manufacturability of MRL4.
Outside the environmental, performance, weight, cost, and waste reduction benefits of this new part, the biggest impact will be reducing supply chain disruption in industries facing challenges with conventional casting.
The TCF, an inherent component of modern, turbofan aircraft engines, serves as a duct for the hot gas flowing from the high-pressure turbine into the low-pressure turbine. Conventionally, TCFs are manufactured by casting and/or forging, followed by additional machining steps.
Due to stringent requirements on airworthy hardware in the aerospace industry, approved vendors for casting and forging parts are very limited. This creates long lead times and high costs. These challenges, and the fact that a TCF isn’t a rotating part, made it an ideal candidate for AM.
The new AM design solution on engine frames isn’t limited to TCF for future engines; it can be leveraged for existing and legacy engine center frames. The proposed design features can also be transferred and/or scaled to turbine rear frames (TRF), low pressure turbine casings, and turbine mid frames (TMF).
“People already want to know how this part has been made and how the design and technology could translate to their industries,” says Ashish Sharma, an advanced lead engineer on the GE AAT team. “Our strategy all along was to make sure the component design meets aerospace engineering requirements and Clean Sky 2 goals, but it could be easily translated to other similar segment engines, and adjacent businesses and sectors.”

“AM offers enormous potential to lower weight, improve component functionalities, and substantially reduce part count in complex assemblies, directly increasing aircraft energy efficiency and reducing assembly costs and time,” says Christina- Maria Margariti, project officer for hydrogen-powered aircraft for Clean Aviation.
“The Clean Aviation program, in line with the EU Green Deal objective of carbon neutrality by 2050, supports the launch of disruptive new products by 2035, with the aim to replace 75% of the operating fleet by 2050,” Margariti says. “Faster time to market and increased production rates will be crucial to reaching these ambitious environmental targets.”
The consortium team regards its work, and the part itself, as a potential game-changer in metal AM for the future production of large parts for commercial aircraft engines.
“At first, the engineering almost seemed to be impossible, but by leveraging advanced additive technologies and pushing boundaries that stretched our limit, we have achieved a design that was only in our imagination and far away from a reality never thought of before,” Sharma says.
The project employed a multi-disciplinary iteration loop setup to design the hardware and leveraged Lean manufacturing concepts, processes, and tools to reduce design iteration time.
At the beginning of the TURN program, GE AAT Munich explored the design space and performed multiple trade studies leveraging advanced technologies such as AM. The GE AAT Munich team was able to lay down a technology maturation plan to advance the art of making TCF cases.
Finally, when the consortium started to support the technology maturation plan, AutoDesk brought advanced tools to optimize additive design, Hamburg University of Technology (TUHH) added additive machine for initial print trials and Dresden University of Technology (TUD)’s experts built an aero/thermal rig with state-of-the-art instrumentation devices for validation – which blends to give satisfying results at the very first attempt to deliver a successful 360° single-piece additive TCF case.
GE Aerospace Advanced Technology (GE AAT) MunichNEWS AND PRODUCTS
ITT acquires Clippard cylinder product line

Clippard Instrument Laboratories’ product line of interchangeable pneumatic cylinders was acquired by ITT Inc. The acquired lines include stainless steel, brass, and aluminum cylinders and volume tanks, expanding ITT’s Compact Automation offerings which include air cylinders and linear and rotary actuators.
The pneumatic cylinders broaden the Compact offering with products designed for high-speed, high-cycle applications. The two businesses share distribution networks, simplifying the customer purchasing experience and creating opportunities to extend relationships with distributors.
To further serve the growing needs of its customers, ITT’s Compact business will expand its Westminster, South Carolina operations, including engineering, assembly, machining, customer service, and quality departments, to house Clippard cylinder production assets.
Connectors with snap & screw/snap termination

Overmolded M8x1connectors with snap termination can be plugged on sockets, sensors, and actuators without further steps or tools. The compact locking system is secure and complies with protection class IP67 with up to six poles.
CONEC circular connectors and sockets of size M8 with snap and screw/snap termination are available in the standardized codings A and B for signal transmission.
Snap connectors can be mounted on their counterpart with an angled or straight cable outlet if little installation space is available.
Variants with M8x1 thread on one end can be mounted firmly on the threaded socket on the control cabinet, the other end with snap lock can be used flexibly on the assembly and production lines.
Combined CONEC sockets with screw/snap termination feature both locking types, so connectors with thread M8x1 and connectors with snap termination can be mounted.
Sockets are available in different numbers of poles up to 8, and variants are available for front and rear panel mounting. The portfolio also includes sockets for the SMT or THR soldering methods.
CONECSmall, fast servo drive

The Everest S is about 30% smaller than its predecessor, and it’s fast – the EtherCAT and CANopen versions deliver bus latency reduced to 1 cycle.
The Everest S includes the features of other Everest servo drives and hasDual BiSS-C feedback support. It combines 16-bit differential current and four configurable ranges to deliver flawless resolution.
Designed with 3kW of power and a starting weight of just 18g, the Everest S is suitable for Pan Tilt gimbals, collaborative robots, legged robots, and autonomous mobile robots.
High-speed SPI bus communication is available for optimized EtherCAT/CANopen multi-axis architectures.
IngeniaVacuum pump unit

The piCOBOT L has a lifting capability up to 35 lb. It builds on the same technology platform as the original version, consisting of a vacuum pump unit and an optional gripper unit. The vacuum pump unit is scalable and can be equipped with the COAX cartridge. Offering a significantly higher vacuum performance, it enables fast movement when lifting heavier items for high productivity in packaging and palletizing, part assembly, or machine tending.
Its high vacuum flow further facilitates the deployment of large foam grippers lifting a variety of objects, single large and heavy ones, to a multitude of small ones simultaneously. The piCOBOT L is also a platform for customized end effectors, developed by Custom Line specialists or by the customer or system integrator.
PiabIndustrial automation devices
DeviceLink delivers automated backup and change detection for industrial control. It works with Allen-Bradley, CODESYS, Beckhoff, and Fanuc devices and can schedule code backups at any time or frequency. FTP and Bash scripting are also supported; Siemens device support is coming soon. Once the code is backed up, DeviceLink will compare it to the last known version. When changes are detected, it’ll create a new committed version. If desired, new edits can be reviewed, approved, and merged into any ongoing development code.
Copia Automation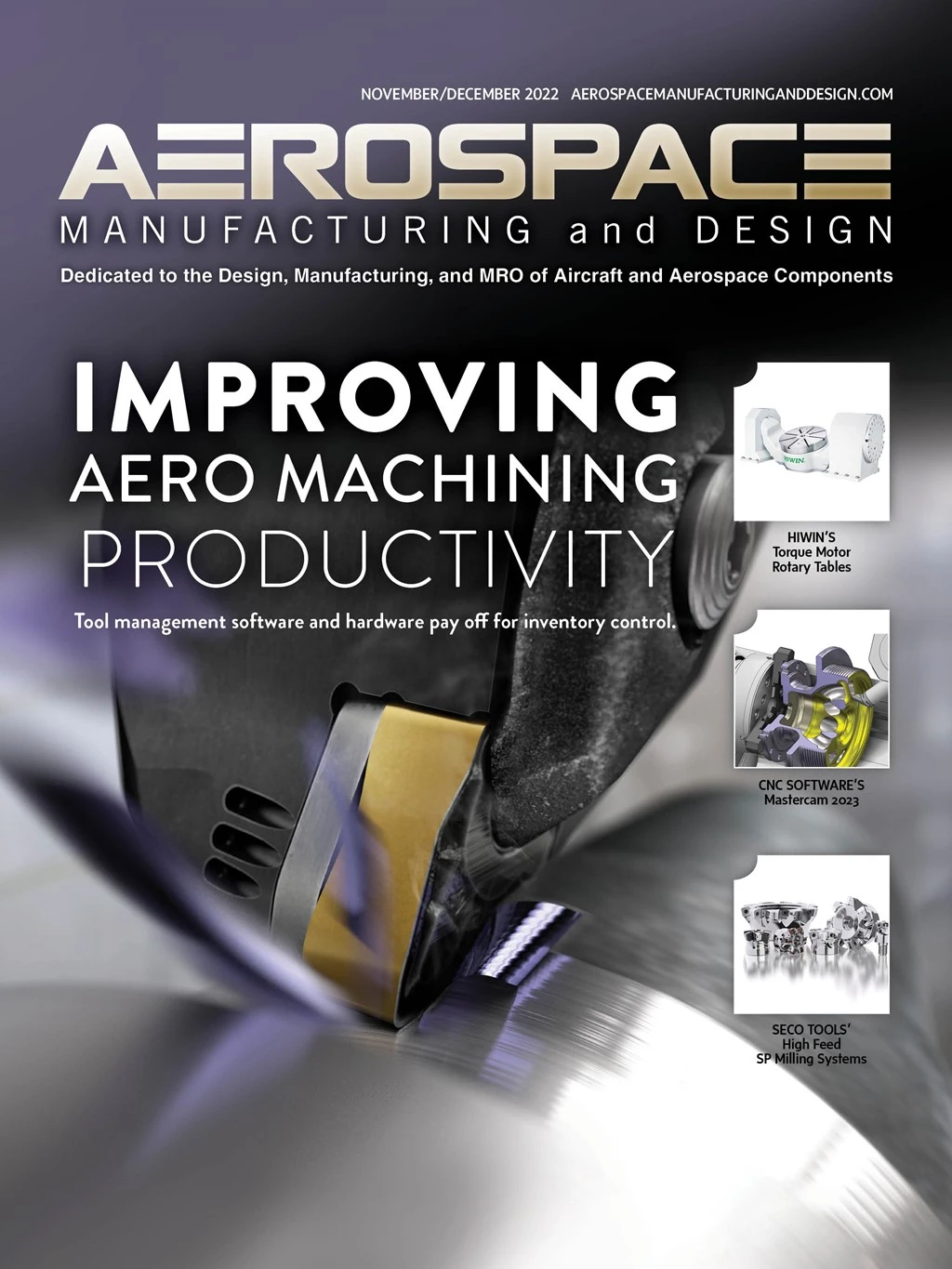
Explore the November December 2022 Issue
Check out more from this issue and find your next story to read.
Latest from Aerospace Manufacturing and Design
- JetZero all-wing airplane demonstrator achieves milestones
- Cermet indexable inserts for medium turning operations
- Trelleborg acquires Aero-Plastics
- Industrial automation products, enclosed encoders
- #61 - Manufacturing Matters: CMMC roll out: When do I need to comply?
- AIX shows aircraft interiors are a strategic priority for global airlines
- Machine Tool Builders Roundtable: Turn equipment into expertise
- No time to waste: How to machine MedTech parts more efficiently