
Around since the 1980s, 3D printing has taken off in recent years. Thermwood Corp., established in 1969 as a thermoformer, developed a process to thermoform wood grain texture to plastic. In the early 1970s, Thermwood manufactured what is believed to be the first computer numerical control (CNC) driven machine.
Fast forward to 2015, Thermwood announced a new additive manufacturing (AM) machine for the 3D printing industry. Most 3D printers at this time were small and made for end-use parts and prototypes. Encouragement from a customer and a renowned professor led Thermwood to develop large-scale additive manufacturing (LSAM), a system that produces tools, molds, masters, patterns, plugs, and fixtures for a variety of industries.
Thermwood’s LSAM can perform both the additive and subtractive functions on the same machine. This near-net-shape approach uses a high-volume thermoplastic printer to quickly create a part that is nearly, but not exactly, the final net shape. A subtractive function then machines the part to the exact final net shape. LSAM prints a large bead at room temperature in a process which is essentially an exercise in controlled cooling. Polymer cooling, not print head output, determines print speed. Polymer cooling determines how fast you can print each layer. Print head output determines how large a part you can print in the layer time available. With LSAM print heads available that can print more than 500 lb per hour, really large parts are possible.
Large print beads – plus Thermwood’s patented compression wheel – create solid, fully fused, virtually void-free printed structures that can sustain vacuum in a pressurized autoclave at elevated temperatures without the need for problematic add-on coatings.
Parts are printed on a patented Bead Board, eliminating most cooling stresses and part warping. The compression wheel fuses layers together and generates highly precise print-bead dimensions, measured in thousandths of an inch.

One area that has been historically weak in large-scale additive manufacturing has been the lack of truly professional slicing software specifically for the near-net-shape process. To address this, Thermwood has developed a near-net-shape computer-aided design (CAD) slicing software, called LSAM Print 3D, that works within Mastercam and provides feature-rich operation. With the ability to coordinate effortlessly with the LSAM machine and control, it accepts solid, surface, mesh, or 2D geometry in every major CAD software format.
Much of the technology used in Thermwood’s LSAM machines and print process is completely new. Thermwood has already received numerous patents on these revolutionary developments and many more are in the works. In addition to numerous announced projects, LSAM has achieved exciting results on many projects that are covered by non-disclosure agreements and must be kept secret. LSAM is truly state-of-the-art in the exciting new world of large-scale additive manufacturing.
For more info.
http://www.thermwood.com
Get curated news on YOUR industry.
Enter your email to receive our newsletters.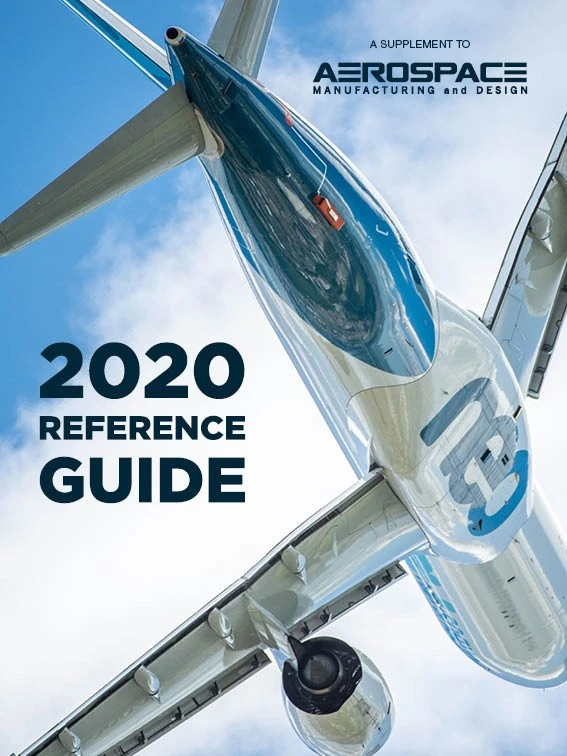
Explore the AMD Reference Guide 2020 Issue
Check out more from this issue and find your next story to read.
Latest from Aerospace Manufacturing and Design
- GE Aerospace secures Air Force engine contract
- Thomson Industries' online sizing and selection tool
- #53 - Manufacturing Matters - 2024 Leaders in Manufacturing Roundtable
- Join us for insights on one of the hottest topics in manufacturing!
- You can still register for March’s Manufacturing Lunch + Learn!
- Ohio creates Youngstown Innovation Hub for Aerospace and Defense
- Tormach’s Chip Conveyor Kit for the 1500MX CNC Mill
- How to Reduce First Article Inspection Creation Time by 70% to 90% with DISCUS Software