
The Sapphire XC 1MZ 3D printer allows customers to print parts 1m in height to address more use-cases for metal additive manufacturing. The printer’s large laser powder bed fusion print volume combines innovative geometric capabilities with repeatable, standardized processes, and validated material properties to achieve distributed manufacturing in a larger format.
IMTS 2022 Booth #433031
Electron beam additive record

The electron beam additive manufacturing (EBAM) process deposited 40 lb (18.14kg) of titanium per hour, making it the highest – and fastest – deposition rate in the world for industrial metal 3D printing.
EBAM deposited more than 330 lb (150kg) of Ti-6AI-4V for three different applications for the Saint Exupéry Institute for Research in Technology’s Metallic Advanced Materials for Aeronautics (MAMA) project. Airbus and Aubert & Duval are key process contributors.
EBAM systems can produce parts up to 19ft (5.79m) in length. EBAM’s interlayer real-time imaging and sensing system digitally self-adjusts metal deposition with precision and repeatability. The closed-loop control allows the EBAM 3D printing process to deliver consistent part geometry, mechanical properties, microstructure, and metal chemistry.
Developing design tools for outer space structures

Aeronautics and Astronautics
Achieving affordable space exploration will require lightweight structures for vehicles, solar arrays, and antennas. Lightweight materials will be used for structural components such as pressurized habitats, cryogenic tanks, landing gear, and truss cages.
NASA envisions structures made from tailorable composite materials, but no design tool can fully exploit the materials’ full potential. AnalySwift LLC, a Purdue University-affiliated commercial software provider, and Wenbin Yu, a professor in Purdue’s School of Aeronautics and Astronautics, are conducting research to create one.
Existing design tools were developed for traditional composites, which have straight fibers. If an open area is needed inside a traditional composite structure, it’s accomplished by creating a cut-out after manufacture, compromising the structure’s integrity.
Tailorable composites, also known as tow-steered or variable thickness composites, can be highly customized due to improvements in manufacturing. New robotic techniques can weave fibers around openings, expanding design options while improving the structures’ overall properties.
DLP 3D printing resin

3D printing resin specifically for digital light processing (DLP) 3D printing of wearing parts enables additive manufacturing (AM) of small, precise components with a service life 30x to 60x longer than with conventional 3D printing resins.
For components in the millimeter range, DLP 3D printers achieve very fine resolution using various 3D printing technologies. Resolutions of 0.035mm are possible, around half the thickness of a human hair. A projector casts layers of the 3D model onto the surface of a special liquid resin. The corresponding regions network under the influence of light. After curing, the construction platform is lowered by one layer for the next exposure. This process creates tiny components, including gears with tips 0.2mm thick with extremely smooth surfaces that require no post-treatment. Microscopic solid lubricants are integrated into the material and released independently during movement.
IMTS 2022 Booth #134812
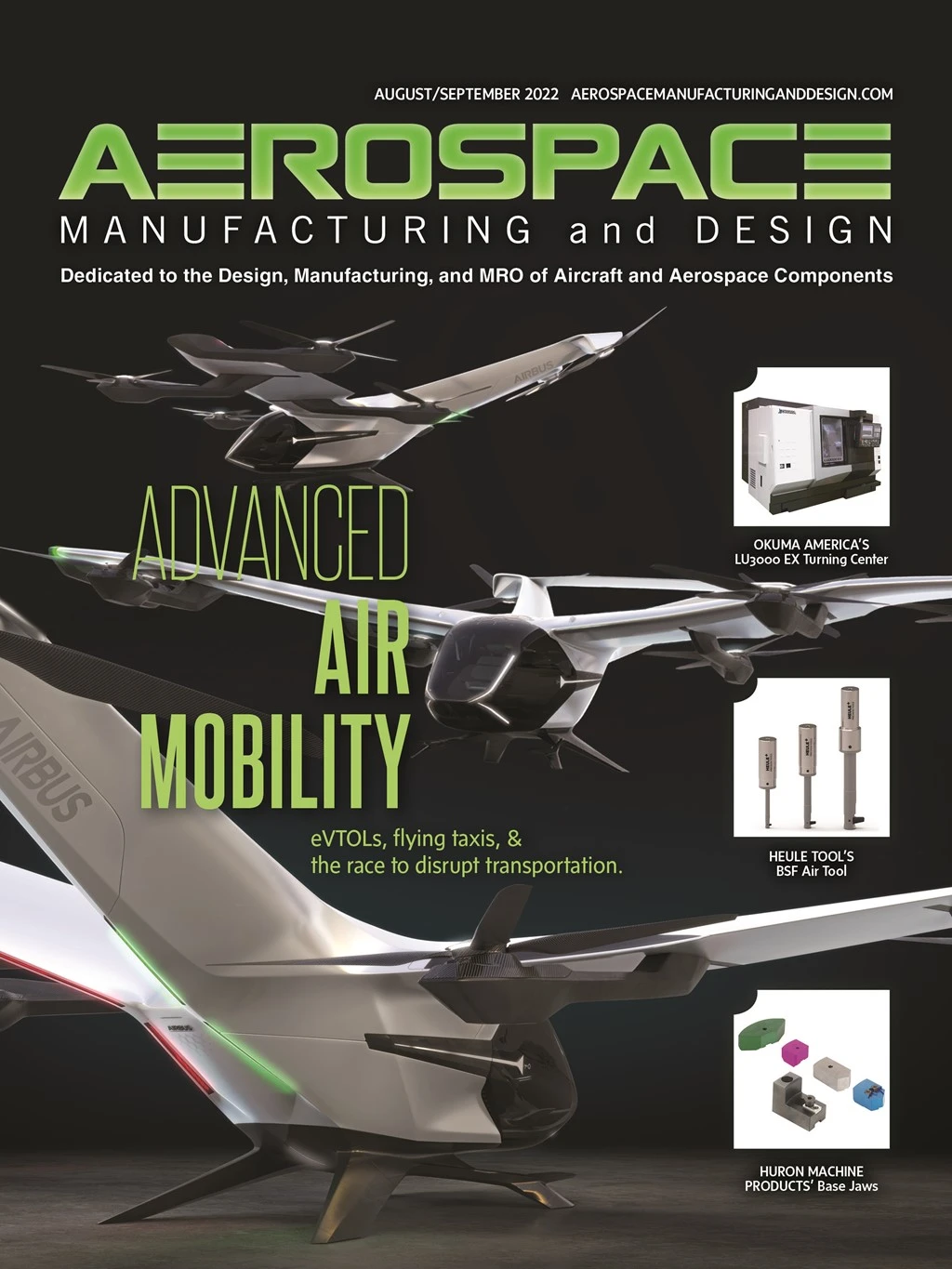
Explore the August September 2022 Issue
Check out more from this issue and find your next story to read.
Latest from Aerospace Manufacturing and Design
- AAMI project call submission deadline extended to May 12
- Jergens launches cast iron tooling column additions
- Airbus to acquire assets relating to its aircraft production from Spirit AeroSystems
- FANUC America's Cobot and Go web tool
- Chicago Innovation Days 2025: Shaping the future of manufacturing
- High-density DC/DC converters for mission-critical applications
- #59 - Manufacturing Matters: Additive manufacturing trends, innovations
- ACE at 150: A legacy of innovation and industry leadership