
Triton Space Technologies, an engineering design and manufacturing company specializing in rocket propulsion systems also provides contract engineering and prototype manufacturing services for customers requiring custom products.
“We had a customer going to the moon in 2021 who commissioned us to build some valves for them,” says Luke Colby, president and CEO of Triton Space Technologies. “We wanted to create a functional prototype of the valve, to check all the parts fit together properly, and the internal parts could slide and move as they should. We went into it not really expecting the METHOD X would be able to keep the tolerances needed for the sliding parts to move, but it did.”

Colby founded Triton Space Technologies in 2014, following 10 years as lead propulsion engineer for Virgin Galactic’s suborbital space tourism vehicle. It wasn’t until the launch of the MakerBot METHOD X 3D printer that he considered a desktop machine that could produce truly functional prototypes.
Triton had to machine prototypes from sheet aluminum in its machine shop, a costly, inefficient process that took 2 to 3 days per prototype and created a lot of material waste. The alternative was to outsource to a 3D printing service bureau. However, this took even longer and didn’t always result in a usable part.

The ability to print with Stratasys SR-30 soluble support material is key to enabling Triton Space Technologies to produce functional prototypes with the tolerances required. If produced without supports, or using snap-off supports, parts would have to be filed and sanded, greatly reducing their usefulness. Harnessing 3D printing’s ability to produce complex geometries, with fewer individual parts, the company can create increasingly sophisticated prototypes capable of meeting the diverse needs of its customers.
High-precision shaping capabilities

The high-precision shaping package includes 0.006" and 0.010" ball mill cutting tools and automated tool-pathing software, enabling tool rooms to automate the toolmaking process by producing sharp corners and edges without requiring EDM operations. By eliminating EDM and other toolmaking operations, Mantle helps tool rooms reduce the time required to produce mold tools up to 75%.

TrueShape technology combines 3D printing of its tool steel pastes with traditional CNC machining to refine the shape of printed tools and deliver accuracy, surface finish, and tool steel properties. The 3D printer is built on a trusted CNC platform and uses multiple cutting mills to refine the shape of the printed tool while it’s still in a soft state. The high-precision shaping package enables tool rooms to produce tools with radii <0.003", a 70% improvement compared to the 0.010" radii previously attainable, eliminating more of the costly and time-consuming EDM operations of traditional toolmaking.
3D-printed revolving devices can sense movement

Advances in 3D printing enable rapid fabrication of rotational mechanisms but integrating sensors into the designs is still difficult. Sensors are typically embedded manually after the device has already been produced because of the complexity of rotating parts. Embedding them inside a device might entangle wires in the rotating parts or obstruct rotation, but mounting external sensors would increase a mechanism’s size and potentially limit its motion.
MIT researchers developed a system to 3D print sensors directly into a mechanism’s moving parts using conductive 3D printing filament. Devices can sense their angular position, rotation speed, and direction of rotation.

With the MechSense system, a maker can manufacture rotational mechanisms with integrated sensors in just one pass using a multi-material 3D printer.
To streamline the fabrication process, researchers built a plugin for the SolidWorks CAD software that automatically integrates sensors into a model of the mechanism, which can be sent directly to the 3D printer for fabrication.

MechSense could enable engineers to rapidly prototype devices with rotating parts, such as turbines or motors, while incorporating sensing directly into the designs. It could be useful in creating tangible user interfaces for augmented reality (AR) environments, where sensing is critical for tracking a user’s movements and interaction with objects.
Get curated news on YOUR industry.
Enter your email to receive our newsletters.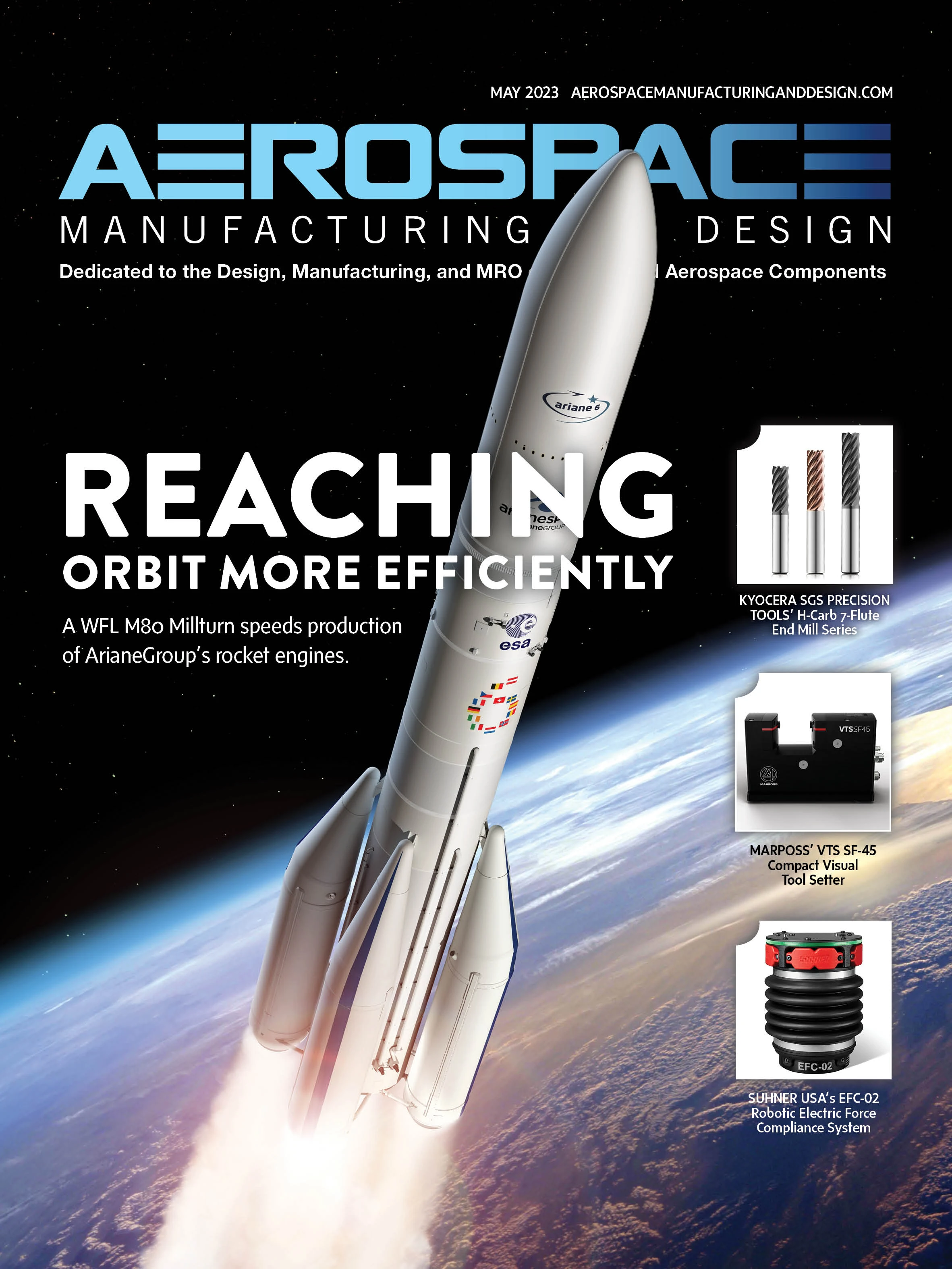
Explore the May 2023 Issue
Check out more from this issue and find your next story to read.
Latest from Aerospace Manufacturing and Design
- Revitalizing the Defense Maritime Industrial Base with Blue Forge Alliance
- Safran Defense & Space opens US defense HQ
- Two miniature absolute encoders join US Digital’s lineup
- Lockheed Martin completes Orion for Artemis II
- Cylinder CMMs for complex symmetrical workpieces
- University of Oklahoma research fuels UAS development
- Motorized vision measuring system
- Everyone's talking tariffs