
GIE Media

1) How does Dynamic Milling (DM) differ from a conventional offset toolpath, and why choose it?
Ask when, not why. Neither is a perfect toolpath for every operation, both have their advantages. There is a lot to consider when deciding between them. The most important of which is machine capability. DM is used for deep axial and light radial cuts and requires a high acceleration/deceleration machine with good look-ahead capabilities for the code-heavy programs. Without this, you may not get the programmed feed rate. Offset toolpaths are for heavier stepovers and shallower cuts requiring a robust machine and fixturing. Other capabilities are usually less crucial.
2) What kind of tool would you choose for DM, and how would it differ from a tool for an offset toolpath?
If you were to use an offset toolpath, you would commonly use a 2-to-5 flute tool, such as our Z-Carb AP or Z-Carb HPR – tools with more chip space that can take heavier stepovers. With DM, you would use something with more flutes, such as our series 51 T-Carb 6-flute end mills. That lets you apply a chip thinning approach to the operation.
3) If you can run a higher feed rate with more flutes, is the highest number of flutes always best for DM?
Not in every scenario. There is a tradeoff that needs to be balanced. You can run a higher feed rate with more flutes, but more flutes means less chip space, forcing you to either decrease the chip load by slowing down your feed rate or decrease your stepover. Insufficient chip space can cause chatter, chip packing, or tool failure/breakage. A high feed rate is great, but a higher feed doesn’t always correlate directly to a faster cycle time. Your material removal rate (MRR) can be increased by decreasing your feed and increasing the radial depth of cut. The open-flute structure of our tools designed for DM allows increased chip space and radial width of cut at accelerated feed rates.
4) What advantage do chip breakers provide for DM?

The deep axial cuts and long flute length needed for those cuts result in a long chip that, if not cleared away, can be re-machined, causing premature tool chipping/failure. They can also clog chip augers/conveyers. Chip breakers that break those long chips into shorter, more manageable chips make them easier to remove.
5) Is DM the best machining style for all material groups?
I’d say it is less material specific and more feature specific. As mentioned earlier, neither style is perfect for every operation. DM is the best style for deep axial cutting, while an offset toolpath may be best when you have a shallower feature at hand. Some materials are easier to machine than others, but a more machinable material may give you the freedom to take a wider cut or run a higher feed rate.
For more information: www.kyocera-sgstool.com
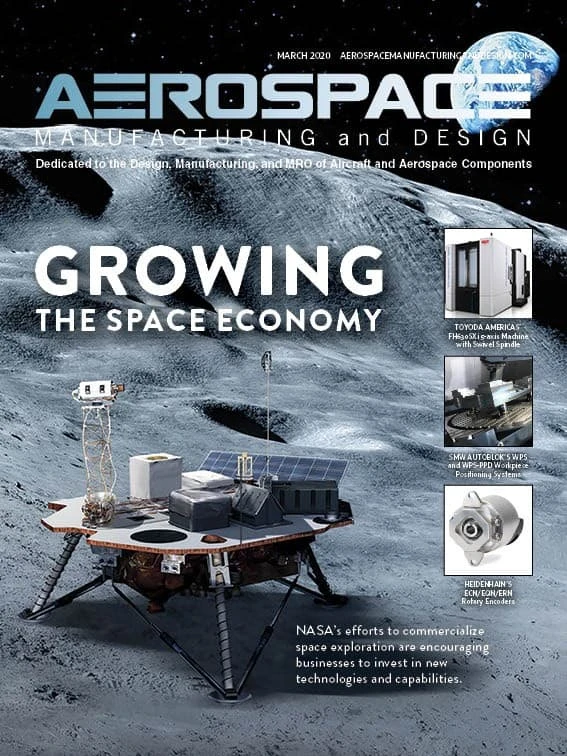
Explore the March 2020 Issue
Check out more from this issue and find your next story to read.
Latest from Aerospace Manufacturing and Design
- AIX showcases the future of air travel
- Sunnen Products' PGE-6000 gage
- #41 Lunch + Learn Podcast - SMW Autoblok
- Revolutionizing aircraft design without sacrificing sustainability
- GE Aerospace awarded subcontract for FLRAA next phase
- KYOCERA Precision Tools publishes 2025-2026 Indexable Cutting Tools Catalog
- BOC Aviation orders 120 Airbus, Boeing jetliners
- Mazak’s INTEGREX j-Series NEO