
Speedy quantification of part defects directly leads to faster turnaround time (TAT) via reduced inspection times. Accurate metrology removes any doubt about the severity of defects, reducing scrap and increasing yield to further improve TAT.
Widely used inspection techniques in maintenance, repair, and overhaul (MRO) shops can provide quick TAT but often can’t accurately evaluate defects. Alternatively, techniques that provide needed accuracy can come at the cost of a quick TAT. To provide fast and accurate defect detection, 4D Technology developed the 4D InSpec Surface Gauge, putting metrology and 3D measurement on the shop floor.

Speed vs. accuracy
Visual tests and fingernail inspection rapidly find defects. Inspectors use their fingernails to make an educated guess as to how large a nick, scratch, or bump is. It provides no quantifiable data and is subjective, though some inspectors are good at classifying larger defects into a range of depths. When unsure whether a defect is acceptable, inspectors tend to err on the side of caution and reject it. That gray area often leads to rejecting parts that meet specifications. Visual inspection only correctly identifies about 85% of bad parts and improperly rejects 35% of good parts, studies show.1 The result is the loss of millions of dollars in good parts by MRO facilities every month. Visual and tactile inspection may provide all-important quick TAT, but at a cost in yield. Rather than a fingernail, a scribe gage better quantifies parts, but they often can’t penetrate to the bottom of parts, and finding a proper reference area on complex geometries adds further uncertainty.
Another defect measurement technique is using replication, combined with an optical comparator or stylus profiler. This method uses costly replication materials, can take around 30 minutes to complete, and provides only 2D traces across a single defect. Defects aren’t mapped along their entire extent – the deepest part of a pit may not have been crossed by the measured cross-section, leaving the deepest point unknown. Additionally, it’s not always visually obvious which pit is deepest, as discolorations and shadowing can cause uncertainty. Through any of these limitations, inspectors reject parts rather than passing a potentially bad component.
Nanometer-scale resolution inspection that removes the gray area but typically requires measurements to leave the shop floor to be inspected with lab-based 3D optical profilers or contact-based stylus profilers. Shipping processes and demand for the instruments can push TAT to weeks. The instruments are significantly more expensive than other processes (up to $200,000) and require a designated, trained operator. And, systems only measure small parts and samples, meaning larger parts require review of replicated defects. These systems provide the high resolution necessary to accurately measure defects and increase yield at the cost of TAT. Often, operators will reject or rework parts for unquantified defects rather than slow the process to accommodate high-resolution techniques.

Shop floor metrology
Working with the three largest engine manufacturers and various MRO organizations, 4D Technology set out to put a high-resolution instrument on the shop floor. The 4D InSpec and 4D InSpec XL are vibration-immune, 3D surface gages designed for portable, rapid, precise measurements at existing inspection stations. Polarized structured light technology allows the gages to be handheld while maintaining a height resolution of 0.0001" (2.5µm).2 Inspectors can perform accurate, in situ defect quantification without sending parts to a lab.
With non-contact and non-destructive measurements of surfaces ranging from rubber to polished metal, defect analysis with the 4D InSpec is like taking a picture. The instrument communicates to a desktop, laptop, or tablet with an Ethernet cable. Data collection and analysis occur in a fraction of a second, displayed through analytical software for the inspector. Aviation customers can use a backpack power supply and handheld tablet for maximum portability for applications, such as on-wing measurements.
Taking measurement systems to the part reduces TAT by providing instant data and reduced labor. Fold mirror attachments allow 4D InSpec to take measurements that aren’t within line-of-sight. At one aviation manufacturer, being able to access tight spaces saves a week of labor – per measurement – by eliminating the need to disassemble everything.

Instant 3D measurement
2D techniques, such as styli and optical comparators for defect measurement, are common on shop floors, but there are drawbacks to lacking an area-based measurement. There is no way to guarantee a 2D trace measures the most extreme part of a defect, and each defect must be measured sequentially. For parts with many defects, this can become time-consuming.
3D measurement maps each defect in the field of view – guaranteeing that the deepest part of a long scratch was measured. Measuring every defect in the field of view simultaneously allows quantifying dozens of corrosion pits, so the deepest point automatically displays.
InSpec’s design allows macro area-coverage and access to recessed features, while maintaining high vertical and lateral resolution. The software’s Feature Analysis displays all data for every feature in the measurement so inspectors don’t have to individually evaluate each defect individually. This is especially useful for inspecting corrosion pitting or dot peening. Precisely measuring defects means inspectors can stop padding depths due to uncertainty, reducing unnecessary rework and rejection of otherwise good components. Additionally, results can be printed, exported to a file, or uploaded into a facility’s quality control system, providing a comprehensive digital record of the measurement. Records can be reviewed and even re-analyzed later should there be any question about the results.

Qualifying geometries
3D measurement is also a powerful tool for assessing critical small geometries such as edge break, radii, and chamfers. If a 2D trace is not perpendicular to such a feature, the radius of curvature or chamfer length calculated will be artificially larger, due to improper trace orientation. Edge break and feature radius are important callouts for many aviation components. Relying on an operator to get the exact 2D trace correct is unrealistic. 3D data allows software to mathematically find the true radius of curvature or chamfer angles and dimensions, independent of human judgment. Since the feature is sampled across many hundreds of lines, the results are more comprehensive and reassure operators of their accuracy.
Rivet analysis
A 3D measurement of a rivet enables software to analyze the planarity of the rivet and its depth or height relative to the surrounding surface. Users can set pass/fail thresholds in the software based on their specifications and receive immediate feedback for each measurement.
Conclusion
As the MRO industry works to improve TAT while maintaining quality, the need for precise shop-floor measurement is increasingly important. Accurate, simple 3D metrology allows inspectors to qualify parts right up to the specification line. This reduces unnecessary rejection and rework without the risk of passing bad components. A handheld shop floor gage allows automatic determination of the deepest feature within the measurement area, across multiple pits or scratches if they are present. Such measurements provide edge break, chamfer, and radius analysis, allowing one system to accomplish multiple inspection tasks. Finally, a digital record of measurement results is critical, should it be necessary to review history and the exact results.
NOTES: 1. See, J.E.: Visual inspection reliability for precision manufactured parts. Human Factors 57(8), 1427–1442 (2015)
2. Joanna Schmit, Erik Novak, and Shawn McDermed “Inspection of mechanical surfaces with polarized structured light,” Proceedings SPIE 10834, Speckle 2018: VII International Conference on Speckle Metrology, 108342F (7 September 2018); https://doi.org/10.1117/12.2322178
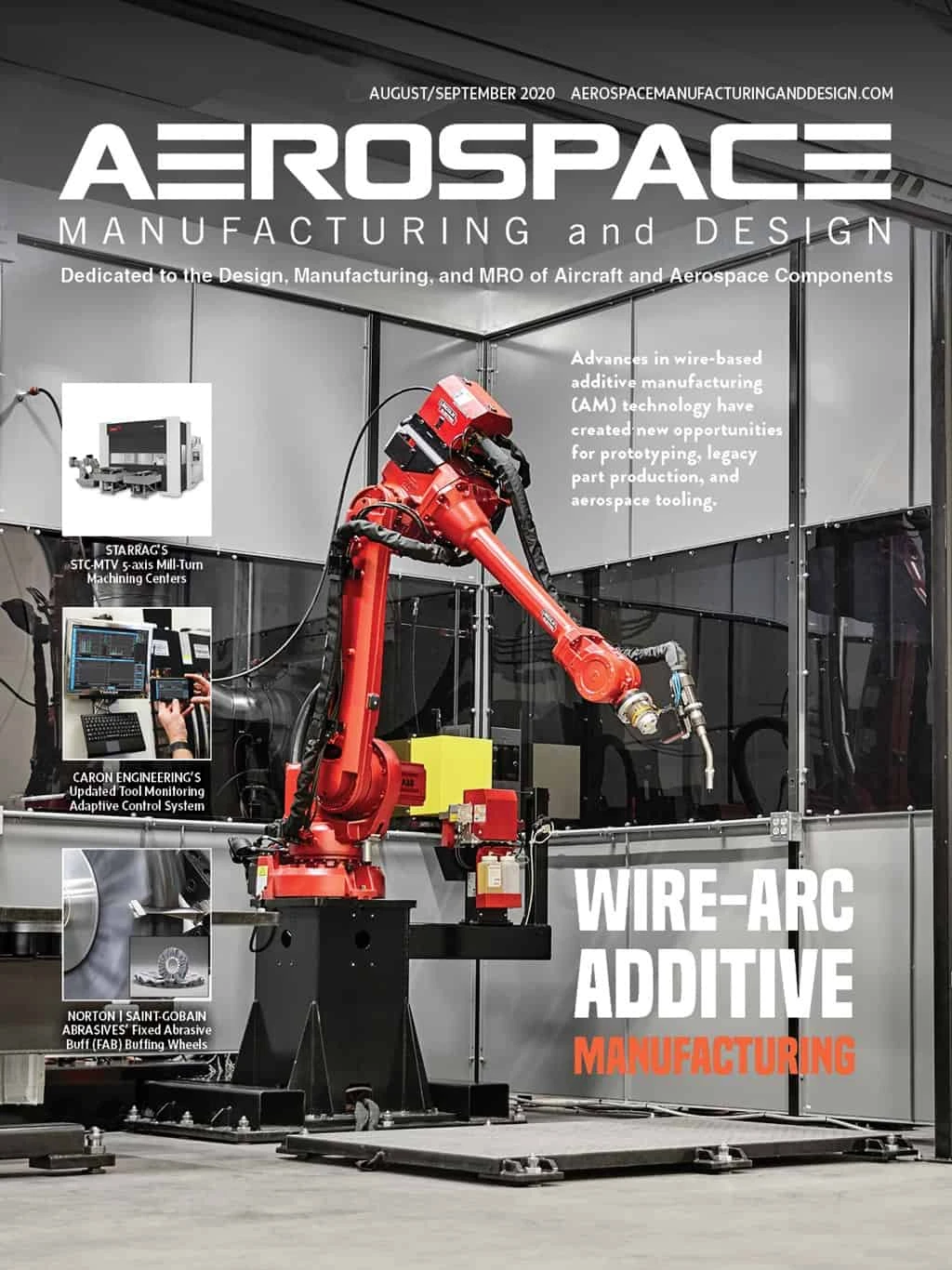
Explore the August September 2020 Issue
Check out more from this issue and find your next story to read.
Latest from Aerospace Manufacturing and Design
- Revitalizing the Defense Maritime Industrial Base with Blue Forge Alliance
- Safran Defense & Space opens US defense HQ
- Two miniature absolute encoders join US Digital’s lineup
- Lockheed Martin completes Orion for Artemis II
- Cylinder CMMs for complex symmetrical workpieces
- University of Oklahoma research fuels UAS development
- Motorized vision measuring system
- Everyone's talking tariffs