
R obots that can climb on vertical or upside-down conductive surfaces, such as the inside walls of commercial jet engines, could explore complex spaces in three dimensions instead of moving back and forth on a flat surface. The Harvard Ambulatory Micro-Robot with Electroadhesion (HAMR-E) is such a micro-robot with electroadhesive foot pads, origami ankle joints, and a specially engineered walking gait.
It was developed by researchers at Harvard University’s Wyss Institute for Biologically Inspired Engineering and John A. Paulson School of Engineering and Applied Sciences (SEAS).
“They could one day enable non-invasive inspection of hard-to-reach areas of large machines, saving companies time and money and making those machines safer,” notes Sébastien de Rivaz, a former Research Fellow at the Wyss Institute and SEAS who now works at Apple.

HAMR-E was developed in response to a challenge issued to the Harvard Microrobotics Lab by Rolls-Royce to design and build an army of micro-robots capable of climbing inside parts of its jet engines that are inaccessible to workers. Existing climbing robots can tackle vertical surfaces but experience problems when trying to climb upside-down, as they require a large amount of adhesive force to prevent them from falling.
The team based HAMR-E on one of its existing micro-robots, HAMR, whose four legs enable it to walk on flat surfaces and swim through water. While the basic design of HAMR-E is similar to HAMR, scientists had to solve a series of challenges to get HAMR-E to successfully stick to and traverse the vertical, inverted, and curved surfaces it would encounter in a jet engine.
First, they needed to create adhesive foot pads that would keep the robot attached to the surface even when upside-down, but also release to allow the robot to walk by lifting and placing its feet. The pads consist of a polyimide-insulated copper electrode, enabling generation of electrostatic forces between the pads and the underlying conductive surface. The foot pads are released and re-engaged by switching the electric field on and off, operating at a voltage similar to that required to move the robot’s legs. The electroadhesive foot pads can generate shear forces of 5.56g and normal forces of 6.20g – more than enough to keep the 1.48g robot from sliding down or falling off surfaces. In addition to providing high adhesive forces, the pads were designed to flex, allowing climbing on curved or uneven surfaces.
The scientists also created new ankle joints for HAMR-E that can rotate in three dimensions to compensate for rotations of its legs as it walks, so it can maintain orientation on its climbing surface. The joints were manufactured out of layered fiberglass and polyimide and folded into an origami-like structure allowing the ankles of all the legs to rotate freely and passively align with the terrain as HAMR-E climbs.

Finally, researchers created a special walking pattern for HAMR-E, as it needs to have three foot pads touching a vertical or inverted surface at all times to prevent a fall or slide. One foot releases from the surface, swings forward, and reattaches while the remaining three stay attached to the surface. At the same time, a small amount of torque is applied by the foot diagonally across from the lifted foot to keep the robot from moving away from the climbing surface during the leg-swinging phase. This process is repeated for the other three legs to create a full walking cycle, synchronized with the pattern of electric field switching on each foot.
When testing HAMR-E on vertical and inverted surfaces, it was able to achieve more than 100 steps in a row without detaching. It walked at speeds comparable to other small climbing robots on inverted surfaces, slightly slower than other climbing robots on vertical surfaces, and was significantly faster than other robots on horizontal surfaces. It is also able to perform 180° turns on horizontal surfaces.
HAMR-E also successfully maneuvered around a curved, inverted section of a jet engine while staying attached, and its passive ankle joints and adhesive foot pads were able to accommodate the rough, uneven features of the engine surface simply by increasing the electroadhesion voltage.
The team is continuing to refine HAMR-E, planning to incorporate sensors into its legs to detect and compensate for detached foot pads, which will help prevent it from falling. HAMR-E’s payload capacity is also greater than its own weight, opening the possibility of carrying a power supply, other electronics, and sensors to inspect various environments. Researchers are also exploring options for using HAMR-E on non-conductive surfaces.
Wyss Institute for Biologically Inspired Engineering
John A. Paulson School of Engineering and Applied Sciences (SEAS)
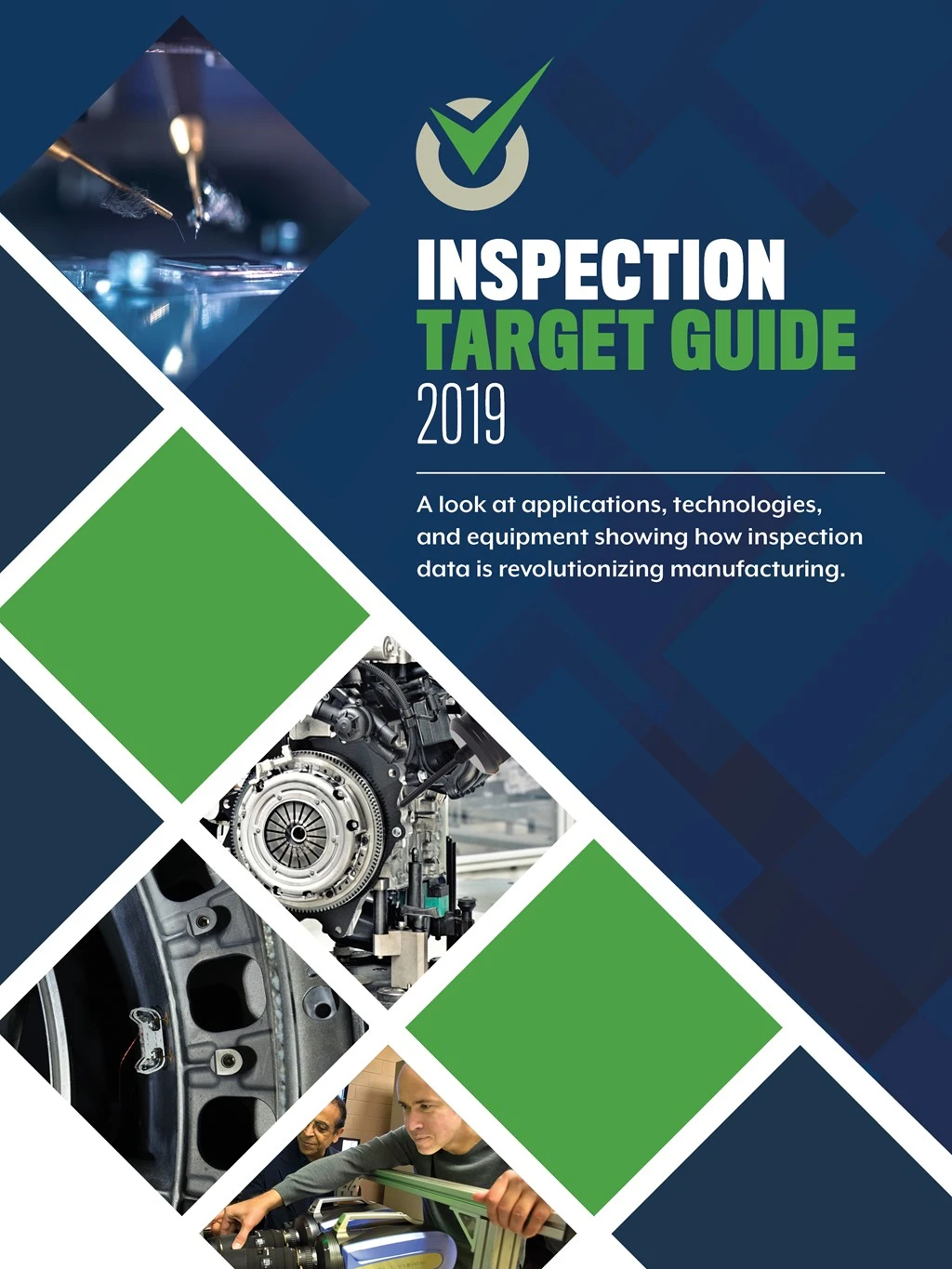
Explore the Inspection Target Guide Issue
Check out more from this issue and find your next story to read.
Latest from Aerospace Manufacturing and Design
- Revitalizing the Defense Maritime Industrial Base with Blue Forge Alliance
- Safran Defense & Space opens US defense HQ
- Two miniature absolute encoders join US Digital’s lineup
- Lockheed Martin completes Orion for Artemis II
- Cylinder CMMs for complex symmetrical workpieces
- University of Oklahoma research fuels UAS development
- Motorized vision measuring system
- Everyone's talking tariffs