
When you think of an inkjet printer, the first thing you imagine is a sheet of paper being pulled through a blocky device and coming out the other end covered in ink. However, an independent, nonprofit, applied research and development organization is challenging that with a device that prints on aircraft instead of paper.
The Southwest Research Institute (SwRI), has secured a patent for a large-scale robotic inkjet printer for aircraft and other complex surfaces.
Clay Flannigan, manager of robotics and automation engineering at SwRI, says aircraft decorative coatings are becoming more complex, leading aircraft manufacturing and maintenance communities to search for more efficient techniques.
“There is a lot of interest in using inkjet technologies applied to aircraft painting, but to fully leverage the potential efficiency and aesthetic advantages of the process, the technology must be able to print on a variety of complex geometries and in varied orientations over large areas,” Flannigan says.
He claims inkjet printing surpasses other processes such as decals or appliqués, which are difficult to qualify due to adhesion and robustness issues across the range of speeds and environmental conditions in which aircraft operate.
How it works
This inkjet printing process, also known as direct printing, is a disruptive technology that allows users to digitally print complex and unique graphics on everything from textiles to billboards. SwRI’s researchers take this concept and apply it to the aviation industry to replace the more traditional, laborious process of painting large graphics on aircraft parts with a faster, streamlined one.
U.S. Patent No. 9,527,275, for “High Accuracy Inkjet Printing,” covers hardware and software for precision printing of multiple graphic swaths of color ink onto complex surfaces, creating a continuous graphic image. Each graphic swath can be aligned over curved surfaces without spaces, gaps, or discontinuities.
A vision sensor detects an encoded pattern to accurately apply the graphic images. The encoded pattern is deposited on the surface in a known location with respect to the most recently deposited graphic swath. The printing system has high-bandwidth servo actuators to locate the print head with respect to the encoder pattern to enable precise positioning for the next swath.
Development
This technique is an internally funded successor of SwRI’s earlier work on the laser coating removal (LCR) technology. The LCR technology combines a mobile robotic platform, laser scanning technology, and high-powered lasers for safe and efficient removal of paint and other aircraft coatings.
The inkjet’s development pushed SwRI to overcome obstacles such as painting large, complex surfaces and adjusting robot positioning.
“We have been developing new processes for removing paint from aircraft for nearly three decades. Now we are looking to revolutionize the way decorative finishes are applied to aircraft,” Flannigan says.
Southwest Research Institute
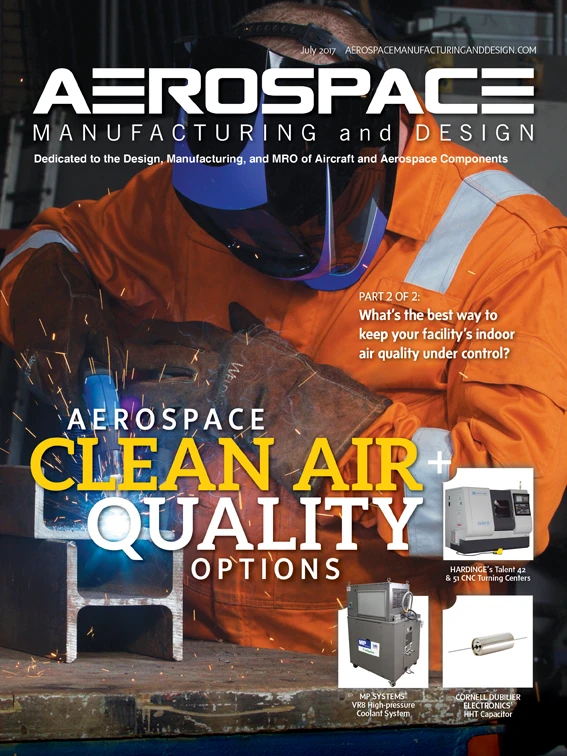
Explore the July 2017 Issue
Check out more from this issue and find your next story to read.
Latest from Aerospace Manufacturing and Design
- Taiwan’s China Airlines orders Boeing 777X passenger, freighter jets
- Reamer re-tipping extends life of legacy tooling
- Revitalizing the Defense Maritime Industrial Base with Blue Forge Alliance
- Safran Defense & Space opens US defense HQ
- Two miniature absolute encoders join US Digital’s lineup
- Lockheed Martin completes Orion for Artemis II
- Cylinder CMMs for complex symmetrical workpieces
- University of Oklahoma research fuels UAS development