
Alcoa recently opened an expansion dedicated to producing powdered metals for 3D printing/additive manufacturing as part of a $60 million investment on its Western Pennsylvania campus. Soon to be part of Arconic – the engineered products and materials company separating from Alcoa’s traditional commodity business – the facility will be capable of atomizing titanium, aluminum, and nickel into the raw material used in metal deposition additive manufacturing (AM) systems. The state-of-the-art, industrial-scale facility is capable of producing enough powder for the company’s use for the next several years, according to Rod Heiple, director, research and development for Alcoa’s Engineered Products and Solutions division.
The company is expanding its capabilities in AM, a market Alcoa leaders expect will grow rapidly – citing an estimate for a global AM industry worth $21+ billion by 2020.
“The key is to play everywhere and put double-down bets on places you see innovation, such as marrying materials and manufacturing processes to solve the most critical challenges,” says Eric Roegner, whose multiple titles include president of Alcoa’s Titanium and Engineered Products division. By creating industrial-scale, additive-materials capability across three major aerospace metals, the company plans to be ready, no matter which metal finds favor first.
Roegner notes that additive manufacturing still needs to define quality standards, inspection, verification, and certification methods, requiring a network of universities, government agencies, and defense and commercial aerospace industry players.
At the technical center, Alcoa has been experimenting with just about all major 3D printing powder-bed and direct metal-deposition processes – testing machines from a refrigerator-sized, nylon-deposition stereolithography machine to an electron-beam, wire-deposition behemoth the size of a recreational vehicle.
Heiple emphasizes the company is “leaning forward” in developing AM, not just in controlling the raw material’s microstructure, but also in applying thermal and physical processing to enhance the end product. Alcoa officials are leveraging expertise across the enterprise; for example, by using proprietary forging techniques on additively manufactured metal components. Forging processes and hot isostatic pressing (another area of Alcoa investment) can densify 3D-printed metals, align grain structure, and reduce residual strain, improving resistance to crack generation and fatigue. To validate these processes, researchers are methodically testing additively manufactured parts substituted as one variable along a well-established manufacturing path from raw material to finished product.
It’s not just about substituting AM parts for those manufactured with traditional methods. Additive manufacturing can incorporate features on large forgings, reducing overall machining time and cutting materials waste. AM can open opportunities for new designs offering strength and low weight, optimized for manufacturing, or make parts with impossible-to-machine geometry.
Known for more than a century for producing metal in ingots, rolled plate, and sheet, Aloca – soon-to-be Arconic – shows me they’re serious about the potential of 3D/AM, putting a lot of dollars into capabilities ready now and for whatever direction the additive market takes in the future. – Eric
Get curated news on YOUR industry.
Enter your email to receive our newsletters.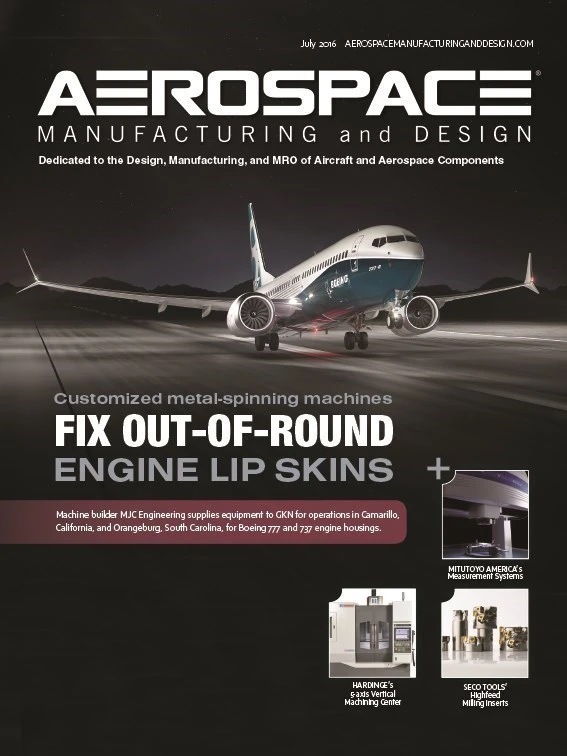
Explore the July 2016 Issue
Check out more from this issue and find your next story to read.
Latest from Aerospace Manufacturing and Design
- BOC Aviation orders 120 Airbus, Boeing jetliners
- Mazak’s INTEGREX j-Series NEO
- Embraer tests wing for new technologies demonstrator
- Mitutoyo America’s SJ-220 portable surface roughness tester
- #55 - Manufacturing Matters - A Primer on Defense Contract Manufacturing
- Registration is open for April’s Manufacturing Lunch + Learn!
- Natilus begins search for new home to build world's most efficient commercial aircraft
- Aerospace Industry Outlook webinar is back by popular demand