
For many drying and curing applications, using infrared radiation (IR) rather than conventional convection systems improves efficiency for aerospace manufacturers and maintenance, repair, and overhaul (MRO) service providers, who are always seeking to trim costs and improve production efficiencies.
The availability of a wide range of IR heating elements, standard and custom heating panels, and new or retrofit ovens and dryers into which heaters are placed simplifies the conversion from convection to IR heating. For MRO providers, IR heating systems are capable of drying and curing various coatings including primers and other undercoats, thermoset resins, polyurethane wet-look coatings, urethane, and other clear coatings.
In addition to various paints and coatings, some aircraft industry composite materials specialists foresee that the finishing and repair of composite materials used in aircraft structural components could benefit from IR heating systems.
Benefits of IR
Gas or electric IR can dramatically reduce drying and curing time, a benefit attractive to volume manufacturers of new components and MRO companies. Using IR heat, drying time is often reduced to minutes, depending on paint or other coating requirements, compared to many hours for convection drying systems. Reduction can exceed 90%.
“Due to its vastly improved efficiency, drying and curing with infrared can greatly reduce energy costs,” explains Jesse Stricker, founder of Intek Corp., a manufacturer that specializes in designing and building electric infrared heating elements, heaters, ovens, and dryers. “Infrared heaters require little or no induced circulation from blowers and fans, are extremely zone-able, and less susceptible to humidity.”
Stricker adds that IR systems generally save space, energy, and time. Convection ovens require blowers and ductwork to deliver heated air from the heat source to the substrate. Infrared heat, on the other hand, travels through the air directly to the substrate. In addition to directly heating surfaces, the heat from IR emitters can be reflected onto parts, providing added drying coverage.
“IR drying and curing is cleaner, providing a higher quality finish on coated products,” Stricker explains. “Because IR heat transmission is line-of-sight and doesn’t depend on large fans or blowers, contamination on the coated surface is virtually nonexistent. This eliminates product rejects and reworking.”
Better control, better results
One of the primary reasons why aerospace parts manufacturers and MROs are converting to IR drying and curing is because it is easier to monitor and control than many convection heating systems.
“It is necessary to understand the behavior of the heat coming from a source, and the fact that the heat must be monitored,” Stricker explains. “Each heat zone has its own temperature control and thermocouple, the thermoelectric device used to measure the temperature. In the case of infrared heating technology, this allows our zoning to be very tightly controlled. This provides a full-surface reference of the actual IR emitter temperature; you can correlate that by running tests on customer’s actual parts prior to presenting the design. This way, you know 800°F at the emitter correlates with 350°F at the part during a specific period of time.”
In drying and curing of paints and other coatings, well-defined heating zones are often required. Multiple zones are trickier with convection heating because it is more difficult to monitor and control multiple blowers and heat sources. With IR heating, each emitter module is a building block of the oven or array, making it simpler to create as many zones and controls as required to achieve the desired results.
There are drying and curing applications where convection heating can be combined with IR panels to create a hybrid system. One example of such a system is when IR is used at the beginning of a process line to preheat the products before going to a convection oven for drying. This hybrid system is advantageous when the products have hidden surfaces that can be dried more evenly by convection heating. In some instances, hybrid systems require a small IR heating chamber to be added before the convection oven; in others, relatively compact IR heaters can be placed within the first section of the convection oven.
Drying & curing composites
Composite, layered or sandwiched carbon-based materials are often used to improve the structural properties of aircraft fan cowlings, undercarriage doors, trailing-edge wedges on flight control surfaces, and fuselage undercarriage structural components. Weighing less than aluminum alloys, composites can add significant fuel savings to next-generation aircraft.
Michael Donnelly, an aerospace composite repair specialist, says IR curing new and refurbished aircraft components and assemblies made of composite materials has many of the same benefits as drying and curing paint and other surface coatings.
“The tolerances for composite temperature profiles used for curing parts are normally extremely tight from start to finish,” Donnelly says. “I have seen convection ovens constructed for that purpose that have ended up being an expensive misstep. On the other hand, the use of a correctly-configured oven or even external heating arrays using highly controllable IR heat sources to tightly match various surfaces may be able to meet those tight profiles more consistently and also accelerate the speed and throughput of curing.”
Intek Corp.
Get curated news on YOUR industry.
Enter your email to receive our newsletters.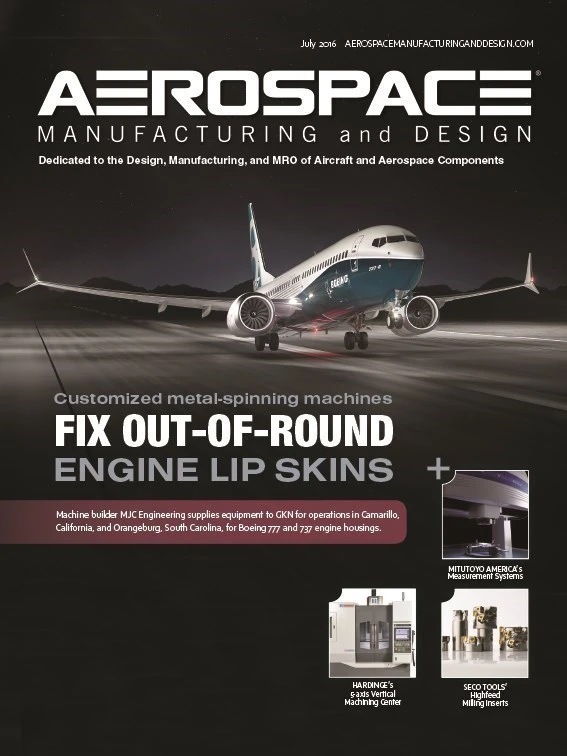
Explore the July 2016 Issue
Check out more from this issue and find your next story to read.
Latest from Aerospace Manufacturing and Design
- Trelleborg acquires Aero-Plastics
- Industrial automation products, enclosed encoders
- #61 - Manufacturing Matters: CMMC roll out: When do I need to comply?
- AIX shows aircraft interiors are a strategic priority for global airlines
- Machine Tool Builders Roundtable: Turn equipment into expertise
- No time to waste: How to machine MedTech parts more efficiently
- The 5 Best and Fastest Spindle Repair Services
- Mill smarter, not harder: How collaboration optimizes production