
While 99% of middle-market manufacturing executives claim to be at least moderately familiar with Industry 4.0 and more than half have developed or are developing an Industry 4.0 strategy, only 5% are currently implementing one. That alarmingly low number comes from a survey commissioned by professional services firm BDO USA LLP that polled 230 executives at U.S. manufacturing companies with annual revenues between $200 million and $3 billion. If major American companies are struggling to apply digital capabilities to physical operations, what are the implications for smaller enterprises?
The inaugural Middle Market Industry 4.0 Benchmarking Survey reveals manufacturers’ intentions are good: 79% reported they have, are developing, or plan to develop an Industry 4.0 strategy. The reality is they face some daunting challenges putting plans in place. Two-thirds of respondents cited poor communication as the biggest barrier to successful implementation.
Eskander Yavar, national leader of BDO’s Management & Technology Advisory Services and Industry 4.0 co-leader, explains, “Too often, organizations embark on a digital initiative but forget about the human element – if internal teams aren’t in sync, implementation of new systems may not go as planned.”
To encourage employee adoption of advanced technologies, 60% of respondents say they are training current employees to give them skills to enable Industry 4.0, and almost as many (57%) plan to hire new people. Even more (63%) plan to use third-party solutions to support Industry 4.0 and two-thirds have hired outside consultants.
As the survey authors note, successful Industry 4.0 adoption requires collaboration between business areas that have historically operated in silos, such as information technology and operations technology. Complicating implementation are legacy technologies and processes that don’t work well together, a problem cited by 64% of manufacturing executives surveyed. Other systemic problems stand in the way of applying Industry 4.0: 63% mention lack of skills or insufficient training, 60% say it’s because of lack of leadership and vision, and 54% blame underinvestment.
“Instilling a company-wide mindset that encourages continuous improvement and willingness to fail is key to ensuring your transformation initiatives don’t lose steam,” Yavar notes.
Manufacturers know that Industry 4.0 can transform their business, and most (69%) are concerned that failure to adequately invest in it will lead to encroachment from non-traditional competitors, a major worry. You don’t have to look far in aerospace to find upstart technologies that could transform the industry with novel concepts for urban air mobility.
Yavar says companies also need to think about adjusting company culture to proactively support innovation. “Short-term mistakes and failures are nearly inevitable, but experimentation is necessary to create lasting, long-term value.” However, he warns, “The window of opportunity is closing fast. Manufacturers who don’t invest in 2019 risk falling behind the curve.” – Eric
Get curated news on YOUR industry.
Enter your email to receive our newsletters.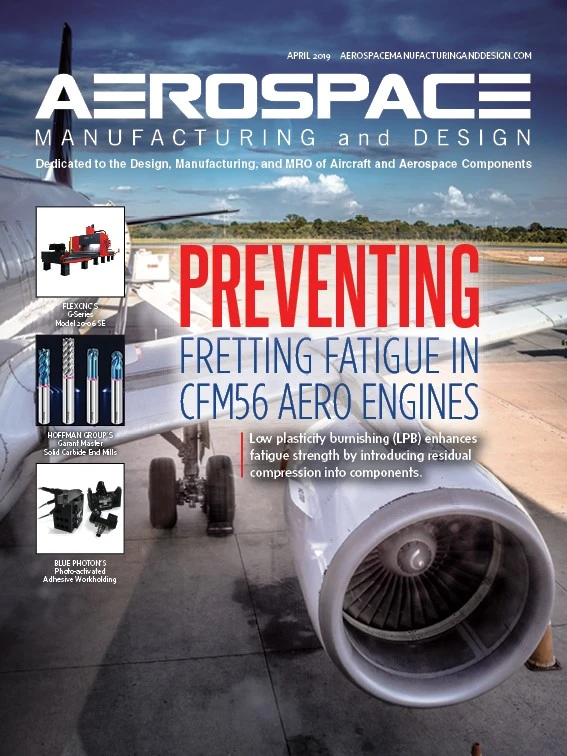
Explore the April 2019 Issue
Check out more from this issue and find your next story to read.
Latest from Aerospace Manufacturing and Design
- Drop in for an interactive webinar on automation in manufacturing
- SW’s wing rib technology for the aerospace industry
- Mach Industries launches Mach Propulsion
- Murata Machinery USA's MT1065EX twin-spindle CNC turning center
- Electra reaches 2,200 pre-orders for its Ultra Short aircraft
- Heule's DL2 tooling for deburring of small bores
- Ralliant to establish global headquarters in North Carolina
- Philatron MIL-DTL-3432 military cables