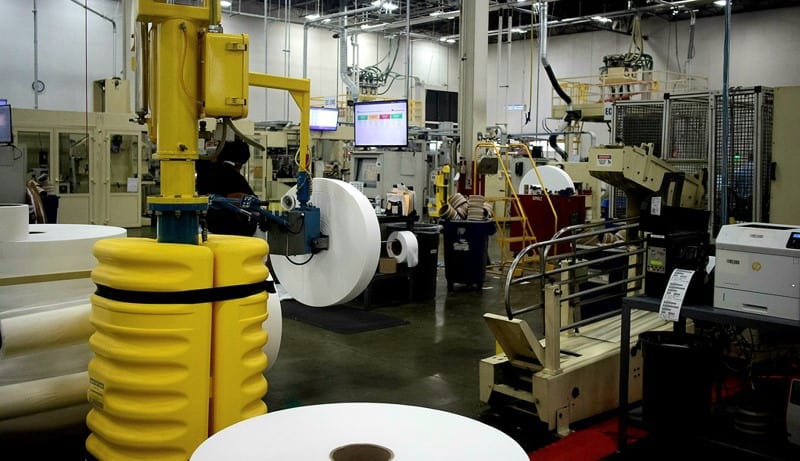
Throughout the last year, the news has been a carousel of disruption, supply shortage, labor gaps, and inflation. The global supply chain is seeing the highest inflation rates in 30 years and there’s no sign of relief. This brings mid-sized manufacturers in the United States to a unique position where revitalizing and digitizing their local factory floor is the logical solution for meeting customer demand while remaining a viable and profitable business.
To address these global disruptions, American policy makers introduced executive orders to help create more resilient supply chains for critical and essential goods. Personal protective equipment and semiconductor chip shortages have highlighted how fragile a global supply chain can be. These issues have impacted the aerospace and defense (A&D) industry with bottlenecks when trying to transport finished items and shortages in bolts, wiring, hoses, and electronics. One focus of the executive orders is shortening the supply chain through reshoring while returning well-paying manufacturing jobs back to the U.S.
Offshoring doesn’t provide flexibility or resilience during disruptive circumstances. Traditionally, offshoring brings more affordable labor and a less expensive product to U.S. consumers; but this is becoming less appealing due to shutdowns in Asian factories, bottlenecks at ports on both ends, and labor shortages throughout the logistics industry. The growing importance of environmental protection standards set by consumers and public companies means foreign suppliers must face audits to ensure they adhere to strict environmental standards. These manufacturing operations have started to return to the U.S. because businesses experienced strained offshore relationships along with a loss of control and visibility, leaving offshore operations closed due to the pandemic and no opportunity to divert production. Looking forward, the global economic outlook for 2022 and beyond is unpredictable. Many manufacturers are considering or already returning to U.S.-based operations. According to one report, 83% of manufacturers are likely or extremely likely to return operations to U.S. soil, up from 54% in 2020. Manufacturers can bring more local jobs and shorten the supply chain by keeping production close to the markets they serve.
However, for mid-sized manufacturers to remain competitive against local and global opposition, they need Industry 4.0 to make reshoring a smoother process on the factory floor.
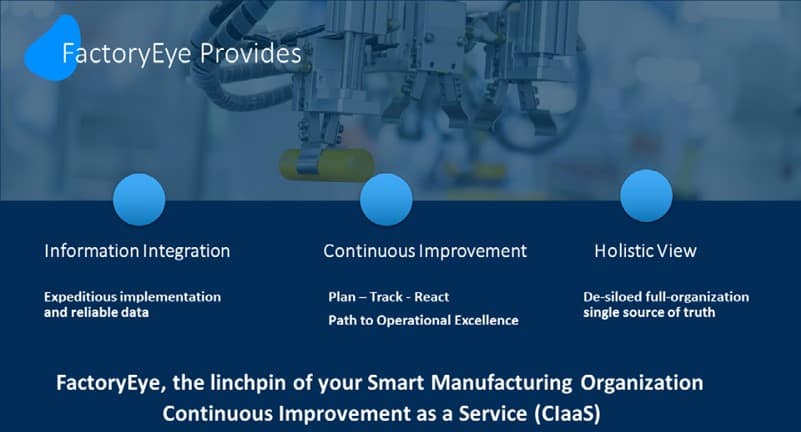
The smart factory era
Industry 4.0 technologies facilitate reshoring by increasing digitization, enabling companies to manage production facilities and supply chains more effectively. Many factory floors in the U.S. don’t have existing infrastructure on machinery for Industry 4.0 solutions, but sensors are a simple install on legacy machinery to acquire actionable data. Manual data collection should be a practice of the past, yet too many manufacturers still collect data by hand, which is tedious, time-consuming, and prone to errors. Benefits of real-time data collection include smart analytics and predictive maintenance to ensure optimal equipment availability and improved product quality. During unexpected disruptions, having data easily accessible and digestible can offer more processing flexibility and agility, decreasing the time it takes to regain control over operations. If a production line is producing a substandard product, sensors can identify the issue sooner, alert the appropriate operators, and adjust the process to reduce waste. Industry 4.0 solutions can quickly transform data from the factory floor into actionable intelligence, offering smooth operations even in a thin labor environment which is crucial during reshoring efforts.
Eliminating data silos
Reshoring isn’t as effective for manufacturers as it could be because without smart analytics, production data isn’t used to its full capabilities. For mid-sized manufacturers hesitant to bring operations back home, embracing an Industry 4.0 strategy and supporting technologies is essential to getting production up and running quickly. Data silos can be created if proper connectivity doesn’t exist between machinery on the factory floor and operational systems. Siloed data can affect a company’s ability to compete since it reduces transparency across operations and hinders collaboration across teams. Although some machines may have sensors, the data may not be getting sent to the right team members to improve the processes. This could prevent manufacturers from taking the necessary actions to correct a production error, creating waste and losing profits.
Inefficient data collection isn’t the only factor that can create data silos. For more mature manufacturers, there can be a variety of systems on the factory floor that were implemented intermittently during the last three decades. These independent, outdated systems can cause a multitude of data silos, but Industry 4.0 can integrate multiple types of data into a centralized format.
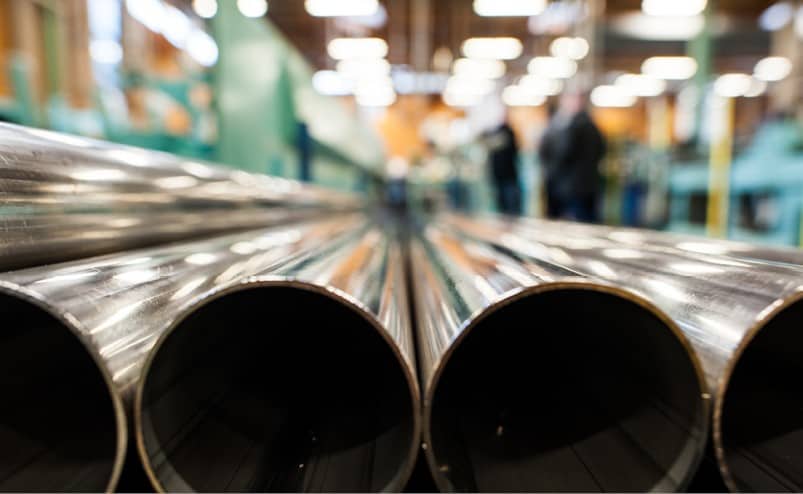
A smarter future with Industry 4.0
Reshoring can bring many high-level manufacturing jobs back to the United States with new opportunities in the modern manufacturing space. Industry 4.0 on the factory floor attracts a more tech-savvy, younger population of workers since these operators are more comfortable with certain technologies since they grew up with smartphones. Digital technologies are paving a new future where machines and people work collaboratively to ensure top efficiency and lower costs with employees having access to more fulfilling tasks. To counter high unemployment, it’s imperative that manufacturers create appealing jobs while reducing workforce risks during reshoring initiatives.
One of the best ways for mid-sized manufacturers to ensure success is by embracing new technologies. Industry 4.0 solutions can bring all information into a single, user-friendly dashboard that encourages team productivity while reducing inconvenient data silos. Real-time data allows for preemptive manufacturing decisions to encourage optimal efficiency.
Manufacturers must find innovative ways to get ahead of local and global competition and Industry 4.0 solutions bring valuable insights into the supply chain during reshoring initiatives.
FactoryEye
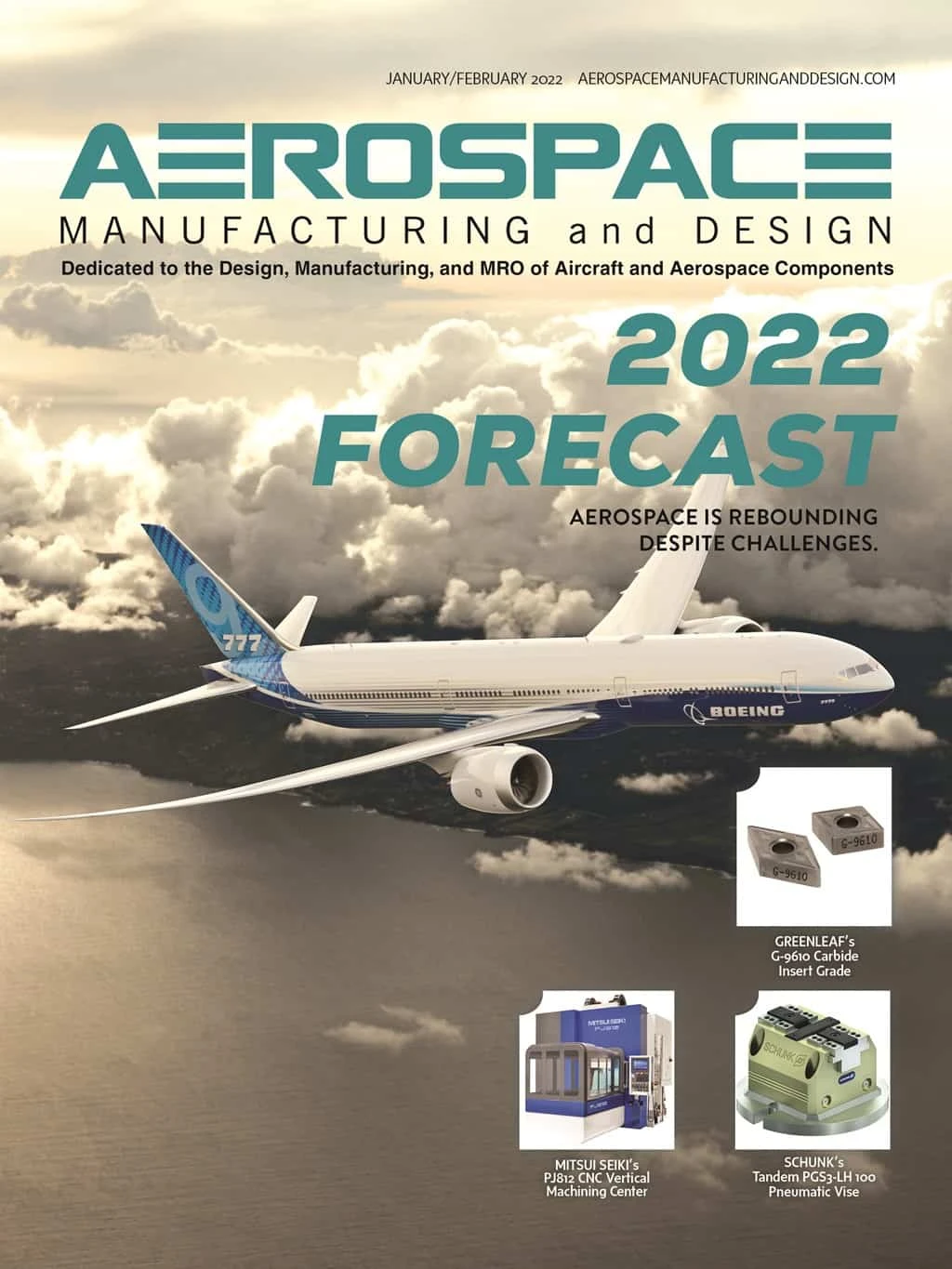
Explore the January February 2022 Issue
Check out more from this issue and find your next story to read.
Latest from Aerospace Manufacturing and Design
- AIX shows aircraft interiors are a strategic priority for global airlines
- Machine Tool Builders Roundtable: Turn equipment into expertise
- No time to waste: How to machine MedTech parts more efficiently
- The 5 Best and Fastest Spindle Repair Services
- Mill smarter, not harder: How collaboration optimizes production
- Be proactive – stay ahead of tariffs and other economic and supply chain curveballs!
- Taiwan’s China Airlines orders Boeing 777X passenger, freighter jets
- Reamer re-tipping extends life of legacy tooling