
A little more than a year ago, I wrote about the alarmingly low rate of middle-market manufacturers adopting Industry 4.0. This year’s survey from professional services firm BDO USA LLP shows a dramatic jump, with 31% of middle-market manufacturing executives now reporting they are implementing an Industry 4.0 strategy, up from 5% in 2019.
BDO’s “2020 Middle Market Industry 4.0 Benchmarking Survey” polled 100 C-level executives at manufacturing companies with annual revenues between $250 million and $3 billion.
What has changed? BDO USA’s National Manufacturing Practice Leader Eskander Yavar explains, “Last year, 32% of manufacturers had developed an Industry 4.0 strategy but hadn’t yet implemented it. Many have since put that strategy into practice.”
Another big change since last year is C-level management identifying as transformation leaders, increasing from 7% to 35%. They’ve replaced business unit heads in charge of transformation, whose numbers dropped from 30% to 6%. As the survey authors noted last year, successful Industry 4.0 adoption requires collaboration between business areas that have historically operated in silos, such as information technology and operations. Realizing the need for strong direction, managers in charge of the multiple silos appear to have taken the reins.
“The shift in responsibility from business unit heads to the C-suite reflects the elevation of Industry 4.0 to an enterprise-level business initiative,” Yavar says. “Digital initiatives often start out as small, isolated pilots. Now that many manufacturers have proof of concept, they’re scaling up to enterprise-wide deployment.”
When the latest survey was conducted, before the COVID-19 pandemic, 67% of manufacturers cited boosting operational efficiencies as a top short-term business objective. Now, Yavar notes, “Facing both COVID-19 disruptions and a recession, manufacturers need to do more with less.”
Boosting operational efficiencies with Industry 4.0 can help manufacturers save money without resorting to layoffs. Reducing waste and increasing speed will allow them to focus more time on revenue-generating activities.
Especially if demand has slowed or production has ceased, BDO’s experts say more innovation with lower operating expenses are key. Industry 4.0 tools that monitor, collect, and report information in real-time – along with advanced analytics and machine learning – can be deployed to better manage performance, more reliably forecast demand, flag anomalies, or perform predictive maintenance or remote repairs.
“Manufacturers that can continue innovating in the recession will be better positioned to achieve breakaway performance when the economy reenters growth mode,” Yavar adds.
Thorough planning, implementation, and innovation aren’t enough, however. Yavar says, “Long-term success for manufacturers hinges not just on developing an Industry 4.0 strategy, but excellence in execution.” Manufacturers that developed Industry 4.0 strategies and executed them well prior to the pandemic “are now in a position to leapfrog their less nimble competitors.”
Calling COVID-19 a reality check for manufacturers that have failed to embrace Industry 4.0, Yavar says, “What may once have been reluctance to invest in Industry 4.0 is now a necessity.” – Eric
Get curated news on YOUR industry.
Enter your email to receive our newsletters.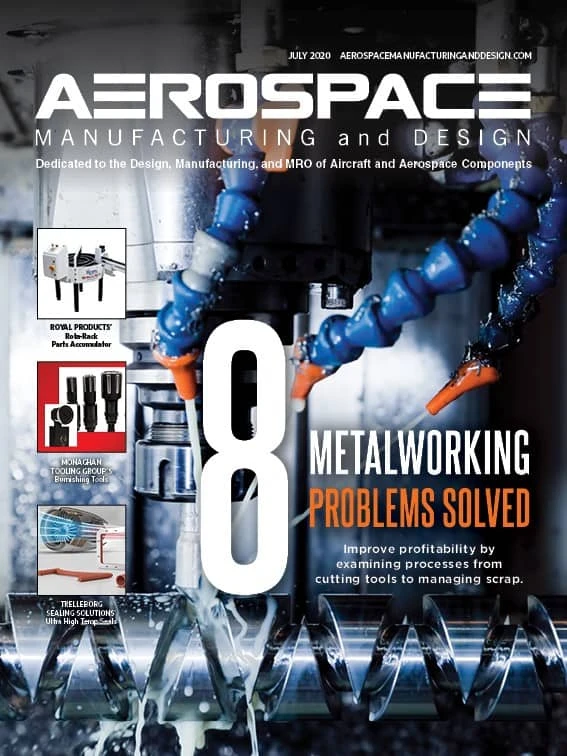
Explore the July 2020 Issue
Check out more from this issue and find your next story to read.
Latest from Aerospace Manufacturing and Design
- Trelleborg acquires Aero-Plastics
- Industrial automation products, enclosed encoders
- #61 - Manufacturing Matters: CMMC roll out: When do I need to comply?
- AIX shows aircraft interiors are a strategic priority for global airlines
- Machine Tool Builders Roundtable: Turn equipment into expertise
- No time to waste: How to machine MedTech parts more efficiently
- The 5 Best and Fastest Spindle Repair Services
- Mill smarter, not harder: How collaboration optimizes production