
More stringent policies on emissions are rapidly being adopted by many countries with projections of a complete ban on automotive internal combustion engines (ICEs) in the Netherlands by 2025 and India by 2030. Automotive manufacturers are accelerating production of electric vehicles (EVs) and plug-in hybrid electric vehicles (PHEVs) to keep up with this demand.
Market forecasts for EVs and PHEVs point toward a promisingly high annual growth rate. The global EV market is estimated to reach almost $46 billion by 2025, a good indication that automakers and suppliers will need to remain in high gear to keep up with technology.
Global automakers will spend $255 billion on research and development (R&D) for EVs through 2023, according to Alix Partners' Global Automotive Outlook study on the future of the auto industry. Several factors are steering the upswing in R&D by automakers, such as the ability to:
First, however, automakers must reduce weight. All vehicles lose efficiency as weight increases, but it’s especially true for EVs because the battery is very heavy. That’s one of the reasons EVs are designed with far fewer parts than traditional ICEs, and those remaining components will feature more complex designs.
Secondly, R&D must continually improve operations to drive down manufacturing costs and ensure safety as next-generation vehicles take the road.
Lightweighting is important for other industries as well, such as aerospace and medical. A small savings in weight on an aircraft can mean big fuel savings. And, since medical implants and devices are integrated into the human body, accuracy and lighter-weight materials must be made to stringent standards. The need for accurate testing in all three industries is crucial.
Casting industry
The need to reduce weight in EVs and PHEVs will naturally lend itself to lighter weight materials such aluminum, magnesium, and carbon fiber. Worldwide, aluminum foundries will benefit greatly from the trend toward lightweight construction. Global aluminum foundry production is estimated to reach 17 million tons by 2020. The use of aluminum in automobiles will double from around 12% to 25% of global consumption with 30 million tons used by 2025.

EVs are relatively simpler to build, with only 20 moving parts versus the 2,000 parts it takes to currently produce a traditional ICE, so there will be an expected decrease in engine and transmission components and an increase in structural components made of light alloys with EVs. Structural applications are being used increasingly in the premium segments for applications such as suspension domes; longitudinal carriers; cross-members; doors; gages; and A-, B-, and C-pillars. In Europe, demand for structural cast aluminum applications increased 65% in 2017. New components will be made from lightweight, more expensive, harder-to-cast materials, and they will be more geometrically complex, two trends that introduce more opportunity for casting errors. When producing aluminum castings, manufacturers must inspect them for internal defects.
This is where Industrial CT can become a great benefit.
Industrial computed tomography (CT)
A leading technology in the medical field since the 1970s, CT has become a powerful observation tool in the industrial realm. A CT scan produces a two-dimensional density map of a cross-sectional slice of an object’s interior. Many 2D slices can be combined to produce a 3D image of practically any part, object, or product of nearly any material. This is critical for any application for which a manufacturer wishes to see inside an object without destroying it.
Today’s industrial CT scanners provide valuable data for initial prototyping and optimizing production processes. They can detect potential part failures, even on larger parts, because CT scanning techniques produce clear images. The images assist manufacturers in fatigue analysis and identify finite cracks and inconsistencies from part to part. Substrate bonding issues, uneven material flow, density, and porosity problems can also be detected through the accuracy of CT images. In post-production, CT screening can improve productivity by eliminating issues likely to cause possible problems in post-production.
CT from design to production

Though seen primarily as a quality assurance (QA) or non-destructive testing (NDT) technique used to monitor build quality, CT can support several phases of the automotive design and build process.
Design – When creating a component, 90% of the work is spent in the design phase. CT can streamline R&D by identifying key information about part designs and how well they match intended geometries – avoiding issues later in the production process. Data can verify flow and strength simulations, reducing time from prototype to finished product.
And, if the new product uses design features from an older part, CT can reverse-engineer components that don’t have updated CAD files. Reverse engineering a part using industrial CT scanning can be faster and more accurate than rebuilding a component from scratch. Scanning legacy parts can generate new, highly accurate CAD models.
Pre-production – Once the design has been completed, tools and molds must be qualified. Industrial CT can detect discontinuities within the part design and quantify findings such as porosity. It can also help qualify molds by confirming the actual parts being produced are in dimensional compliance with specifications.
Quality Inspection – Typical casting flaws can include porosities (pores and blisters), thermal cracking, dimensional changes, and inclusions. NDT testing with industrial CT can detect blowholes and pores, provide geometric measurement of inner structures, and analyze wall thickness. For safety-relevant components in the automotive industry, determining wall thicknesses following casting process and finish machining provides critical information about the material’s stability and thermal conductivity.

Cast parts that don’t meet specification can be sorted out early. Engineers can use the data to draw conclusions regarding casting quality from the types of flaws found, thereby increasing productivity by initiating appropriate improvement measures.
Conclusion
With so much riding on the reliability and safety of next-generation vehicles, quality control is extremely important. Industrial CT can go a long way in streamlining the process from research and development through final production. Trust the power of CT to provide a roadmap for success that leads to a bright future for automotive manufacturers and other highly regulated industries such as aerospace and medical.
About the author: Yxlon Business Development Manager for CT Dirk Steiner began his career with Yxlon, after graduating from Fachhochschule Hamburg.
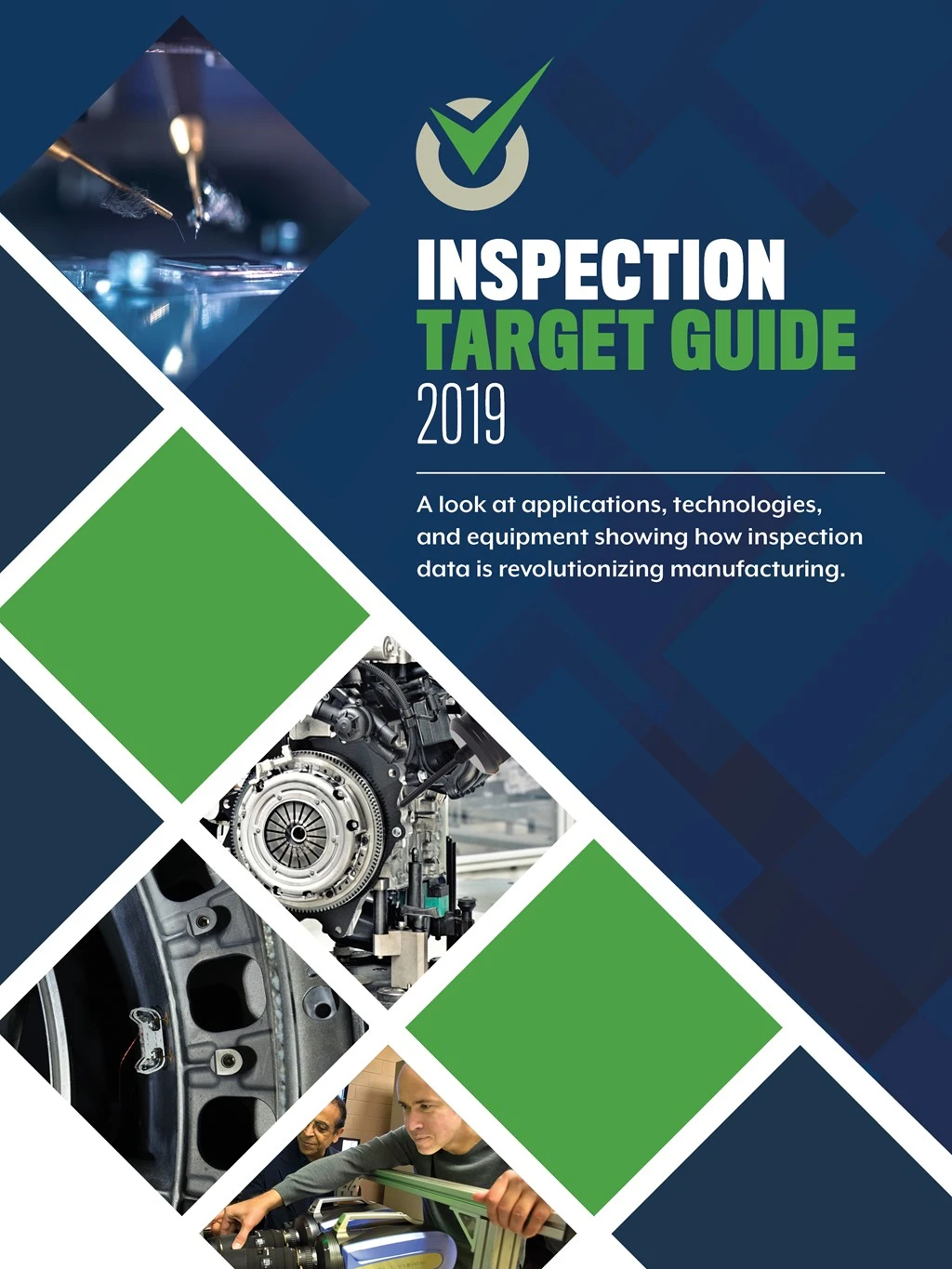
Explore the Inspection Target Guide Issue
Check out more from this issue and find your next story to read.
Latest from Aerospace Manufacturing and Design
- Drop in for an interactive webinar on automation in manufacturing
- SW’s wing rib technology for the aerospace industry
- Mach Industries launches Mach Propulsion
- Murata Machinery USA's MT1065EX twin-spindle CNC turning center
- Electra reaches 2,200 pre-orders for its Ultra Short aircraft
- Heule's DL2 tooling for deburring of small bores
- Ralliant to establish global headquarters in North Carolina
- Philatron MIL-DTL-3432 military cables