More than 90% of milling tools are 1" or less in diameter, so producers, suppliers, and consumers have much to gain by optimizing cutting tool technologies in this range. At ISCAR, experience and confidence, generated from decades of tool development, lead to questions of how best to measure tool value. Considering how a tool is going to be used – the machining approach and subsequent cutting parameters based on workpiece geometry ensures that most of the tool’s cutting edge can be used. The resulting high utilization usually means high productivity and positive impact on cost per unit (CPU).
Underutilization, misapplication Machinists often see used cutting tools that only have wear on a fraction of the cutting edge. Cutting tools capable of a 1/2" depth of cut or greater are sometimes only used at cutting depths of 0.100" or less. When considering the average solid carbide end mill capable of 1×D or, more likely, 2×D flute length – a cutting depth of 0.050" to 0.100" results in 5% to 20% utilization. That prime example of misapplication shows that much of what’s being purchased goes unused. If an application requires only 0.050" to 0.100" depth, switching to an interchangeable solid carbide or indexable solution designed for smaller depths of cut could dramatically improve CPU.

NANO indexable mills
Indexable milling tools require screws that clamp the insert, and they tend to be less accurate than solid end mills. They also demand more room to create pockets and threaded holes for the insert screw, resulting in tools with only one or two flutes in 3/8" diameter and smaller. ISCAR’s NANMILL is an innovative design which addresses these traditional shortcomings. The ability to accurately press such a small insert, combined with unique dovetail clamping that eliminates the insert’s screw hole, produces 5/16" end mills with 2 flutes and 3/8" end mills with 3 flutes.

Ease of use
Clamping/indexing miniature milling inserts may appear to be cumbersome, but ISCAR designers developed systems to ensure ease of use:
- Magnetic key – ensures inserts are not dropped, also used for screw tightening
- Large insert screw – result of dovetail clamping without passing through the insert
- Interchangeable Multi-Master Heads – easy to remove and replace, keep machine spindle running while insert clamping/indexing is performed over a workbench
For applications that require shallow depths of cut (0.100" or less), NANO indexable technologies can substitute for solid carbide end mills, reducing tool costs and CPU. NANMILL is also an excellent fit for machine tools with smaller spindles (BT30), Swiss machines, and lathes with driven tool stations.
For more info. http://www.iscarmetals.com
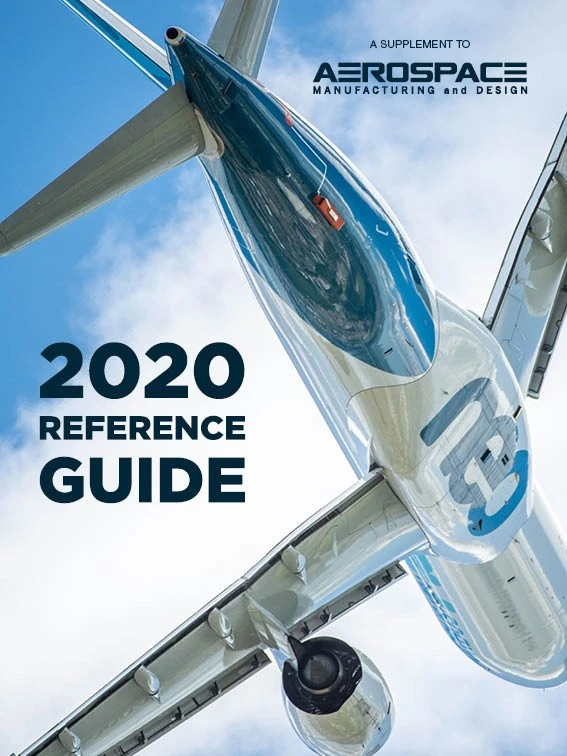
Explore the AMD Reference Guide 2020 Issue
Check out more from this issue and find your next story to read.
Latest from Aerospace Manufacturing and Design
- Piasecki acquires Kaman's KARGO UAV program
- PI Americas’ long-travel XY piezo nanopositioners-scanners
- AAMI project call submission deadline extended to May 12
- Jergens launches cast iron tooling column additions
- Airbus to acquire assets relating to its aircraft production from Spirit AeroSystems
- FANUC America's Cobot and Go web tool
- Chicago Innovation Days 2025: Shaping the future of manufacturing
- High-density DC/DC converters for mission-critical applications