
The HF4 (ENMX06 and ENMX09) portfolio covers 0.625" to 1.500" end mills, face mills from 1.500" to 6.000", and nominal and oversized modular solutions from 0.625" to 1.500"; grades and geometries for everything from mild steels to the most difficult heat-resistant super alloys. For users of the ISO-standard solution SDMT/SDMW insert, YG-1 has the same grade and geometry portfolio as the HF4, plus cutter bodies. For face milling, the FM10 (PNMU) combines versatility and productivity, enabling roughing to finishing with the same insert and cutter.
YG-1
EASTEC Booth #5327
Thread cutting and forming taps

The thread cutting and forming taps product line encompasses three performance levels, allowing manufacturers to cost-effectively match the right tap to their application. The combination of superior base materials, advanced coatings, and special edge preparations lets the taps generate precision threads while providing excellent chip evacuation, shorter setup times, and longer tool life.
The three performance levels encompass the product designations T32 and T34 in thread cutting taps and T33 in forming taps. At the base level are universal general-purpose taps. The second T34 mid-level range consists of higher performance taps working well in various materials, making them well-suited for high-mix/low-volume production environments with constantly changing parts and materials. The top performance level is material-specific thread cutting and forming taps such as those optimized for steel or other advanced materials.
Seco Tools
High speed vertical precision center

The VL30 Series high-speed vertical machining centers were developed specifically for high-speed/high-precision hard milling of mold components as well as graphite and copper tungsten electrodes. The VL30 Series features high thrust, high-efficiency linear motor drives for the X-, Y-, and Z-axis for machining hardened tool steel alloy components. The 5-axis versions use direct drive rotary axes for smooth and perfectly controlled complex contouring. Delivering up to 1,574ipm cutting feed rate with 1G acceleration/deceleration, the line provides superior speed and motion control in high-speed point milling in multi-axis contouring applications. For accuracy, the precision glass scale feedback system detects 0.1μm increments.
The VL30 line has a proven track record of machining high-precision mold inserts for a variety of applications for medical, packaging, industrial, and aerospace manufacturers.
The upgraded offerings include advanced features for process automation, workpiece and tool handling, and the Fanuc 31i-B with i-HMI operator interface – making it easier to realize improved output and profitability. The latest Graphite Package option allows customers to machine completely dry with no risk of electrode contamination or premature machine wear. All versions allow simple integration with robotics and in-process part inspection.
Available in three models, the VL 30-5X 5-axis machining center, VL 30, and the larger VL 50 3-axis versions, this series features a 15hp 50,000rpm spindle accepting HSK E25 tooling for precise roughing and ultra-fine finishing. An integrated tool changer holds up to 90 tools.
Specifications include 7.9" x 11.8" x 7.9" X-, Y-, and Z-axis travels, 11.8" x 15.8" table size and a compact 53" x 128" footprint.
Enhanced production features include a 4-point leveling bed, finite element analysis-designed main components, hand-scraped castings for excellent machine geometry, and superior chip and dust evacuation with a choice of solutions to suit most needs.
Mitsui Seiki USA
CBN coating technology for hard turning applications

KBN020 general purpose CBN grade is for applications ranging from continuous to heavily interrupted machining. Using new layering techniques, Kyocera developed the Megacoat Tough coating technology combining a highly wear-resistant layer on the surface adhered to high-content CBN to toughen the edge for greater fracture resistance when encountering interruptions. The adhesion layer is laminated between the wear-resistance layer and the CBN to reduce layer peeling for longer tool life and stable machining. Providing excellent wear and fracture resistance delivers more flexibility, range, performance, and tool life when turning hardened materials.
Kyocera Precision Tools
PMTS Booth #7027
Femtosecond laser solutions

AgieCharmilles Laser S 1000 U fs and AgieCharmilles Laser S 1200 U fs are now equipped with a fiber femtosecond laser. This will ensure a laser machining process capable of creating fine details with enhanced quality while maintaining high performance. It allows processing a wider range of materials that only femtosecond laser sources can machine efficiently, such as ceramics, glass, sapphire, etc.
Users will maintain flexibility thanks to the ability to switch seamlessly between nanosecond and femtosecond laser sources in the same machine in the same job. Depending on the application and desired results, it’s possible to use the strengths of each laser source for the best combination of quality and productivity.
GF Machining Solutions
EASTEC Booth #1728
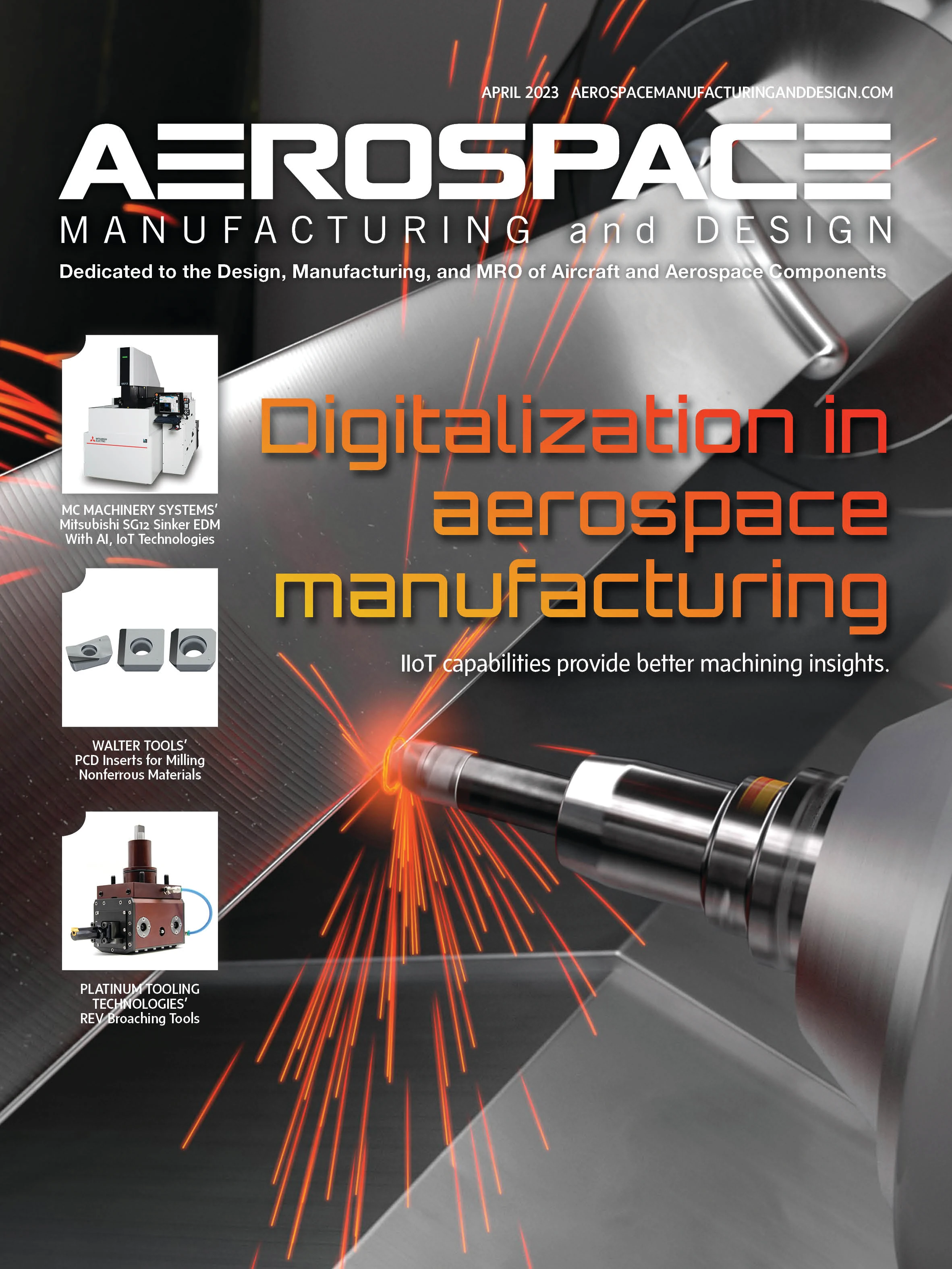
Explore the April 2023 Issue
Check out more from this issue and find your next story to read.
Latest from Aerospace Manufacturing and Design
- Revitalizing the Defense Maritime Industrial Base with Blue Forge Alliance
- Safran Defense & Space opens US defense HQ
- Two miniature absolute encoders join US Digital’s lineup
- Lockheed Martin completes Orion for Artemis II
- Cylinder CMMs for complex symmetrical workpieces
- University of Oklahoma research fuels UAS development
- Motorized vision measuring system
- Everyone's talking tariffs