
IMTS – The International Manufacturing Technology Show – returned to Chicago’s McCormick Place as a live, in-person event in 2022. The desire to see technology first-hand, in one location, and get advice from industry experts prompted more than 86,000 to attend – a strong showing as the world emerges from a pandemic and grapples with supply chain and workforce challenges.
While metal removal, additive manufacturing, tooling/workholding, metrology, controls, and other technologies had their showcase areas, automation was evident in all four halls. Robots and collaborative robots (cobots) were featured in numerous booths, with machining centers highlighted in work cells, equipped with bar feeders, pallet systems, and automated tool holders to an extent not previously seen. Fueling the focus on automation is the need to maximize production with fewer skilled workers available – a need felt by small job shops to major original equipment manufacturers (OEMs). Automation is increasingly viewed as necessary for a company’s competitive edge. There was evidence that many of the attendees were looking for a solution to improve production at their shops now, and ready to buy, not just coming to see what’s new.
Robots, cobots, collaboration

Automation in the form of robot arms, cobots – free-standing or attached to automated guided vehicles (AGVs) – was on exhibit performing welding, tool-setting, palletizing, inspection, bin-picking, grinding, polishing, and other tasks.
Universal Robots debuted its UR20, designed to provide up to 30% more speed and torque than previous cobots, with payload of 20kg (44.1 lb) and reach of 1,750mm (68.9”), it can stack pallets up to 2m high. Engineered to reduce weight while preserving rigidity, the 64kg UR20 is compact enough to be mounted directly on a machine.
Anders Beck, VP of innovation and strategy at Universal Robots, says many robotic applications such as machine tending are similar, so you don’t need a customized solution in every case. “Customers now want a standardized, mature design at a fixed price with one-day setup and training,” he explains. Universal Robots is working with 299 partners now, developing interfaces for their robots. Beck sees the market evolving, where robot manufacturers develop the platform for others to innovate process applications, much in the way mobile phones can support widely diverse apps.

One example of growing robotics collaboration, OnRobot’s One-System Solution allows its end-of-arm tool (EOAT) to interface with any leading robot arm through a quick-change mechanical and electrical interface. Further enhancing ease of implementation, OnRobot’s D:PLOY application uses a dashboard to manage a cobot or light industrial robot arm along with tooling, sensors, and other devices. Once users define the robot’s workspace and enter workpiece attributes, D:PLOY automatically generates the program logic, signal exchange, event handling, path planning, and real-time monitoring.
“System integrators can take on more projects with existing resources. Robot manufacturers benefit from dramatically greater accessibility for their products. And end users gain powerful new abilities to implement, manage, and redeploy automation across their facilities,” says Kristian Hulgard, general manager of OnRobot’s Americas division.

Expanding on the collaborative theme, partners demonstrated three-finger grippers with a payload up to 15kg and gripping force from 10N to 240N, an off-the-shelf electric parallel gripper, and a compact electrical vacuum gripper that needs no compressor or air supply.
https://www.universal-robots.com; https://onrobot.comSolutions, not just tools

Concerns that supply chain disruptions would prevent many machine tool manufacturers from being able to fill their booths were unfounded. On display at this year’s IMTS were machines as small as a microwave – Bantam Tools’ Explorer desktop CNC milling machine – to giant machining centers such as Niigata’s HN800V heavy duty boxway machining center that would nearly fill a one-car garage. https://www.niigatausa.com/our-products/hn800v; https://www.bantamtools.com
In an exclusive interview with GIE Media’s Manufacturing Group publications, the president of DN Solutions (the former Doosan Machine Tools) Wonjong Kim says a machine only cutting metal is not a 100% solution for the customer. “Automation is key now, it’s transformative. Some customers are still reluctant to employ it, but automation is fundamental, not optional, from my perspective, if you want to stay in business.”
Many of the 15 DN Solutions machines on the floor, including the Puma and Lynx lines, featured automation, such as single and multi-level automatic pallet changers. DN Solutions plans to open a new tech center by Q1 2023 near Chicago’s O’Hare Airport. https://www.dn-solutions.us
Additive grows

3D printing and additive manufacturing (AM) technology has grown into a major occupant of the front of McCormick’s West Hall. While the focus formerly was on rapid prototyping in polymers, the emphasis has moved to making production parts in metal. Ankit Saharan, Ph.D., senior manager metals technology for EOS North America explained aerospace has been a fast adopter of AM, especially the low earth orbit and defense hypersonics sector, where humans aren’t passengers. Faster design, more design freedom, the willingness to fail faster and move on, and supply chain resiliency (more suppliers) make AM attractive. “There’s less doubt about the process, but the technology still needs time to generate trust on part qualification versus traditional methods such as casting or cutting,” Saharan explained. https://na.eos.info
Bryan Crutchfield, VP and general manager, Materialise North America, spoke to data security within distributed manufacturing. Traditional manufacturing requires data security, but data integrity and security is even more important in AM. As companies transition from centralized production to distributed production, they want to make sure their design and production data is secure. Built on 30 years’ of 3D printing experience, Materialise’s CO-AM open software platform gives manufacturers cloud-based access to tools that allow them to plan, manage, and optimize every stage of their AM operations to use AM for serial manufacturing and mass personalization.
“We think this will help customers differentiate themselves in the market. AM continues to evolve. Your customers and your competitors have started using it, and if you don’t start, you’re going to fall behind. If you’re not ready, your customers will go to someone who is.” https://www.materialise.com
Get curated news on YOUR industry.
Enter your email to receive our newsletters.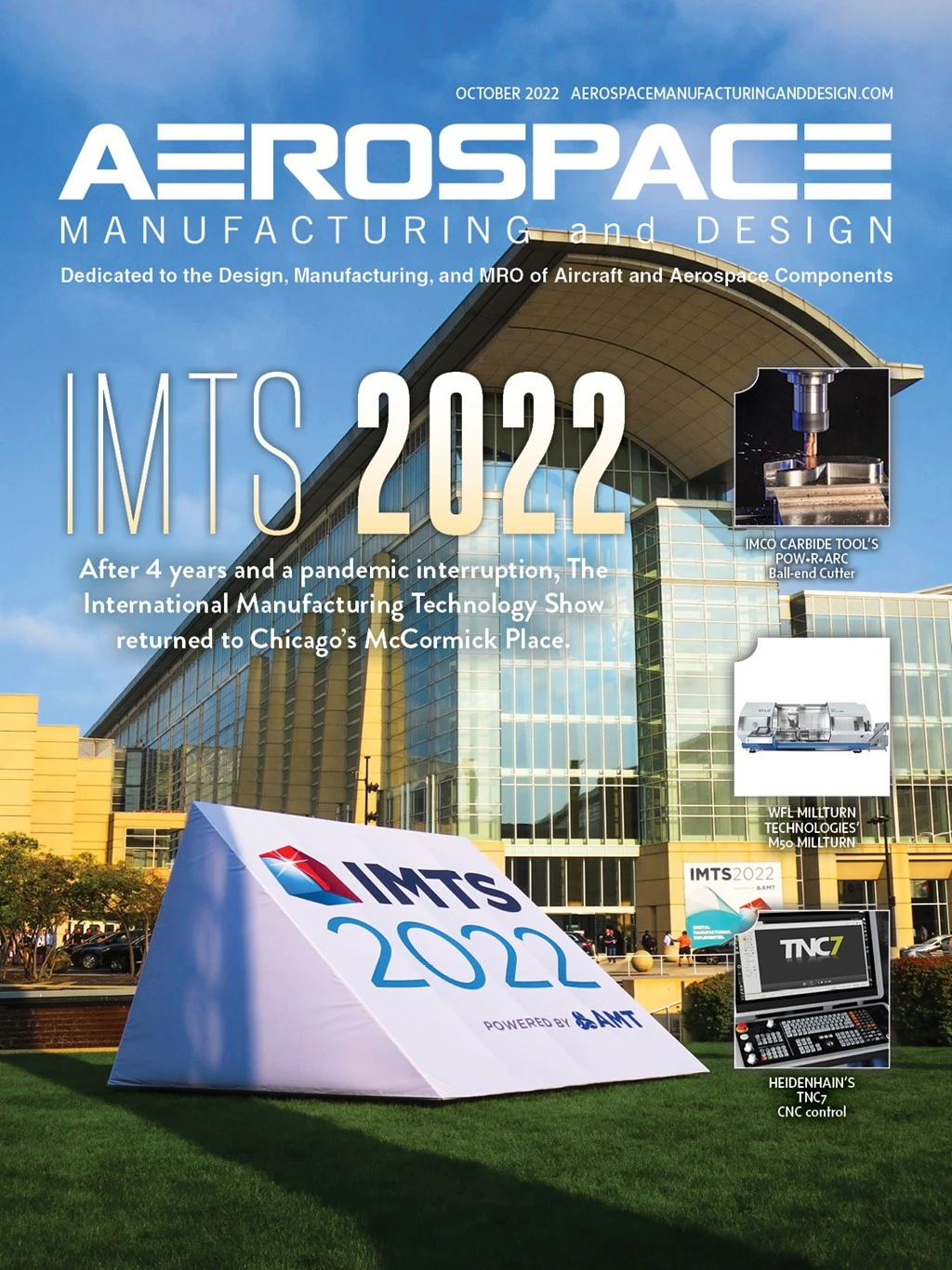
Explore the October 2022 Issue
Check out more from this issue and find your next story to read.
Latest from Aerospace Manufacturing and Design
- AAMI project call submission deadline extended to May 12
- Jergens launches cast iron tooling column additions
- Airbus to acquire assets relating to its aircraft production from Spirit AeroSystems
- FANUC America's Cobot and Go web tool
- Chicago Innovation Days 2025: Shaping the future of manufacturing
- High-density DC/DC converters for mission-critical applications
- #59 - Manufacturing Matters: Additive manufacturing trends, innovations
- ACE at 150: A legacy of innovation and industry leadership