
Traditionally, aerospace fasteners go through centerless grinding to achieve the required diameter. Using 50-year-old technology, most of these processes use infeed ground at the rate of one piece per cycle. With fuel costs and other considerations putting increased emphasis on lighter, titanium alloys in fastener production, centerless grinding has become even more challenging.
John Bannayan, president of Glebar, offers his thoughts on current challenges in the industry and how manufacturers can combat these hurdles.
AM&D: What are the challenges facing the aerospace industry?
JB: To improve aircraft range and reduce greenhouse gases, the major airplane manufacturers have increased the use of lighter materials such as carbon fiber and titanium in aircraft construction.
It all comes down to uptime and reduced part price. Aging centerless grinding equipment, spare parts availability, and lack of field service technicians to service the old equipment lead to increased downtime which compresses margins and reduces profits. Old equipment is also more troublesome due to lack of automation.
Titanium is a difficult material to grind. It needs to be cut and not rubbed. It also has a tendency to burn, reducing the material’s strength. The Glebar GT-610 CNC with the 10" diameter grinding wheel allows for more chip clearance than a 24" wheel, flushing heat away from the parts, providing excellent cutting action, better coolant penetration, and less tendency to burn.
AM&D: What are the challenges for aerospace fasteners?
JB: The vast majority of fasteners have to be sized by grinding. Using a rebuilt grinder yields a single piece per cycle. An aggressive grind has the potential for burning, which introduces micro-fractures in parts and causes fastener failure.
AM&D: What makes titanium so difficult to grind?
JB: Its material composition dulls grinding wheels. It also absorbs heat and is flammable. Since abrasives are used in centerless grinding, a dull wheel tends to rub the material from the surface rather than cut it, which increases heat and causes deformity. This also makes size control challenging.
AM&D: How can manufacturers combat these hurdles?
JB: By cooling components as they grind to remove the heat from the point of contact between the part and the grinding wheel. Cooler parts are an indicator that the grinding wheel abrasive is a good match for the application.
We have worked with a number of fastener suppliers. The competing processes were old 1950s machines retrofitted to run one part at a time.
Engineers have successfully modified the GT-610 CNC machines to grind a range of materials including titanium alloys at large volumes and in the variety of shapes, sizes, lengths, and diameters required for advanced aerospace fasteners. This centerless grinding machine can infeed grind as many as eight fasteners per cycle with precision and accuracy, more than quadrupling the output of other centerless grinders.
AM&D: How did Glebar configure the machine to grind titanium alloys at large volumes?
JB: TheGT-610 CNC can produce multiple components per cycle in a highly automated cell. Setup is the challenge fastener manufacturers encounter when centerless-grinding multiple parts per cycle. Our solution is a patent-pending, lateral, work-rest blade axis to control flush-head angles – the Quick Change Gripper System – and our offline P4K gaging system.
Our machines are designed with rapid changeover of automation elements, so a grinding wheel exchange can take 15 minutes rather than hours as on larger machines. The control is sophisticated yet simple to operate, reducing the skill required to run the equipment and allowing operators to run many machines at once.
In centerless grinding, tooling for a component consists of two grinding wheels mounted on opposing spindles and a work-rest blade that supports the components. The grinding wheels are shaped using diamond tools to conform to the component. The raw component lies on the work rest support and the smaller grinding wheel pushes the part into the wheel in the larger form, producing the desired shape.

The work-rest blade can be pulled out of the machine using two screws. And the blade height – a critical setting on the machine – can be adjusted using a wrench. The grinding wheel and work-rest blade are mounted on independent precision slides, further simplifying machine setup.
Engineers have worked very hard to come up with a centerless grinding solution for the fastener industry that performs extremely well when running large volumes of the same part as well as short runs that require quick changeover. The Glebar quick change gantry system can be changed from one part to the next within a couple of minutes and wheels changed within minutes. For high production runs, the GT-610 CNC excels. With high Cpk’s [in Six Sigma quality methodology, the process capability index] and Ppk’s [process performance index] and in-line gaging available, the process is extremely stable. Due to its ability to run multiple parts per cycle with infrequent dressing frequencies, it’s a candidate for large volume programs.
AM&D: Can you share any examples?
JB: In a recent fastener study, the customer was running one part at a time and had to sort through parts to determine quality of an entire batch. Our engineers provided a turnkey system and in-line gaging, automatically compensating for the key diameter by station, to improve quality control. Redressing was at a minimum compared to their rebuilt 1950s vintage grinder, and Cpk’s and Ppk’s were very high, meaning the machine was consistent and repeatable.
Glebar Co.
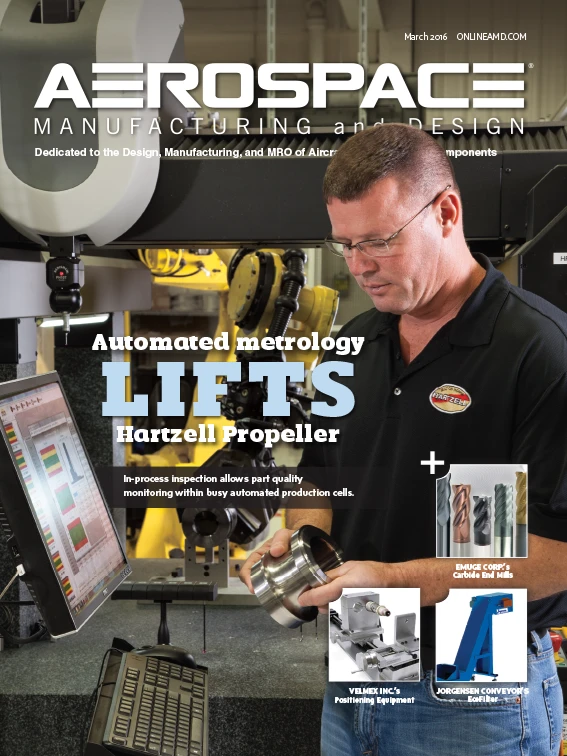
Explore the March 2016 Issue
Check out more from this issue and find your next story to read.
Latest from Aerospace Manufacturing and Design
- Safran Defense & Space opens US defense HQ
- Two miniature absolute encoders join US Digital’s lineup
- Lockheed Martin completes Orion for Artemis II
- Cylinder CMMs for complex symmetrical workpieces
- University of Oklahoma research fuels UAS development
- Motorized vision measuring system
- Everyone's talking tariffs
- Boom Supersonic to launch Symphony engine testing in Colorado