
An estimated 200 billion fasteners are used per year in the U.S., each having a similar function – join two or more parts together and transfer loads from one part to another. When design engineers specify precision-machined fasteners for military, aerospace, or aircraft assembly, they must consider many factors to ensure the end product is high-quality, accurate, and cost effective. One very important consideration is the accurate and consistent geometry of threads.
Thread geometry
Product designers and engineers typically specify fasteners based on the shear or tension that the part will be exposed to, loads that will be transferred, required materials, and operating environments. For high precision applications, external and internal parts must be designed and manufactured for accuracy and strength, tolerances, and resistance to wear and corrosion. Loads, pressure, and operation requirements may vary depending on the application, but once these factors have been identified, engineers can calculate and specify the desired thread geometry.
Like any three-dimensional object, threads are characterized by geometric measurements and dimensions, including pitch, lead, depth, and diameter (major, minor, pitch, and root diameters). Geometric measurements, combined in the design specs and prints, are known as the thread form.
How internal and external threads fit together is almost entirely impacted by thread form. In aerospace applications, the standard unified and metric thread form is 60°, and thread fit falls into the category of Class 3A and 3B fit (A indicates external threads and B indicates internal threads). Class 3 is the most critical and requires the tightest tolerances. Due to the high importance of accurate and consistent threads, there are ways designs can be improved to achieve the required accuracy and decrease costs and production times.
Machining methods

Product designers typically take time to understand the application and calculate the dimensions needed for threads to comply with requirements. Many are confident with their geometric specifications, and that when they submit them to a machinist, they will be produced as desired. However, there are factors in the machine shop that can compromise thread consistency including poor tool quality, calibration inaccuracy, and machining process. For fasteners, product designers should be aware that multiple machining processes exist that will yield significantly different end products in terms or quality and costs.
Subtractive machining. Subtractive processes remove material from a blank workpiece. During thread cutting, a sharpened cutting tool cuts away the extra material with each pass leaving behind the newly-formed threads.
Thread cutting is typically chosen for applications that favor full or very deep threads, when the blank is uneven or unpolished, or when lower quantities are specified. Threading methods do not always provide a great enough angle to form the deep, non-precise threads that cutting can.
However, subtractive processes make it difficult to achieve precise thread geometry and tight tolerances. Product designers must select alternative machining processes to meet the components’ application and operation requirements.
Thread rolling. This cold-working method uses hardened steel dies to form threads by applying force to the surface of a blank workpiece. The cold working, or work-hardening, nature of the process allows machining to be done at room temperature. Rolling increases tensile strength of threads, making them harder and more compact.

Unlike subtractive machining methods, such as thread cutting, material is not removed during the rolling process. This leaves the natural grain structure of the material intact and free of imperfections. Rolling provides the very smooth finishes with increased shear strength.
Most threaded aerospace parts require uniform surface finishes and uniform thread geometry to increase strength and prevent galling, a form of wear most commonly resulting from excessive friction. This can be a costly issue that leads to the loosening, seizing, and stripping of threads. Uneven thread surfaces are very susceptible to galling because there are more opportunities for sliding. Roll-threaded parts can achieve uniform surfaces with thread tolerances as precise as ±0.0001", helping to eliminate galling.
Precision for exotic metal machining. Unlike many commercial-grade components, aerospace fasteners are made from specialized or exotic metals, such as titanium or Inconel. Titanium is preferred for these applications because it is lightweight with a much higher strength-to-weight ratio than other metals. It also resists corrosion and performs reliably under high temperatures. Titanium parts have tensile strengths of up to 160ksi and shear of up to 95ksi, physical properties that are desirable for aerospace assembly components, but make titanium difficult to machine.
Many machining processes, including cutting, cannot achieve the accurate dimensions and uniform surfaces required for these applications, especially when it applies to titanium and other exotic metals. When cut, these metals will typically fracture and produce chips, flakes, or microscopic impurities that can cause surfaces to gall. However, the extreme pressures from rolling dies can accurately form threads on these difficult-to-machine metals. Although these materials are very hard and will not easily deform, they typically roll very well, providing the uniform surfaces, tight tolerances, and accurate thread geometry required by the application.
Cost, accuracy during mass production
Because of the high demand for bolts, screws, and threaded fasteners, designing parts for mass production is very important. In terms of quality and cost, thread rolling is a preferred machining process for high-volume production runs.
Flat or rounded thread rolling dies do not have the sharpened edge like cutting tools. During subtractive methods, cutting edges will eventually wear down and require periodic sharpening. Production is temporarily suspended for the tools to be sharpened and reset. This down-time drives up machining time and costs. Thread rolling is a continuous process, and many thread-rolling machines can produce thousands of parts per hour at high speeds.
High-volume thread rolling is also a preferred process for dimensional and geometric consistency. As cutting tools wear down, the dimensions of the threads can fluctuate. Geometric inconsistencies, even at the slightest level, can compromise thread form for assembly components. Requirements may vary, but many standards require in-depth inspection of geometric dimensions following machining. Machine shops use inspection tools such as thread gages, micrometers, and optical comparators to ensure thread accuracy. Destructive test sampling is often used to check for defects, and thread pitch is inspected under magnifications up to 500x.
Machinists still inspect and monitor the rolling process during production, but for the most part, once the dies are properly lined up and calibrated, rolling is highly consistent and repeatable, so in production runs, the dimensions of the first part are as precise as the last.
Vallorbs Jewel Co.
About the author: Kenneth Rinier is the general manager of Vallorbs Jewel Co., a precision parts machining company, and he can be reached at quote@vallorbs.com or 717.392.3978.
Get curated news on YOUR industry.
Enter your email to receive our newsletters.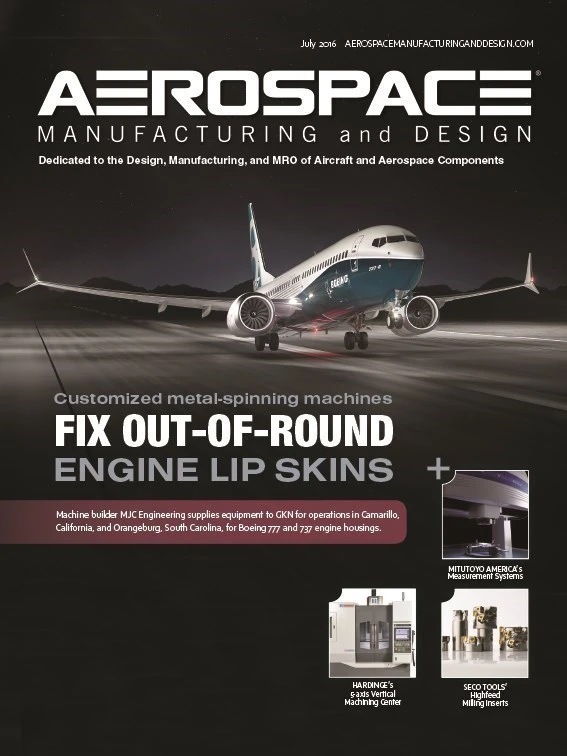
Explore the July 2016 Issue
Check out more from this issue and find your next story to read.
Latest from Aerospace Manufacturing and Design
- Heart Aerospace relocates to Los Angeles
- Fixtureworks introduces Stablelock Clamps
- Piasecki acquires Kaman's KARGO UAV program
- PI Americas’ long-travel XY piezo nanopositioners-scanners
- AAMI project call submission deadline extended to May 12
- Jergens launches cast iron tooling column additions
- Airbus to acquire assets relating to its aircraft production from Spirit AeroSystems
- FANUC America's Cobot and Go web tool