

As we are all learning how to live during this pandemic, there are ways that we can improve our part quality and not spend a lot of money.
Often when we experience quality problems on the shop floor, it’s due to poor tooling issues or the incorrect tool holder being used. When visiting customers as a tooling salesperson, we see tooling used by the operators in poor working condition. If we look at turning tools for instance, we recognize that the tool has been involved in a wreck on the machine and the nose of the tool is damaged, allowing the shim to be unsupported under the nose. If this is the case, replace the toolholder because this type of condition creates vibration in the tool and allows for a poor finish or difficulty holding size and/or finish.
If the machine has been involved in a wreck, it’s important to inspect the machine to see that it’s still on center. There are numerous ways to inspect this and see. The easiest way is to face a bar end and look to see that the machine is on-center and doesn’t leave a bump at the center of the bar. Some of today’s machines have alignment pins in the turret. If your machine has these pins, check to make sure these pins are not sheared or broken. If so, replace them immediately.
Often when we experience quality problems on the shop floor, it’s due to poor tooling issues or the incorrect tool holder being used.
Milling cutters are also tools that need to be maintained and inspected for damage. Many cutters no longer use shim seats in the cutter itself. Therefore, we need to make sure there is no damage in the pocket. This would include making sure there are no burrs on the floor of the seat as well as checking for any damage to the cutter wall. Any issues in these areas will not allow the insert to seat properly, harming finish and tool life.
Poor tool maintenance can lead to poor tool life. Poor tool life leads to down time, so make sure to set up a proper tool maintenance program in your shop. That will allow you to improve the uptime on your machine and ensure the quality of your parts meet specifications expected by your customer.
Keep in mind, “An ounce of prevention is worth a pound of cure.”
CMR Consulting

Mike Ramsey, president of CMR Consulting, retired from Kennametal Inc. as vice president, global machine tool industry sales, after 39 years of service in sales and marketing. He can be reached at miker2468@aol.com.
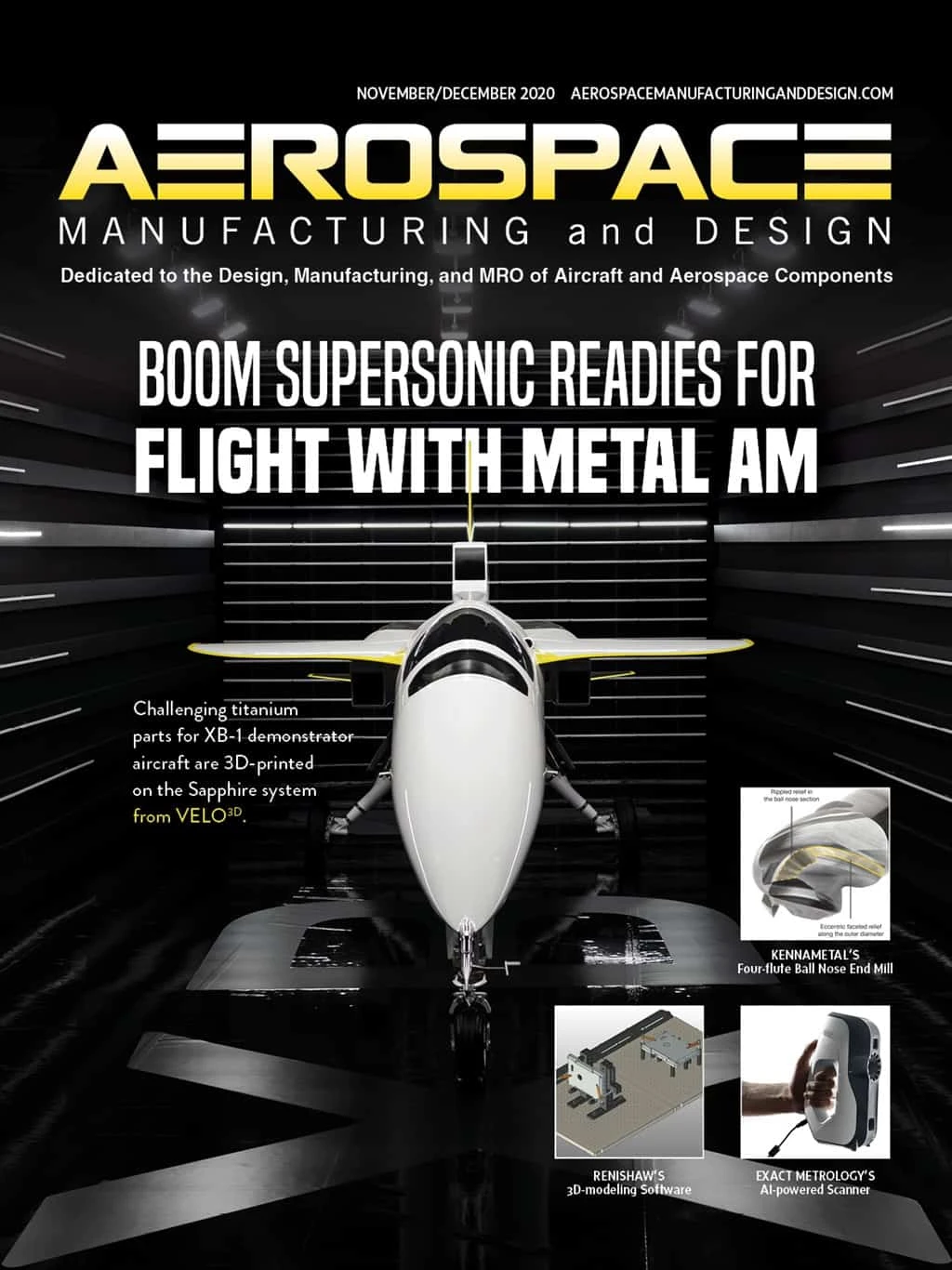
Explore the November December 2020 Issue
Check out more from this issue and find your next story to read.
Latest from Aerospace Manufacturing and Design
- America Makes announces QTIME project call
- Innovation meets precision for 40% faster machining
- Upcoming webinar: Pro tips from a supply chain strategist
- Heart Aerospace relocates to Los Angeles
- Fixtureworks introduces Stablelock Clamps
- Piasecki acquires Kaman's KARGO UAV program
- PI Americas’ long-travel XY piezo nanopositioners-scanners
- AAMI project call submission deadline extended to May 12