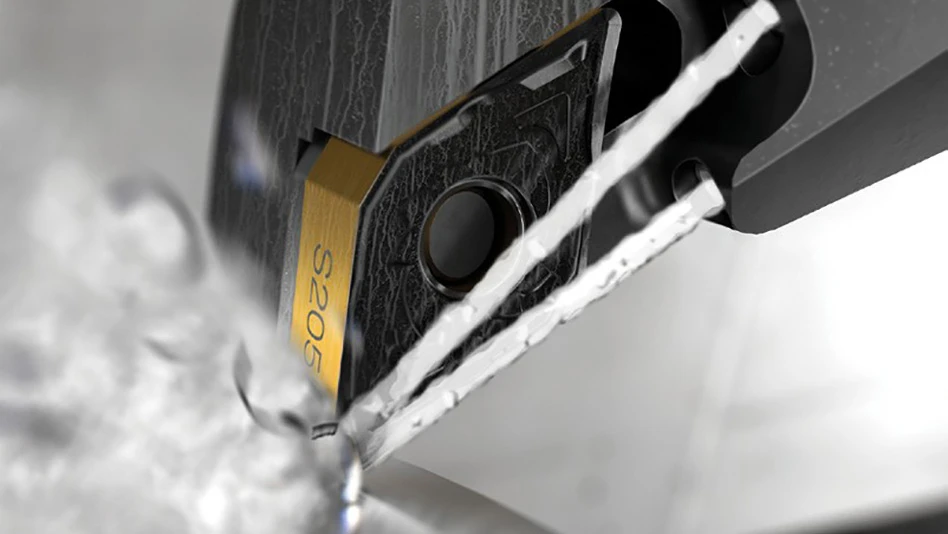

Productivity is one of the main goals for aerospace manufacturers and having the right cutting tools available at the right time is critical. Both have cascading effects for resources, operational efficiency, and the bottom line. Despite this, a major cause of wasted time continues to be overlooked: poor tool management.
In a typical workshop, 20% of operators’ time can be spent looking for tools, while 15% of jobs are rescheduled or delayed because the right tools couldn’t be found. These findings, based on Sandvik Coromant’s research of its own customers, show the extent to which poor tool management contributes to wasting time for manufacturers.
By using tool management software to control inventory levels, order tools, and produce consumption cost reports, time savings can be realized across the value stream, including operators, purchasing, and management. Depending on the frequency of needing to access, order, or report consumption of tooling used, savings of around 30 minutes per person, per shift on the floor can be realized, plus two hours or more daily for purchasing.
In addition to wasted time, poor tool management leads to accumulated high-value inventory levels, with large volumes of tool stock becoming obsolete, or stock-outs where inventory is depleted when a certain tool is needed most. Other effects include difficulties in measuring tool performance, and higher costs for stock management and processing orders.
A sector so concerned with time shouldn’t be wasting it looking for tools and spare parts. So, where are manufacturers going wrong with tool management? Many aerospace manufacturing operations today use a digital platform to document and manage tool inventory and ordering. These methods can range from a simple spreadsheet to a full-fledged digital tool management software system. The idea of digital tool management isn’t new, but just how data-driven and efficient these tools are is questionable.
Benefits of digital tool management

In its Digital factories 2020: Shaping the future of manufacturing report, PwC observed “the full effect of digitalization is only realized when companies are connected in real time to their key suppliers and critical customers.”
As with supply chain management, better data capture can also be applied to managing tool inventories for aerospace production. However, manufacturers face more challenges because tool management has many different facets. One common challenge is ensuring production is never at a standstill by monitoring inventory levels and knowing when new tools must be ordered.
One example cited in PwC’s report is Fujitsu’s plant in Augsburg, Germany, where automated shelf-life monitoring optimizes inventory levels and prevents stock-outs. In this case, digitalized inventory management does more than save time – it supports faster production times overall. Better tool management shouldn’t be exclusive to large multinationals such as Fujitsu, though. With easy-to-use software, small- or mid-sized manufacturers can also automate multifaceted tool management processes.
Considerations when choosing

Using digital tool management software replaces spur-of-the-moment decision-making with data-driven decision-making that aligns with actual use of inventory. When choosing digital tool management software, consider key features such as stock optimization that can aid ordering decision-making.
Software with stock optimization capabilities uses data gathered throughout the course of a few months to learn a company’s tool ordering habits. The software calculates the delivery time for the item, the consumption of the item, and the maximum and minimum for the stock inventory to suggest an optimized stock value. Stock optimization allows decision-making to be data-driven while making a manufacturer’s inventory management more efficient by analyzing ordering habits for streamlined ordering.
Tool-matching capabilities are another important consideration when choosing inventory management software. Software will include other matching items needed for a given tool used in the job and check if those items are in inventory or if alternate items are available. If a shop needs a new cutting head, a good tool management system will see what other grades or inserts match and whether those parts are in inventory so purchasing doesn’t need to order a new item when a suitable item is available. If your tool management software and cutting tool suppliers are following the ISO 13399 standard, this is a seamless process.
Ease-of-use

Good tool management platforms are intuitive and easy to use, aiding efficiency on the shop floor. Shops can use digital tool management platforms even without vending-style hardware cabinets. With proper digital tool management software, picking from and returning a tool to stock is quick, controlling inventory and keeping production going.
Data management can also be easier and more efficient. Tracking features in the software easily generate reports on the frequency of tool usage, allowing users to identify low-use or obsolete items or to track tool performance and longevity – comparing between different vendors or across a shift. Digital tool management software also allows assigning individual tools to specific jobs, making cost tracking more detailed.
When choosing a digital tool management software solution, it can also be beneficial to work with a supplier that goes beyond just inventory management. For example, Sandvik Coromant offers a robust digital CoroPlus Tool Guide and CoroPlus Tool Library to accompany its CoroPlus Tool Supply management software and hardware platform that serves as a resource to help manufacturers select the right tool for the job in the first place.
While many aerospace shops may have some type of tool tracking or inventory management system, real benefits will only be realized by using a smart data-driven system with real shop-oriented functionality for organizing, streamlining, and reporting the inventory and tool purchasing process. The resulting transparency in stock levels and usage allows manufacturers to reduce stock and order processing costs, and increase productivity.
About the author: Clovis Mansour is the global vending tool logistics specialist for Sandvik Coromant.
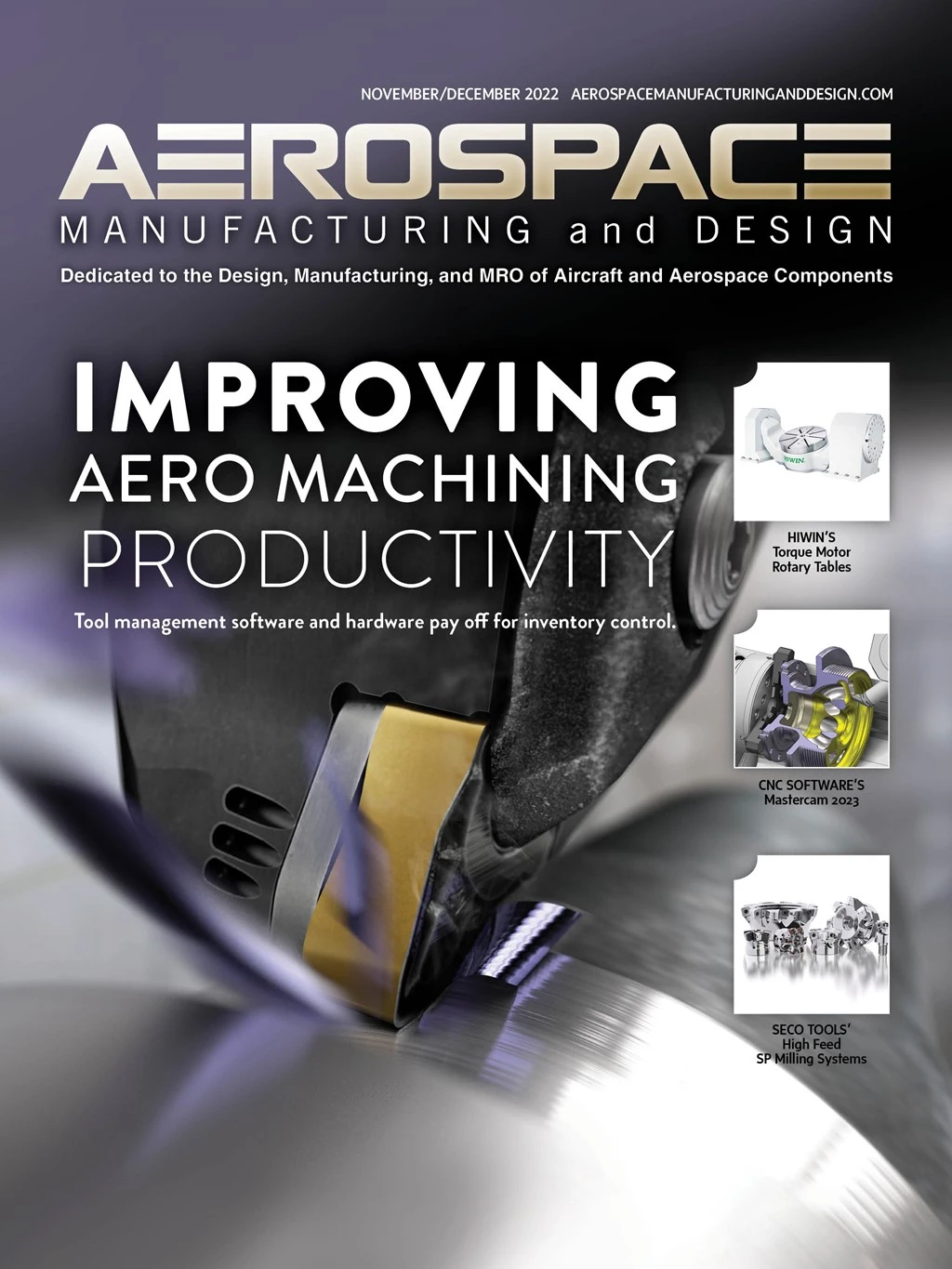
Explore the November December 2022 Issue
Check out more from this issue and find your next story to read.
Latest from Aerospace Manufacturing and Design
- Maximize your First Article Inspection efficiency and accuracy
- Archer unveils Midnight Launch Edition
- AMETEK PDS' rapid-response tactical booster amplifiers
- BAE Systems expands Endicott operations to support aircraft electrification
- Frontgrade's Class L GaN DC-DC converter, EMI filter
- #39 - Lunch & Learn Podcast with EMUGE-FRANKEN USA and Okuma America
- Boeing selects Collins Aerospace ejection seats for F-15EX
- Exxelia's mica capacitors