
Aluminum, zinc, cobalt, copper, titanium, zirconium, molybdenum, magnesium, and stainless steel are high-purity metals and alloys that are the backbone of aerospace.
The alloys should be highly consistent with extremely low levels of impurities and contaminants due to the critical nature of components made from these materials. This is driving non-destructive inspection using scanning acoustic microscopy (SAM) to identify small inclusions and defects down to 50µm.
SAM is accepted in the semiconductor industry as a failure analysis and reliability detection metrology technology but now with instrumentation, SAM is applied to high-purity metals and alloys.
The challenge is performing 100% inspection at sufficient throughput speeds to remove materials with defects not meeting strict quality requirements. Increasing scanning speed meant sacrificing scanning image resolution, but SAM advancements improved throughput speeds and defect detectability.
“While a conventional 5MHz sensor could take up to 45 minutes to inspect an 8"-to-10" square or disc alloy, an advanced phased array with 64-to-128 sensors and innovative software to render the images reduces inspection time to 5 minutes with more granular detection of small impurities or defects,” says Hari Polu, president of OKOS, a Virginia-based manufacturer of SAM and industrial ultrasonic non-destructive (NDT) systems.

By dramatically increasing inspection speed, specialty metals are no longer limited to selective sample testing during in-process quality control. SAM was used for inspection, but the testing involved handheld units or multi-point inspection. It’s now more feasible to conduct 100% inspection of the entire surface/interface.
Advances help detect gross defects and smaller defects to drive highly consistent, high yield products.
“Advanced, phased array SAM systems make it possible for specialty metals divisions to move to a higher level of failure analysis because of the level of detection and precision involved,” Polu says. “In the past, detecting a 500µm defect was the goal; now it’s a 50µm defect. And with high-purity metals, they want to inspect every item, not just a few samples.”
SAM, a non-invasive, non-destructive ultrasonic testing method, is the industry standard for 100% inspection of semiconductor components to identify defects such as voids, cracks, and delamination of different layers within microelectronic devices. Failure analysis and quality testing is applied to specialty metals and alloys to detect subsurface flaws, dis-bonds, cracks, and other irregularities.

SAM directs focused sound from a transducer at a small point on a target object. The sound hitting the object is either scattered, absorbed, reflected, or transmitted. By detecting the direction of scattered pulses and the time of flight, a boundary or object can be determined as well as its distance.
Samples are scanned point by point and line by line to produce an image. Scanning modes include single layer views, tray scans, and cross-sections. Multi-layer scans include up to 50 independent layers. Depth-specific information can be extracted to create 2D and 3D images without tomographic scans and X-rays. Images are analyzed to detect and characterize flaws such as cracks, inclusions, and voids.
When high throughput is required for 100% inspection, ultra-fast single- or dual-gantry scanning systems are used with 128 sensors for phased array scanning. Multiple transducers can be used to simultaneously scan for higher throughput.
Software is critical to improving the resolution and analyzing the information to produce detailed scans. Multi-axis scan options enable A-, B-, and C-scans, contour following, off-line analysis, and virtual rescanning for composites, metals, and alloys, resulting in highly accurate internal and external inspection for defects and thickness measurement through inspection software. ODIS Acoustic Microscopy software supports transducer frequencies from 2.25MHz to 230MHz.
Polu says, “With more sensors and advanced software to interpret the information at very high resolutions, specialty metals manufacturers can inspect 100% of materials at one to two orders of magnitude better to discover flaws that were previously undetected.”
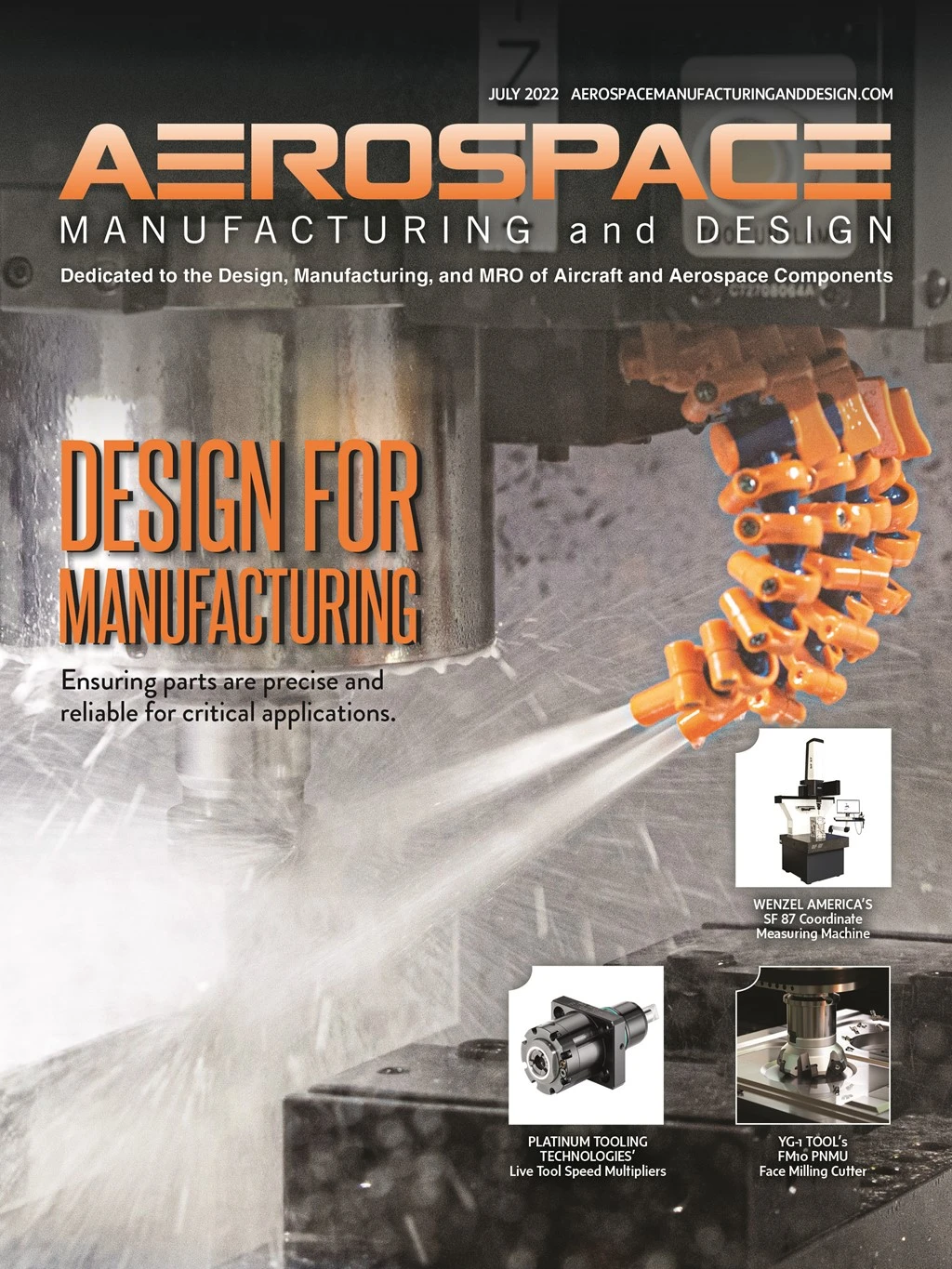
Explore the July 2022 Issue
Check out more from this issue and find your next story to read.
Latest from Aerospace Manufacturing and Design
- Revitalizing the Defense Maritime Industrial Base with Blue Forge Alliance
- Safran Defense & Space opens US defense HQ
- Two miniature absolute encoders join US Digital’s lineup
- Lockheed Martin completes Orion for Artemis II
- Cylinder CMMs for complex symmetrical workpieces
- University of Oklahoma research fuels UAS development
- Motorized vision measuring system
- Everyone's talking tariffs