
Aerospace Manufacturing & Design (AM&D): How is hydraulic press technology keeping pace with the latest aerospace challenges, for example, large/complex presses including compression molding types for lightweight aircraft components?
Rob Bisbee (RB): Our systems come standard with expandable platforms, ready for auxiliary equipment, guarding, and material handling with communication systems. Monitoring systems track each cycle’s progress while process data – including force, parallelism, and temperature – are stored for record-keeping and direct inspection opportunities.
Greenerd also offers support for the more complex functions with live troubleshooting, software backups, and program edits. Greenerd also offers additional tools and options, including heated platens with dynamic temperature control maintaining 5°F across the working area.

The tools available on modern press equipment help manufacturers achieve significant benefits in their processes
.AM&D: How do you work with customers to build large, complex presses?
RB: When partnering with our customers, Greenerd engineers take deep dives into their process for a thorough understanding of what will make a project successful. By choosing the right technologies to meet those needs, we can create press solutions that more perfectly address their application. Combined with expertise in automation and integration, Greenerd can deliver turnkey systems that integrate seamlessly into production lines.
AM&D: When a customer comes with a requirement, how do you match the customer with the right press solution?
RB: By taking the time to learn and understand the goals for projects, Greenerd can bring broad application experience to the partnership, which is essential in enabling the customer to achieve the best possible outcome for their investment. During the initial design process we tailor custom solutions to the application by combining our press engineering, automation, and application experience with the customer’s engineering and shop floor knowledge specific to their production environment. While standard products can often meet requirements, an open review of the customer’s specific production dynamics typically reveals opportunities to deliver more benefits and value than from a standard product. These press systems will be in operation for decades, so it’s worth taking the extra time to create the optimal solution.
AM&D: How does automation factor into press solutions?
RB: Automated technologies that can improve quality, reduce overhead, and solve difficult challenges have always been in demand by the largest manufacturers. In recent years, many small and medium manufacturers have been taking advantage of these technologies as well, often by leveraging original equipment manufacturers (OEMs) for solutions tailored to their production realities. Technical expertise from Greenerd can help integrate a variety of technologies into a solution, combining many elements of a customer’s pre-processing, post-processing, and material handling requirements into one solution by one equipment provider.

AM&D: What recommendations are there for companies automating hydraulic presses?
RB: Press functionality is at the core of automation projects. Partnering with a press manufacturer who is also an authorized system integrator is advantageous. Leveraging this automation expertise in combination with the customer’s view of potential process improvements can achieve higher levels of added value in the production environment and for the manufacturer.
One Greenerd customer recently said, “The team and I had a fairly evolved view of how we wanted the overall process to flow; what we lacked was the press hydraulics knowledge and controls expertise to see it through.” Another customer said, “During the design/build the decision was validated as Greenerd was able to apply past experiences which ultimately improved the overall design of the cell.”
Another option is to work with a generic automation house or systems integrator. While this can be beneficial for non-press projects, these sources may lack the specific product knowledge that comes with years of working with presses, tooling, dies, and product handling. Not all third-party automation companies have presses/production knowledge, but most major press manufacturers have worked with and can deliver automation.
AM&D: Has the stressed supply chain and lack of skilled labor impacted the presses/stamping industry?
RB:Volatile supply chains have created challenges, and production capacity is constrained by available labor, so moving to greater in-house capabilities and automation allows manufacturers to meet these new market realities.
Staffing to meet surges in demand remains a significant issue for manufacturers, especially in rural areas. Implementing new technologies can reduce the number of manual tasks and improve documentation and process controls. This also simplifies the training needed to scale production.
AM&D:
How is Greenerd positioning its equipment solutions and its capabilities to help aerospace manufacturers solve production problems?
RB: We continue to invest in new technologies and broaden our expertise to provide the best solutions. Material tracking, machine vision, final inspection reporting, and robotic material handling are all being paired with presses right-sized for the application. Combining available technologies in a meaningful way improves quality and increases productivity. With a diverse portfolio across many industries, the right technologies can be found to solve the most difficult problems.
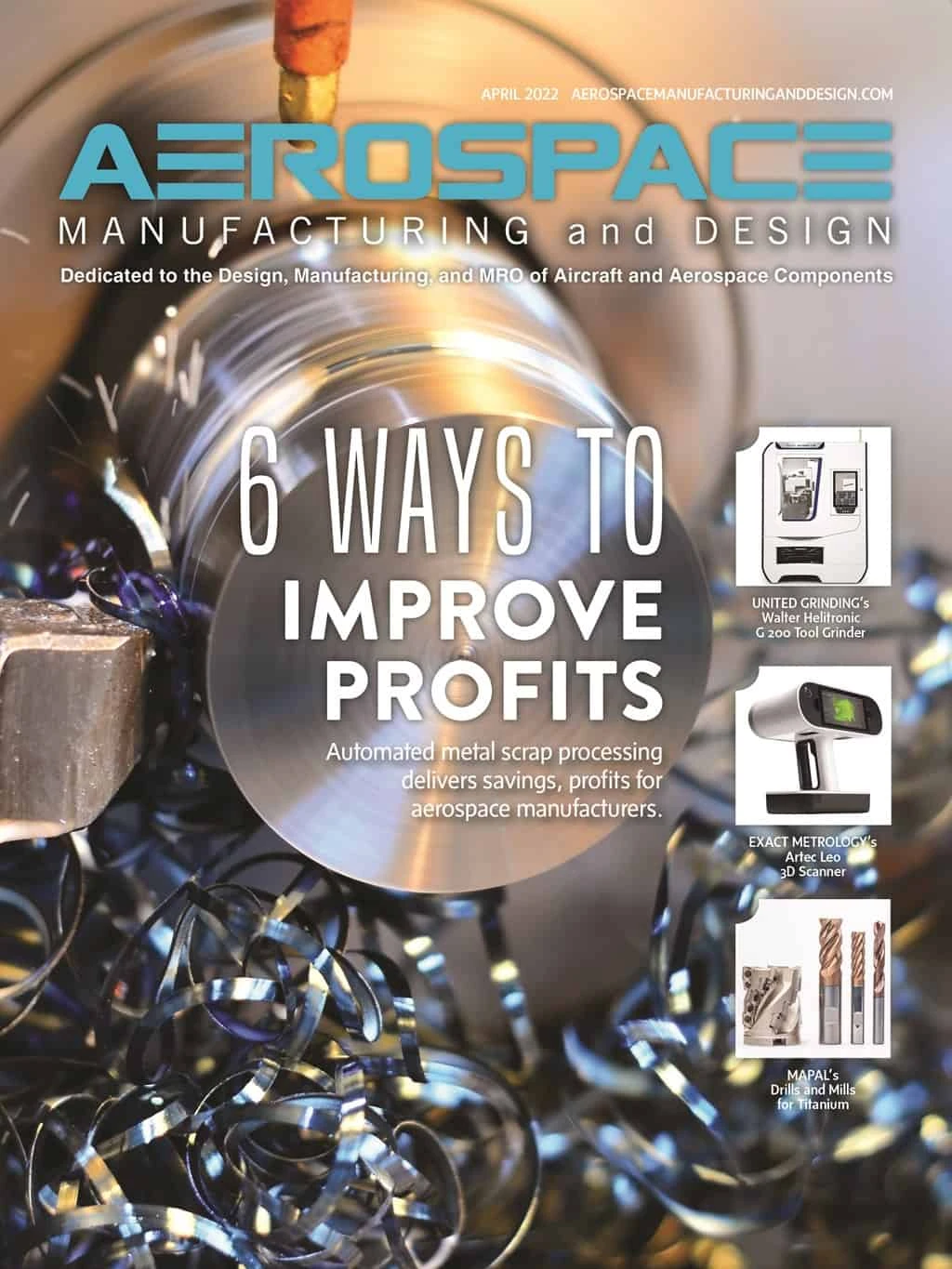
Explore the April 2022 Issue
Check out more from this issue and find your next story to read.
Latest from Aerospace Manufacturing and Design
- Electra reaches 2,200 pre-orders for its Ultra Short aircraft
- Heule's DL2 tooling for deburring of small bores
- Ralliant to establish global headquarters in North Carolina
- Philatron MIL-DTL-3432 military cables
- Beyond Aero refines its hydrogen-electric light jet
- Americase's advanced protective solutions
- Social media - what are your thoughts
- GE Aerospace secures Air Force engine contract