
The INTEGREX e-1250V/8 AG Hybrid multi-tasking machine combines full 5-axis machining, heavy-duty turning operations, and pallet-changing capabilities for productive processing of large, highly complex parts from titanium, aluminum, and steel. The machine also includes the Hybrid Auto Gear (AG) package with a full range of Smooth Technology solutions for Done-in-One gear production.
The machine’s ability to perform milling, turning, boring, and drilling operations in single setups reduces inaccuracies that can occur when moving heavy parts across multiple workstations. Additionally, the machine’s direct-drive table eliminates backlash for smoother, high-precision rotation in heavy-duty cutting operations.
High-speed and high-torque milling spindle specifications are available to meet the various demands of individual application requirements.
The machine’s two-pallet changer provides unattended operations and off-cycle part setup. This simple, efficient form of automation allows you to load, unload, and inspect parts on one pallet while the machine works on the other undisturbed.
Mazak Corp.
IMTS 2024 booth #338300
Automated laser welding system

The modular design of Emerson’s Branson GLX-1 laser welder enables use in ISO-8 cleanroom environments. The servo-based actuation controls of the GLX-1 welder allow for greater freedom to design and join components with three-dimensional contours.
The GLX-1 welder relies on Emerson’s Simultaneous Through-Transmission Infrared (STTlr) laser-welding technology, which provides higher production efficiency, weld strength, and aesthetics. TheGLX-1 delivers weld power using Branson’s high-power laser banks, which offer configurable power levels up to a maximum of 250W per bank.
Operational and security features are accessed through the welder’s 12" touchscreen HMI. The welder offers 99 levels of customizable password protection and connects easily with plant networks to meet industrial Internet of Things (IIoT) or communication requirements, offering Data Interface Gateway (DIG) and fieldbus interface gateway compatibility, a USB port, and an OPC-UA interface.
Skiving tools

Gear manufacturers can have a single source for skiving tool solutions, including wheels for internal and external gears as bell-type or shank tool variants in the module sizes m 0.4 to m 5.0. Skiving tools can be used in various gear applications including the production of ring gears, shafts with internal and external splines, and splined shaft profiles. The skiving tools have no restrictions on the material being machined and are suitable for both soft and hard machining processes.
The company’s clamping division specializes in providing customized solutions for applications ranging from low-volume job shops to high-volume automotive production environments. The company designs and develops clamping solutions by working closely with its customers to learn about the unique application challenges and production environments.
End mills

The M934 and M935 cutting tools are extensions of the M9 POW•R•FEED line. Both achieve high metal removal rates well-suited for machinists looking to improve production processes.
Engineered with multi-parabolic grinds (MPG), M934 4-flute end mills cut in steels, titanium, and nonferrous materials. In 3- to 5-axis machines, users can swing the tool around the part without clogging, increase feed rates in moves in Z, and reduce cycle time.
M934s are for parts requiring helical entry, ramping or slotting, and an option to peripheral mill at super aggressive feeds. The flute and end face geometries minimize clogging.
M935 5-flute end mills are designed with unique flute and core geometries for very aggressive traditional tool paths, stepovers, and depths. Each flute has a unique helix angle, providing excellent balance and chip throw. MPG (multi-parabolic grinding) makes M935 tools’ end face and flute cavity suitable for extremely aggressive ramping, helical entry, and cutting parameters.
They’re engineered to slash cycle times, boost metal removal rates, finish jobs faster, and provide great tool life. M934 and M935 mills feature super-fine cutting edges and edge prep for long life. Both options have a wiper flat end for smooth floor finishes. The M935 is also available with Chip Management System (CMS).
IMCOWANT MORE?
Enter your email to receive our newsletters.
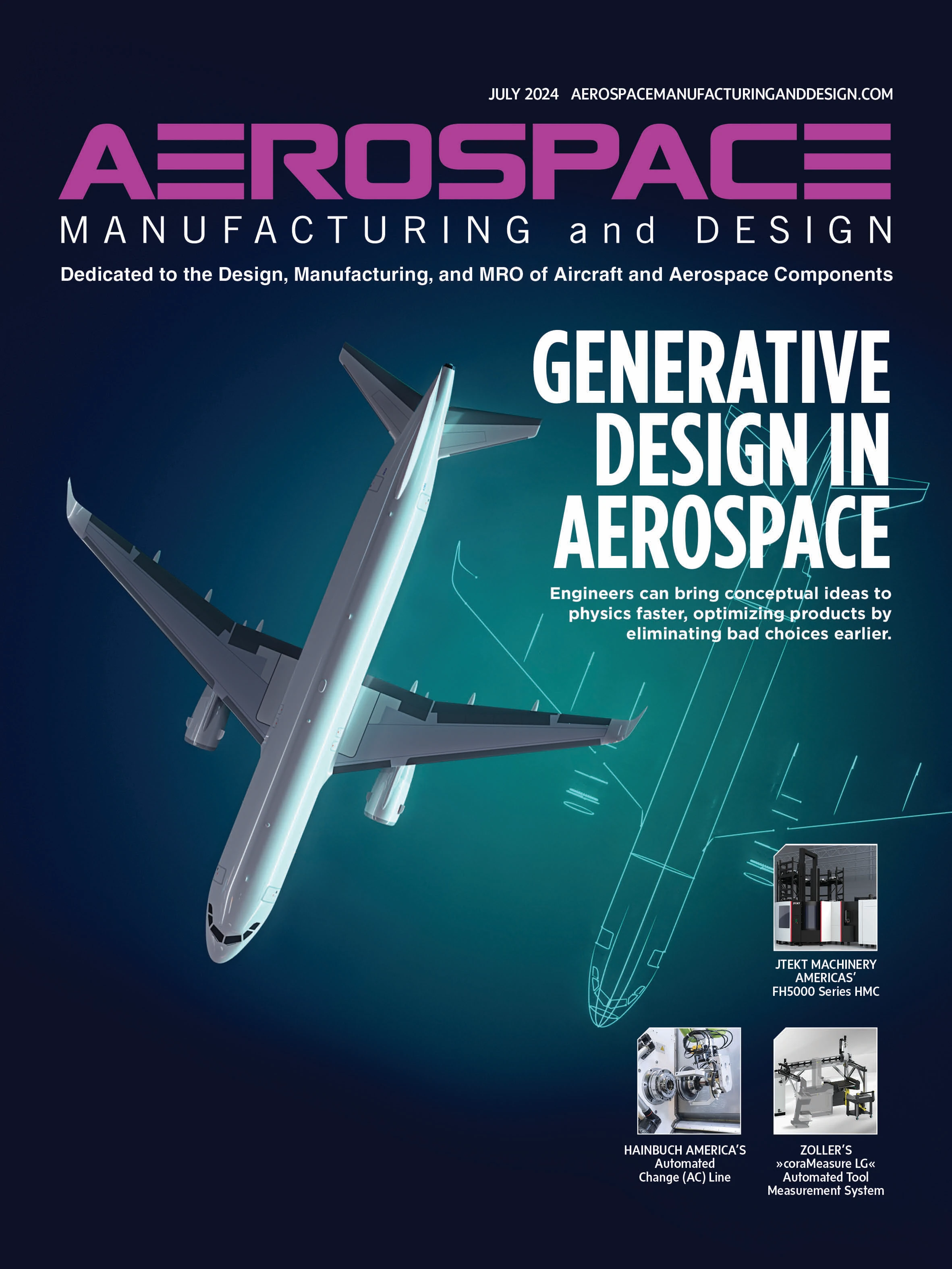
Explore the July 2024 Issue
Check out more from this issue and find your next story to read.
Latest from Aerospace Manufacturing and Design
- Cyient Group, Deutsche Aircraft finalize multi-year contract
- High surface quality at high speed
- #57 - Manufacturing Matters - Agile & Robust Supply Chain Management with Lisa Anderson
- Take control of your manufacturing business despite supply chain turmoil
- Strengthening the defense maritime industrial base for national security, economic resilience
- Register now to learn solutions for high-temperature aerospace machining challenges
- Expertise on machining, joining offered in April’s Manufacturing Lunch + Learn
- NASA offers free high school engineering program this summer