
MAX phases materials – layered, hexagonal carbides and nitrides – show promise for turbines in aircraft and power plants, space applications, or medical implants, and a new method makes it possible to produce them on an industrial scale. Developed by scientists from Jülich, the process uses a crust of salt to protect raw material from oxidation at 1,000°C production temperatures, then water washes the salt away. The method, recently published in the journal Nature Materials, can be applied to other high-performance materials.
MAX phases offer the heat-resistance and light weight of ceramics yet are less brittle and can be plastically deformed like metals. They are the material basis of MXenes, a largely unexplored class of compounds similar to graphene and have extraordinary electronic properties.
“There was no suitable method for producing MAX phases in powder form, which would be advantageous for further industrial processing. That’s why MAX phases have not played any practical role in industrial application,” explains Junior Professor Dr. Jesus Gonzalez-Julian, young investigators group leader at Jülich.
The salt strategy
Produced at extremely high temperatures, MAX phases would normally react with atmospheric oxygen and oxidize, which is why they are usually produced in a vacuum or in an argon atmosphere. With the Jülich method, researchers encapsulate the raw material with a potassium bromide salt that melts during production.
“A bath of molten salt protects the material and prevents it from coming in contact with atmospheric oxygen,” explains Apurv Dash, lead author and doctoral researcher at Jülich. Meanwhile, the salt separates components so they no longer bond to form a compact solid, allowing production of fine-grained powders. This avoids a lengthy, energy-intensive milling process. Additionally, the salt bath reduces the synthesis temperature necessary to form the desired compound, cutting energy and production costs further.
Just salt and water
Molten salts have been used for non-oxide ceramic powder production for some time. However, they require a protective argon atmosphere instead of atmospheric air.
“Potassium bromide, the salt we use, is special because when pressurized, it becomes completely impermeable at room temperature. We have now demonstrated that it is sufficient to encapsulate the raw materials tightly enough in a salt pellet to prevent contact with oxygen – even before the melting point of the salt is reached at 735°C,” Dash explains.
As with many scientific discoveries, luck played its part in inventing the method: vacuum furnaces are scarce because they are expensive and take a lot of effort to clean. To produce his powder, the Jülich doctoral researcher tested a normal air furnace – successfully.
The new method is not limited to a certain material. Researchers have already produced a multitude of MAX phases and other high-performance materials, such as titanium alloys for bioimplants and aircraft engineering. Scientists are now planning to investigate industrial methods for processing the powders further.
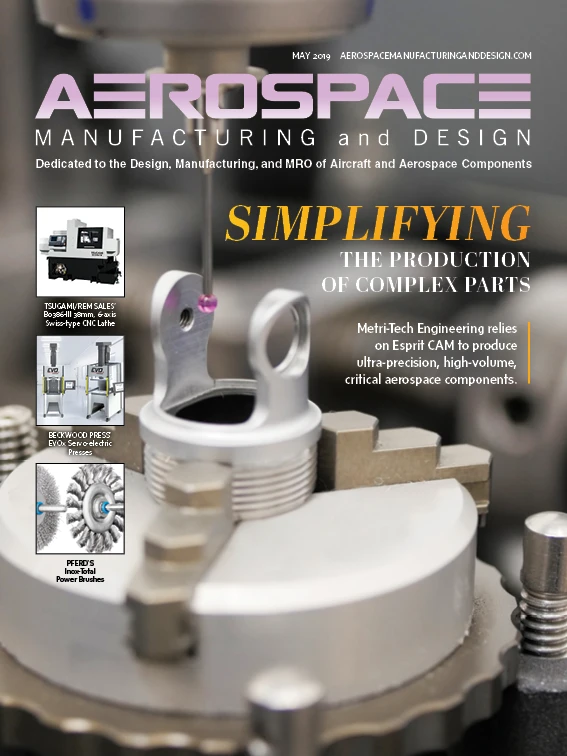
Explore the May 2019 Issue
Check out more from this issue and find your next story to read.
Latest from Aerospace Manufacturing and Design
- Essential strategies to protect your data
- NASA selects instruments for Artemis lunar terrain vehicle
- Twin-cutter boring head
- Bell awarded funding for X-plane build phase of SPRINT program
- Shaft coupling clamps
- #46 Lunch + Learn Podcast with SMW Autoblok
- Gleason Corp. acquires the Intra Group of Companies
- Thread milling cutter reduces cutting pressure, vibration