
Industrial production of titanium alloys has been plagued by challenges associated with quality and waste management. Engineering scientists from the Hong Kong Polytechnic University (PolyU), in collaboration with RMIT University and the University of Sydney, have successfully used additive manufacturing (AM) to solve these long-standing issues in titanium alloy production.
The research team’s discovery of the innovative use of AM for producing titanium alloys and potentially other metal materials offers advantages such as reduced costs, improved performance, and sustainable waste management.
The research team 3D-printed a new strong, ductile, and sustainable titanium alloy (α-β Ti-O-Fe alloy) by incorporating inexpensive and abundant oxygen and iron, the two most powerful stabilizing elements and strengtheners for α–β phase titanium alloys.
Previously, the embrittling effect of oxygen and the micro segregation of iron have hindered their combination for developing strong and ductile α-β titanium-oxygen-iron alloys.
The simplicity for net-shape or near-net-shape manufacturing by AM makes these alloys attractive for a range of applications. AM allows adjusting the microstructure of metal alloys, increasing strength, flexibility, and resistance to corrosion and water.
Compared with the Ti-6AI-4V benchmark material, the new titanium alloy demonstrates better mechanical performance, with comparable ductility and considerably higher strength.
Although traditional manufacturing methods, such as casting, can also produce the alloy, the poor properties of the resulting material may render it unsuitable for practical engineering. AM effectively overcomes the limitations of traditional methods to improve alloy properties. Furthermore, AM makes possible lightweight but strong metal parts with intricate internal patterns, permitting holistic and sustainable material design strategies.
The energy-intensive Kroll process, typically used to produce titanium alloys, generates off-grade sponge titanium, resulting in substantial waste and increased production costs. AM enables recycling off-grade sponge titanium, converting the waste into powder for use as raw material.
Dr. Zibin Chen, assistant professor of the Department of Industrial and Systems Engineering at PolyU and a leading author of the research, says, “Our work can facilitate the recycling of more than 10% of the waste generated by the metal alloy production industry. This can significantly lower material and energy costs for industries, contributing to environmental sustainability and carbon footprint reduction.”
Prof. Keith K.C. Chan, chair professor of manufacturing engineering at the Department of Industrial and Systems Engineering at PolyU and a co-author of the study, notes, “This work can serve as a model for other metal alloys that use 3D printing to enhance their properties and expand their applicability.”
The Hong Kong Polytechnic University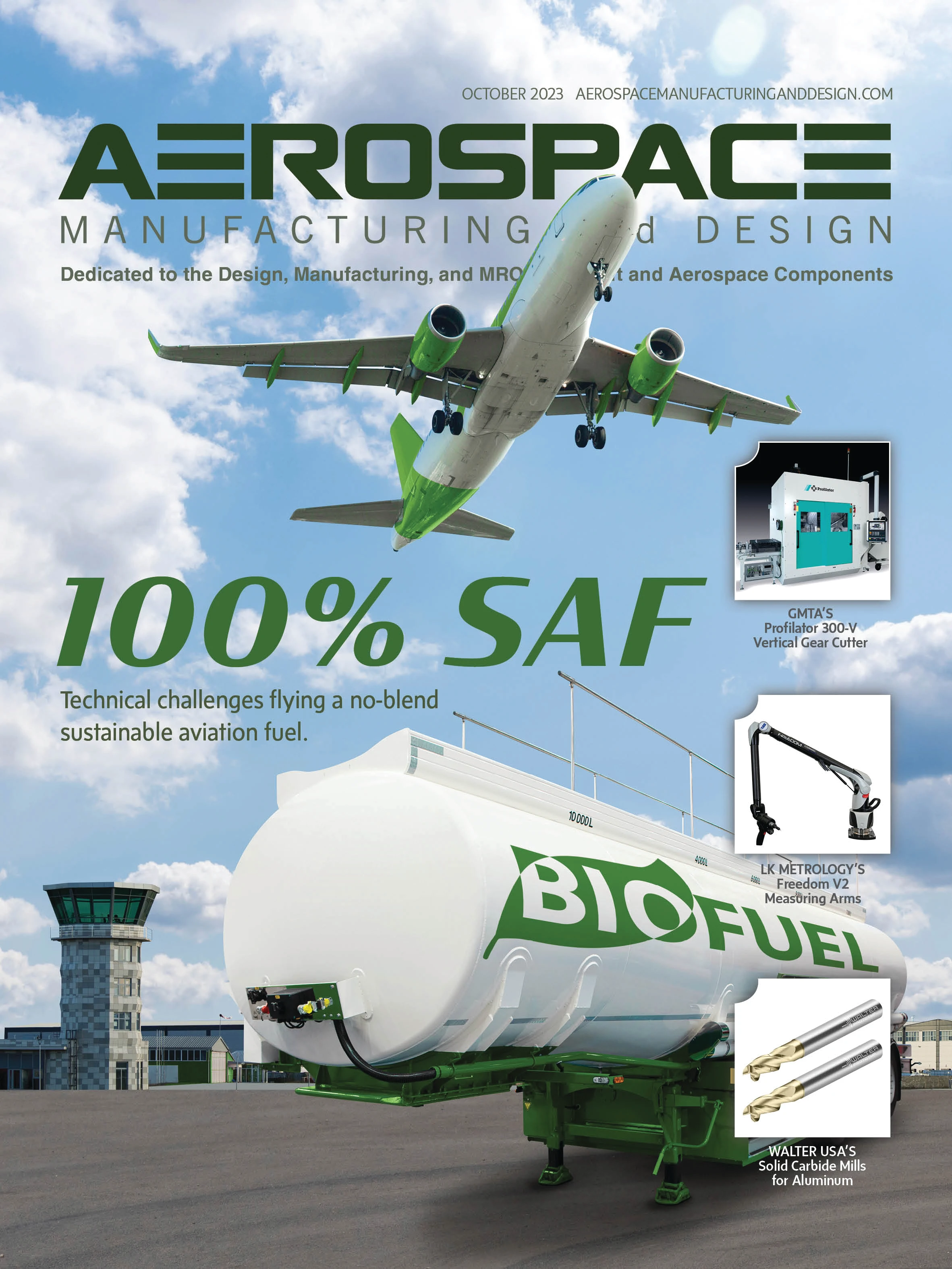
Explore the October 2023 Issue
Check out more from this issue and find your next story to read.
Latest from Aerospace Manufacturing and Design
- Cyient Group, Deutsche Aircraft finalize multi-year contract
- High surface quality at high speed
- #57 - Manufacturing Matters - Agile & Robust Supply Chain Management with Lisa Anderson
- Take control of your manufacturing business despite supply chain turmoil
- Strengthening the defense maritime industrial base for national security, economic resilience
- Register now to learn solutions for high-temperature aerospace machining challenges
- Expertise on machining, joining offered in April’s Manufacturing Lunch + Learn
- NASA offers free high school engineering program this summer