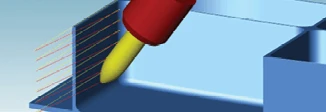
Open Mind Technologies USA Inc.

Advances in materials and engine efficiency have created clear benefits for replacing older aircraft. Demand is so significant that machine tool makers are challenged to supply equipment quickly enough to aircraft manufacturers and their suppliers. Increasing the number of spindles can be difficult and expensive, so some producers are reacting by increasing productivity of tooling, workholding, and CAM software solutions. Enhancements to support technologies can increase productivity of existing equipment, reducing the need for new machines.
Aerospace CAM
Many CAM systems focus on processes such as 5-axis milling, mill-turn, wire EDM, or mold-and-die applications. So, ideal CAM software for aerospace must excel at high material removal of aluminum from structural components and work well with high-precision temperature-resistant titanium or nickel-based superalloy compressors and turbines.


Structural machining
High-performance roughing brings aluminum blocks or plates to near-net shape, where 90% or more of the block weight may be removed. This is important in typical 3-axis structural components and crucial in 5-axis components. Many CAM programs have a high-performance roughing module using trochoidal techniques. Open Mind’s hyperMILL MAXX Machining roughing module has been extended to apply to 5-axis roughing. For shaped structural components (wing segments or doors), 5-axis roughing benefits subsequent machining processes.
Finishing techniques

Standard structural part surfaces are machined with swarf milling, with the side of the cutter aligned to the side of the part, enabling good performance but limited to 50mm high wall surfaces. For larger wall surfaces, swarf milling may cause the cutter or wall surface to vibrate. Multiple steps with overlap and inconsistent deflection patterns are also possible. The next best option is point milling in many passes by using the tip of a ball-nose end mill with a small step-over. Unfortunately, point milling increases cutting time dramatically.
Open Mind’s hyperMILL MAXX Machining finishing uses a conical barrel cutter (also known as circle segment or arc segment end mill) for a barrel contact radius of 1,000mm or more, producing a wider stepdown 10x to 15x that of a ball-nose end mill. This can reduce cutting time 90% or more. The conical barrel cutter has the large barrel radius ground on a tapered feature, compared to a traditional barrel cutter where the large radius blends to be tangent to the cutter shank.
The taper allows the cutter axis to be pulled away from the surface being cut. The result is a shorter, stiffer cutter without interference from the cutter holder. Though the tangent barrel cutter provides some benefit, the conical barrel cutter enables a larger barrel radius to allow shorter cutters without interference from the cutter holder.

Conical barrel cutters exhibit long life and consistent machining performance. In addition, the ball end on the tip of the conical barrel cutter can be used to clean fillets and blend surfaces using the same cutter.
Engine components
Single blades for a turbine engine can be machined from rectangular block, cylindrical stock, or near-net forgings. Roughing is a critical task to control costs and to set up for finishing operations. Due to various starting stock shapes and irregular finishing shapes, stock tracking is essential during roughing to avoid wasteful air cuts. As blades can be twisted, multiple cutting orientations should be used during roughing to leave minimal stock for finishing.
Single-blade finishing is typically performed with ball-nose end mills, especially on twisted surfaces and near attachment platforms. Open areas of the blade surface are often cut with a tilted bull-nose cutter. This cutting style gives a large effective radius of curvature and can produce a fine surface finish with fewer passes compared to a ball-nose end mill. Recent developments also include the applications of high-angle conical barrel cutters to single blade components.
Finishing multi-blade components – a turbine bladed disk (blisk) – brings additional challenges due to tight blade spacing and requirements for high aspect-ratio cutters. CAM collision detection and avoidance techniques can find a solution in the close spacing between blades.
Small cutter radii imposed by blade spacing, fillet geometry, and fine surface finish specifications may require hundreds of passes around the blade using a ball-nose end mill. Applying long path lengths against hard metals is time consuming and leads to cutter wear and concerns for manufacturing consistency. Some engine manufacturers change a cutter for each subsequent blade surface to assure consistency of wear and reduce imbalance of the machined part.

Machining blisks with close blade spacing requires CAM collision detection and avoidance.
Twisted multi-blade surfaces typically don’t allow swarf milling. Conical barrel cutter solutions are also being applied to achieve cycle time and quality improvements. The larger stepover reduces overall path length and tool wear compared to ball-nose end mills.
Single-blade and multi-blade components can be classified with feature-based and family-of-parts (macro) programming. Repeated geometry selections of curves and surfaces are more complex than typical holes and pockets but can be represented by feature definitions. Using best practices for materials and tooling, including feed rate and spindle speed, holders, stepdown, and stepover, can be useful when programming for multiple parts. A comprehensive family-of-parts strategy reduces the programming effort across many parts while achieving high productivity.
CAM has a large influence on machine tool performance, so users can benefit by selecting the proper software for the application. The most advantageous CAM software is continually evolving with each new version release to offer enhancements and innovations that keep up with aerospace manufacturing requirements.
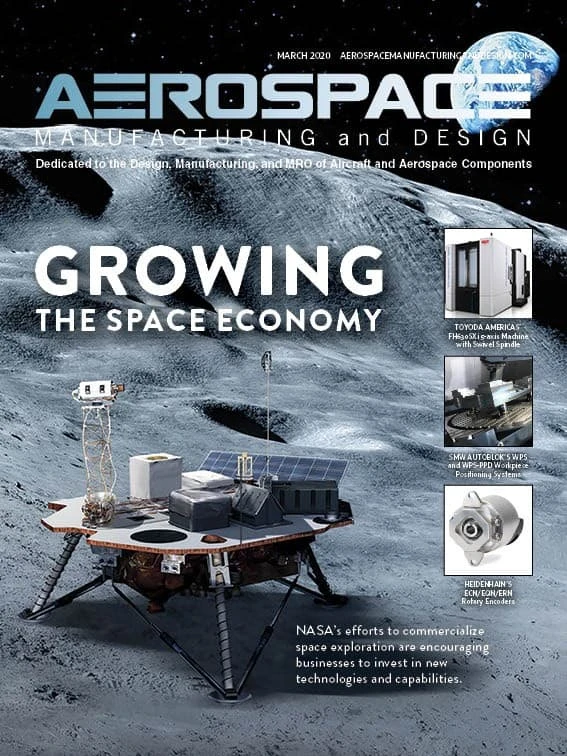
Explore the March 2020 Issue
Check out more from this issue and find your next story to read.
Latest from Aerospace Manufacturing and Design
- Safran Defense & Space opens US defense HQ
- Two miniature absolute encoders join US Digital’s lineup
- Lockheed Martin completes Orion for Artemis II
- Cylinder CMMs for complex symmetrical workpieces
- University of Oklahoma research fuels UAS development
- Motorized vision measuring system
- Everyone's talking tariffs
- Boom Supersonic to launch Symphony engine testing in Colorado