
Professional Aircraft Accessories (PAA) in Titusville, Florida, specializes in the repair and overhaul of landing gear, accessories, instrumentation, pressurization, radio, radar avionics, and airframe components. Already well entrenched in fixed-wing aircraft, expanding into the helicopter market was a natural extension, and the request for quote (RFQ) for overhaul and recertification of OH-58 Kiowa helicopter transmissions provided a perfect opportunity.
There was only one caveat: a very condensed timeframe. PAA officials found that oil shear braking technology helped them meet the technical requirements of the project and the fast response needed for initial certification testing.
Short-fused project takes off

With the RFQ approved, PAA officials had four months to design and build a dynamometer test stand and overhaul three transmissions to get their project verification audit from the Army. Given the short timeframe, the project engineering team opted to use non-regenerative technology. Jerry Leach, director of production engineering and planning, led the team designing the system.
“Designing a system to do what we wanted with regenerative technology would have been more efficient, but it would have taken 4x longer and cost at least twice as much,” Leach says. “We contracted out key components of a system we could build in-house and decided to dump power into the system and then load it via braking. This is very effective, but it builds up a lot of heat which must be exhausted.”
Power is supplied via a GE electric motor and variable frequency drive (VFD) combination with 700hp and 3,600rpm. The specification calls for testing at 40%, 60%, 80%, 100%, and 112% of load for various timeframes. Precisely controllable load is supplied by a TB 83 oil shear brake from Fairfield, Ohio-based Force Control Industries. At 112% of load, Leach cites 8,200 lb-ft torque. The test takes about an hour, during which there is very little temperature rise.

“They definitely sized the cooling unit correctly,” Leach says.
To dissipate the heat generated by that amount of torque, the oil shear brake is equipped with a forced lubrication and cooling system. In addition, the heat exchanger circuitry also has components to safeguard against viscosity changes as the oil changes temperature. To safeguard against overloading the pump, which moves 250 gallons of oil per minute across the brake, heating elements controlled by a programmable logic controller keep the oil at a fairly consistent temperature.
Leach and the team specified components from various sources, the GE motor and VFD, a skid-mounted brake and cooling system from Force Control Industries, and a 1.7:1 gearbox to reach the 6,000rpm needed. They used LabView software from National Instruments for data acquisition and testing. Once the major components were installed, there was still plenty to do.
“The plumbing required to move that much fluid, at temperatures from 50°F to 175°F to accommodate expansion and contraction, was challenging,” Leach says.
Additionally, 1,200A electrical service had to be put into the facility before everything could be wired and tested. Getting it all in place was the first hurdle, but it wasn’t the last challenge for the project.
Just a few tweaks

While the system was designed for vertical operation, the brake was mounted horizontally to allow direct torque measurement. Force Control officials didn’t foresee a problem doing so, but an air pocket was created that caused the friction disc to burn up, since it was not fully wetted. A fast and effective solution was implemented, allowing PAA to produce overhauls for the initial validation audit.
After passing the validation audit, PAA was off and running. The test stand was performing well, but the brake needed to be rebuilt after every 10 to 15 transmissions.
Leach’s company, PAA, was footing the bill, and he thought that rebuilding the brake so frequently would be normal – until Force Control engineers devised a solution.
“Apparently their engineers were seeing similar issues with another installation and determined a need for additional surface area. We were very pleased to hear that it could be accomplished by changing out internal components,” Leach states.
Changing external components, would likely change the location of virtually all of the hoses, power connections, and positioning of the brake relative to the helicopter transmission. It might mean relocating everything.
Once the new components were installed, PPA engineers haven’t experienced any issues with the system.

“The level of support was outstanding” Leach says.
Clear skies and smooth sailing
Despite a short timeframe for development and a rocky start, the OH-58 Kiowa transmission overhaul test stand is operating smoothly and has been for the past two years. Following this successful project, PAA is also planning to test additional helicopter components, which can be accomplished with minor modifications to the existing test stand.
While the success of the project was important to both PAA and Force Control, it is vital for the brave men and women who rely on the Kiowa reconnaissance helicopter every day.
_off_Hawaii_in_2013-usnavy_fmt.png)
Rebuilding the transmissions quickly, yet proficiently, and getting these armed scout aircraft back into service is a top priority for the Army. With the cooperation between customer and vendor, as well as the oil shear braking technology employed in the custom dynamometer test stand, PAA officials can tell the Army, “Mission accomplished.”
Force Control Industries
National Instruments
Professional Aircraft Accessories (PAA)
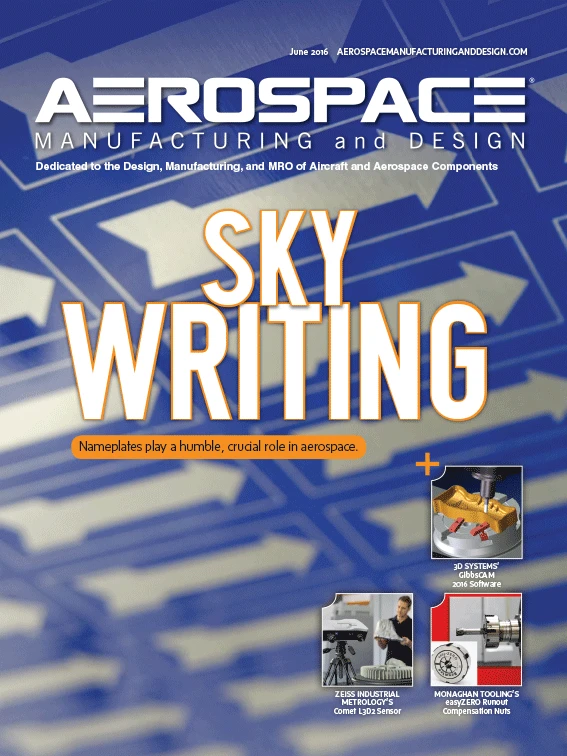
Explore the June 2016 Issue
Check out more from this issue and find your next story to read.
Latest from Aerospace Manufacturing and Design
- Trelleborg acquires Aero-Plastics
- Industrial automation products, enclosed encoders
- #61 - Manufacturing Matters: CMMC roll out: When do I need to comply?
- AIX shows aircraft interiors are a strategic priority for global airlines
- Machine Tool Builders Roundtable: Turn equipment into expertise
- No time to waste: How to machine MedTech parts more efficiently
- The 5 Best and Fastest Spindle Repair Services
- Mill smarter, not harder: How collaboration optimizes production