
Longtime relationships with its employees, customers, and suppliers, along with access to real-time manufacturing data, are helping a Connecticut aerospace job shop survive the disruptions of the COVID-19 pandemic and prepare for renewed growth in its wake.
When the pandemic appeared, PDQ immediately took measures to protect its employees, including regular body temperature checks. Slowing or stopping production weren’t options as a military aerospace parts customer named the shop an essential business.
“We are to remain open and fulfill deliveries as needed, and that’s where we are right now,” Manufacturing Manager Scott Norman says.

Machine data challenges
PDQ was undergoing a comprehensive enterprise resource planning (ERP) software implementation when the COVID-19 crisis began, making part demand and data management more volatile. For a company that already needed improvements to machining data recording, it was a challenging time.
“In the old system, operators wrote their setup and run times on paper time sheets,” Norman explains. “The production data was entered at the end of the day and wasn’t immediately verifiable. We were a slave to when and how the information was put in.”
Delayed and sometimes inconsistent manual recording of machine output resulted in shop personnel not always being sure of finished part volume and expected lead time.
As LillyWorks (Hampton, New Hampshire) installed the ERP, PDQ officials decided to integrate the software with a machine data communications (MDC) platform from Excellerant LLC (Somers, Connecticut). Excellerant’s software and hardware act as a universal decoder, allowing a shop to connect various brands of CNC machine tools and controllers, monitor and manage each machine’s data in real time, and then transmit the data to the company’s ERP system. Excellerant communicates via MTConnect, Fanuc Focas, OPC-UA, Haas MNET Q-Codes, and other machine control connecting protocols and can be used with legacy CNC machines.
Excellerant’s system counts parts as they’re created. At the end of each shift, the operator qualifies the number of good parts produced and the MDC platform automatically enters the total into the shop’s ERP system.
Norman says using the Excellerant platform has made it easier for his staff to do its job. “I don’t have to leave my office to tell operators what needs to be done. They know what they should be doing, how many parts they should be making. Previously, that wasn’t communicated clearly to them, now it is.”
PDQ President and CEO Ron Gronback Jr. adds that with the automated system, “You turn the machine on and Excellerant knows every button you push. Turn it on and not run it, it knows that, too.”
“Every machine can be monitored wirelessly,” Norman says. “We use Excellerant for our DNC, for labor reporting, and for tracking part counts, uptime, and downtime. I have a 55" monitor on the wall outside my office that everyone can see. All the machines are highlighted in either yellow, green, or gray, with yellow indicating that a machine is idle, green that it’s running, and gray that there’s no connection or it isn’t turned on.”
Real-time machine data monitoring helps PDQ maximize spindle use.
“The more jobs you run through the system, the more representative the data becomes and that makes it much better,” Norman says. “The accurate, real-time data confirmed things that Ron and I knew all along. It wasn’t about finding out who is working and who isn’t. Excellerant gives us real data for better planning. Now, I can quote with accurate setup times, etc.”
Because Excellerant is integrated with the LillyWorks ERP, “when an operator puts in the proper information, it will trigger the materials replacement plan if we’re short.”
Excellerant also works with LillyWorks’ Protected Flow Manufacturing (PFM) feature, a predictive process tool that analyzes how parts are being made, machine efficiency, and the supply chain for hardware and raw materials. It then determines the order parts should be processed to maximize quality, efficiency, and on-time delivery. Algorithms consider the upcoming operations and indicate which job should be worked on next – it’s not always those due soonest.

Operator-friendly machine
Excellerant gives operators a way to report and document machine stoppages for part measurements, broken tools, or other interruptions. An operator can assign reason codes to times when the spindle’s not turning, and the office can analyze that input to determine downtime causes.
Rick Lees, Excellerant’s director of technical operations, says it’s important to involve the machine operators so they know how automated data acquisition can make their jobs easier. “If you tell the operators ‘here’s what we’re doing,’ it can get people’s guard up. But if you present the system as a way the operators can tell the office why a machine is idle, what element of the process resulted in a slowdown or shutdown, it provides instant and solid documentation for any problems.
“We’ve made Excellerant a more useful tool for PDQ by integrating it with their ERP system. When the PDQ front office receives an order, it enters the job into LillyWorks and assigns it to a machine or machines on the shop floor. Excellerant follows the job and displays the work order, the operation, and the number of parts needed so the operator knows what to do. As the job progresses to completion, the time data comes directly from the machine control. The operator doesn’t have to remember how much time was spent on that part.”
Operators can also see how many parts they should have at any time, how many parts they’ve made, and what’s next.
“They can see what’s next on the list and point out any concerns. If they say, ‘I have all the tools in this machine already, it will be a really quick changeover,’ it winds up being a real timesaver. This doesn’t work without the operators being in the loop,” Lee says.

Appreciated
Norman underlines the contributions of Excellerant staff to the success of the installation, including Lees, senior software architect Casey Marquis, and lead service technician Michael Paul Loiselle. “They listened. I can tell they are listening to other customers too, because since we started with Excellerant, they’ve updated it a few times.”
Lees says, “PDQ is in a very positive spot with Excellerant. Scott is an asset to making the product better because he’ll write us and ask, ‘Hey, can it do this, or can it do that?’ Customer use is the best tool to make the product better. The things we’ve added at their request have enhanced the system. We’re really partnering on this. We’re not just handing them devices and saying, ‘Here you go, good luck.’ You know, it’s all about the relationships.”

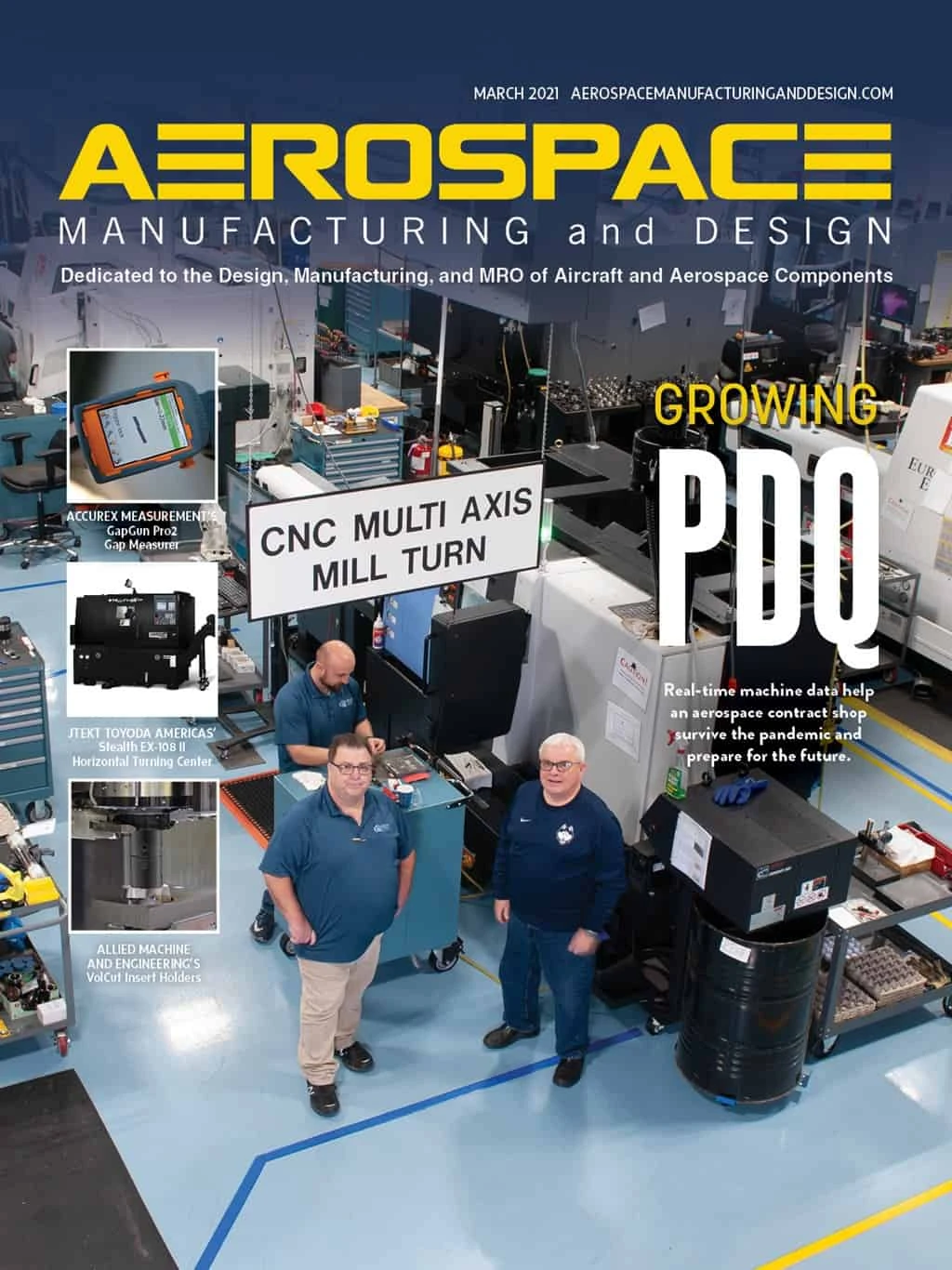
Explore the March 2021 Issue
Check out more from this issue and find your next story to read.
Latest from Aerospace Manufacturing and Design
- Strategies to improve milling and turning for medical components
- Being proactive about your business despite uncertainty
- Optimizing production of high-precision components through collaboration
- An inside look at the defense maritime industrial base
- Safran inaugurates advanced manufacturing and engineering hub
- Dillon pin location jaws
- NASA-supported technology outfits Venus Aerospace hypersonic engine
- To the Smoothest Surfaces, Finishes, and Beyond | Okuma GA26W