

Some time ago, I got into my car, began driving, and noticed I needed to force the steering wheel to one side to drive straight. Not being a car guy, it took me a considerable amount of time to realize the tie rods had fallen out of alignment. Similarly, when operating a CNC grinding machine or a multi-axis tool grinder, you may have become accustomed to the machine being out of calibration and you’ve learned to work around it.
Even with a machine that’s poorly calibrated, operators can still consistently produce parts or cutting tools that meet the required tolerances. Just as I managed to drive my car in a straight line by turning the steering wheel slightly, operators can make necessary adjustments to various geometric parameters to achieve a high-quality end product.
However, it’s crucial for operators to understand the disadvantage lies in increased setup times and therefore loss of productivity.
In 5- or 6-axis CNC tool grinding, you’ll waste more blanks to arrive at the first good tool. Moreover, when tasked with overseeing multiple misaligned grinders, there’s no viable method for managing these deviations (aka cheats).
The geometric accuracy of a CNC grinding machine holds utmost importance, as it directly impacts swift setup, efficient changeovers, and contributes significantly to the overall benefits of lean manufacturing practices and standardized operating procedures. A correctly adjusted grinder can be used by multiple operators without having to adjust for calibration errors.
Another aspect impacting efficient setup is accurate calibration of the grinding wheel. Most multi-axis grinders use a camera that produces an image of the grinding wheel profile which the operator can view and use mouse-clicks to accurately define the corners, angles, periphery, and radii of the wheel. This information is transmitted and integrated into the grinding program.
One commonly misunderstood aspect in tool grinding is the impact a corner radius on a grinding wheel has on the resulting tool geometry.
For instance, many operators choose to dress a small corner radius on a fluting or relieving wheel. This aims to extend the longevity of the corner while eliminating the need for constant attention until the corner has sufficiently worn in. Ballnose accuracy and radius tangency are also affected by unspecified corner radii.
Effective tool design software should be able to incorporate this corner radius into its calculations and enable precise 3D simulations. However, it’s essential for the wheel presetter to accurately capture this corner radius.
Another frequently overlooked aspect of wheel preparation is the need to preset the wheel on the wheel arbor intended for use in the machine, without any switching. This practice guarantees precise measurements and allows for the detection of potential excessive runout during the presetting process.
Addressing these aspects will contribute to enhancing the efficiency and bottom line in grinding, which is equally important for operators and owners alike.
About the author: Eric Schwarzenbach, founder of MyGrinding Inc., retired as president from Rollomatic Inc. – global builder of CNC grinding and laser cutting machines.
WANT MORE?
Enter your email to receive our newsletters.
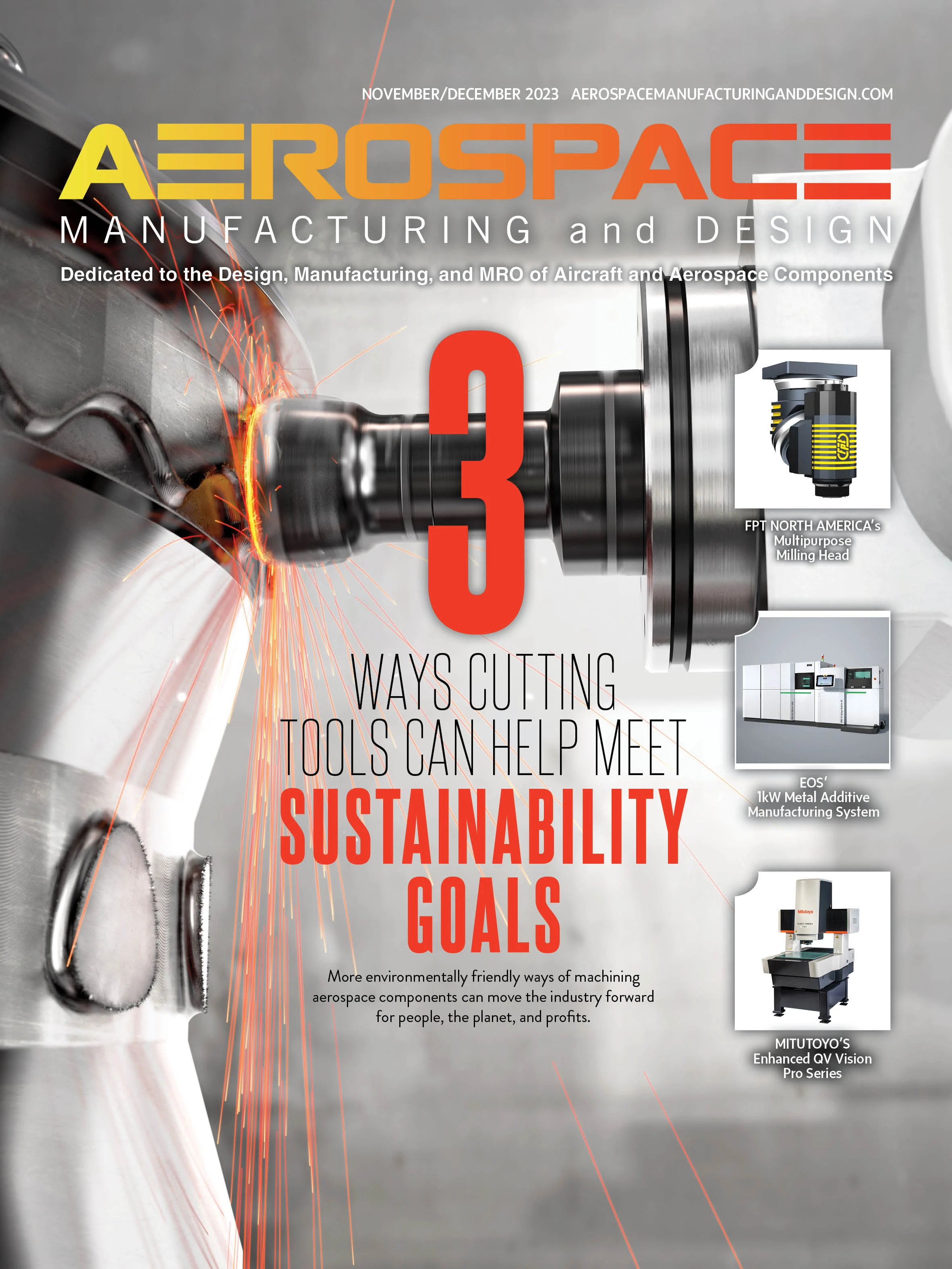
Explore the November December 2023 Issue
Check out more from this issue and find your next story to read.
Latest from Aerospace Manufacturing and Design
- Korean Air finalizes Boeing widebody order
- Walter introduces a performance copy milling grade
- Precision Aerospace Holdings acquires Clearwater Engineering
- CERATIZIT releases UP2DATE catalog
- #56 - Manufacturing Matters - How Robotics and Automation are Transforming Manufacturing
- Find out the latest developments in tool path strategies for machining
- Building, maintaining the Navy’s next generation of maritime platforms
- Address the challenges of machining high-temperature aerospace components