
Ceramic matrix composites – CMCs – have been talked about in aerospace for decades. Combining ceramic (metal and non-metal) materials with non- metallic fibers that retain their strength at high temperatures, CMCs make good candidates for the hot sections of turbine engines, especially since demand for greater jet engine efficiency and power has driven the need for materials able to withstand heat near the melting point of nickel and titanium. And, while CMCs offer the greatest payoff in jet engine hot sections, they also have benefits in engine nozzles, tail cones, and other components not subject to as much intense heat and pressure.
So why aren’t CMCs more prevalent? Some reasons became clear during the recent Ceramics Expo conference in Cleveland, organized by the American Ceramics Society. Dr. Jay Lane, engineering fellow – ceramics and composites, Rolls Royce Corp., with 32 years of ceramics experience, was one of the presenters. He noted that CMCs have one-third the density of nickel-based alloys and can reduce the weight of an engine system by 50% to 70% – that’s as much as 2,000 lb per civilian engine. But CMCs are costly to develop, verify, and produce, so they’ve mainly seen use in military turbine applications where performance outweighs cost.
However, CMCs are moving into next-generation commercial transport engines.
Steven Atmur, head of business development for COI Ceramics Inc., an affiliate of space launch vehicle and propulsion systems manufacturer Orbital ATK, explained the lack of a broad-based CMC supply chain. He noted that after initial enthusiasm for CMCs in the 1980s and ’90s, no commercial market developed, so the pioneering CMC suppliers were bought, sold, and/or closed. He pointed out that CMCs are not a commodity, and require engineers who understand the capabilities and limits of the materials and how to certify them – tasks only the engine manufacturers could afford. They took the supply chain in-house, vertically integrating CMC production for their own purposes. Atmur says it won’t be technology pushing CMC development; it will be industry pulling the CMC market. The supply chain will evolve only with production commitments and more customers.
Turbine engine original equipment manufacturers (OEMs) will focus on the engine core – high-volume, high-payoff parts. The parts the OEMs choose not to make themselves – low pressure turbine blades, exhaust components – will fall to the supply chain. Since lead times from design freeze to certification can take five years or more, small- and medium-sized enterprises will need other business to sustain them. They can’t all be dedicated to CMC part fabrication and repair – they will need to diversify – as many tier suppliers and machine shop managers already know.
Speaking of conferences, registration is now open for 72 distinct programs in the inaugural Integrated Industries Conference at IMTS 2016. Topics focus on motion, drive, and automation; the Industrial Internet of Things/Industry 4.0; and surface technology. You can find out more about them at our website, which you may have noticed, has a new URL: www.AerospaceManufacturingAndDesign.com. Yes, it’s long, but easy to remember: the name of this magazine dot-com. And once you bookmark it, you won’t have to type it into your web browser. – Eric
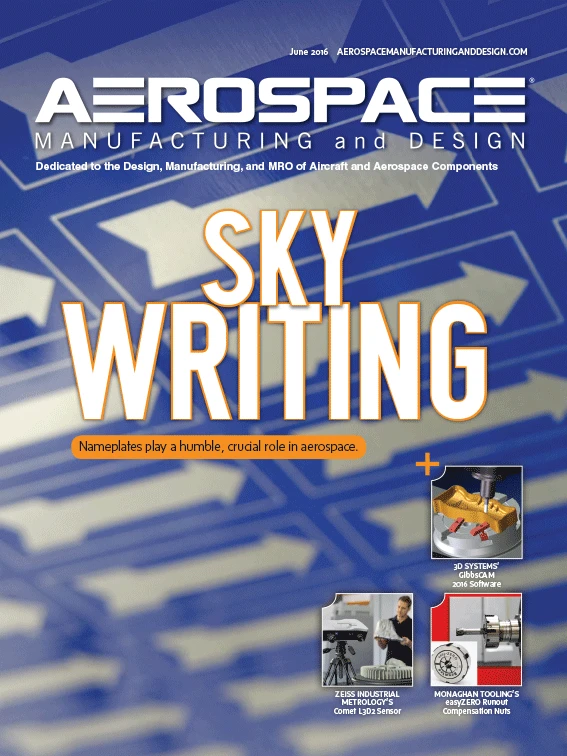
Explore the June 2016 Issue
Check out more from this issue and find your next story to read.
Latest from Aerospace Manufacturing and Design
- Revitalizing the Defense Maritime Industrial Base with Blue Forge Alliance
- Safran Defense & Space opens US defense HQ
- Two miniature absolute encoders join US Digital’s lineup
- Lockheed Martin completes Orion for Artemis II
- Cylinder CMMs for complex symmetrical workpieces
- University of Oklahoma research fuels UAS development
- Motorized vision measuring system
- Everyone's talking tariffs