When bonding metals, the metals must melt where they meet or some molten metal must be introduced between the pieces. When the metal solidifies, a solid bond forms. However, researchers at the Massachusetts Institute of Technology (MIT) found that melting can inhibit metal bonding rather than promote it.
The counterintuitive finding could impact the design of coating processes or 3D-printing systems that require materials sticking together.
Post-doctoral researchers Mostafa Hassani-Gangaraj and David Veysset and professors Keith Nelson and Christopher Schuh reported their findings in the journals Physical Review Letters and Scripta Materialia.
High-speed imaging reveals that melting induced by impacting particles of metal can impede bonding. The optical setup, with a high-speed camera that uses 16 charged-coupled
Until now, these

That uncertainty has led to questions about whether the metal particles actually melt as they strike the surface. The new images make it clear that under some conditions, metal particles sprayed at a surface
When engineers find that a coating material isn’t bonding well, they often increase spray velocity or temperature to increase melting chances. The new results reveal the opposite: melting should be avoided.
The best bonding happens when the impacting particles and impacted surfaces remain in a solid state but splash outward in a way that looks like liquid.
Schuh says, “To stick metal to metal, we need to make a splash without liquid. A solid splash
The findings could be relevant for processes used to coat engine components in order to reuse worn parts rather than relegating them to the
In addition to coatings, the new information could also help in the design of some metal-based additive manufacturing (AM) systems, where it is critical to ensure that a layer of printing material adheres solidly to the previous layer.
Massachusetts Institute of Technology
www.mit.edu
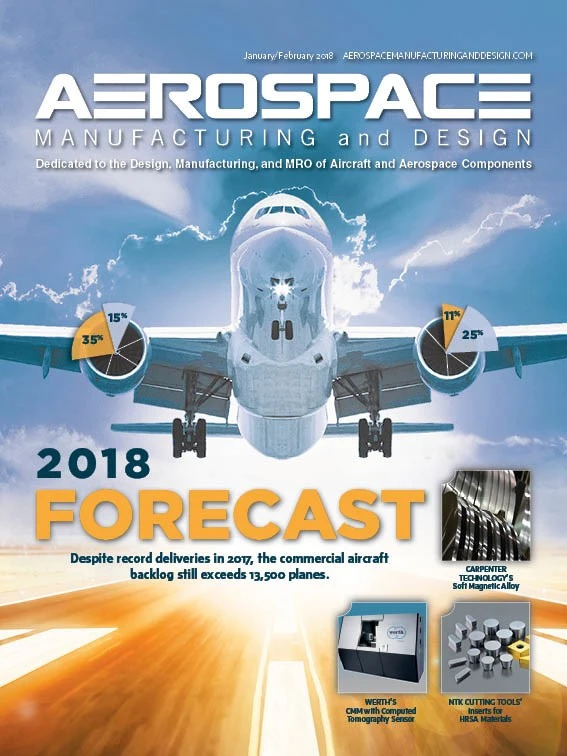
Explore the January February 2018 Issue
Check out more from this issue and find your next story to read.
Latest from Aerospace Manufacturing and Design
- Titanium drop bottom furnace installation underway
- Solid carbide taps for demanding materials
- The Partner Companies acquires Precision Eforming
- Hall Effect angle sensors
- July is for learning – so drop in for this month’s second Manufacturing Lunch + Learn
- Essential strategies to protect your data
- NASA selects instruments for Artemis lunar terrain vehicle
- Twin-cutter boring head