
In my 30-year aerospace career, I’ve been part of several engineering teams that developed many aircraft systems. All had one thing in common: a date in the future when development had to stop so the aircraft could be built. That deadline meant we had a finite amount of time to finish our work. I always thought we needed more time to solve design issues, to make the design better before we built it. Maybe what we really needed wasn’t more time, but a faster way to work through our design iterations.
A typical aircraft development program involves multiple teams designing systems and subsystems in parallel. Each team goes through as many iterations as time allows to find the best one before the critical design review, while balancing performance, weight, schedule, and cost considerations. Inevitably, one team discovers their part of the project has a serious issue requiring redesign, and their changes cause other teams to redesign their systems, too.
This process can only be repeated a few times until the engineers have to put down their pencils and hand over their work to be built. This process can create aircraft with optimized subsystems that meet requirements, but often the overall aircraft becomes suboptimized. Complex aircraft almost always have issues not discovered until they’re built, when it can cost hundreds of times more to fix a problem found in flight testing than one found in design.
Generative design is the faster method I always wanted earlier in my career: a way to help engineers deliver the very best products and still meet design and delivery dates. It enables engineers to move faster from high-level architecture to detailed physics-based designs, allowing many more iterations to produce designs with fewer problems once built.
Generative design sounds like science-fiction, but it’s already embedded into real aerospace development tools.
Generative design today

Many generative capabilities now exist across various engineering domains. Generative tools for the mechanical domain are integrated with topology optimization, where an algorithm can make a part as light as possible while still meeting a desired stress level. The algorithm can use finite element analysis to examine the materials available and the stress the part will experience throughout its life cycle, then bolster areas that might break. The result is a part that weighs as little as possible yet maintains maximum strength.
Once a part is designed, it must be built efficiently. How parts are manufactured is just as important as physical qualities. Fortunately, the tools also incorporate manufacturability as a consideration when generating a part’s design, so generated parts can be optimized for peak functionality and producibility.
Modern aircraft are more than just mechanical items – they integrate mechanical, electrical, electronic, software, and other systems. Similar generative capabilities can be found in all these engineering domains. In electronics, there are tools to generate and test complex integrated circuit designs. Tools in the electrical domain can generate detailed wire harness designs and create the artifacts needed to build and maintain those designs.
One part of generative design is the algorithm that auto-generates a complex physical part, but operating and maintaining an aircraft for decades also can be a significant part of its life cycle cost. Operation and maintenance require many volumes of support data, but translating designs to support data can be tedious, mundane, and expensive. Generative design can automate complex design tasks and automate mundane documentation tasks as well. Companies are saving thousands of hours creating documentation with generative design tools.
How this helps aerospace
All these capabilities help address the need to go faster. Much of engineers’ design cycle time is spent exploring dozens of iterations. After selecting a final design, they focus on the many details that determine system functionality. Often, engineers find the design chosen initially wasn’t the best one. This restarts the time-consuming process of detailed design.
By automatically creating aspects of a product’s design, generative design enables engineers to bring conceptual ideas to physics faster, optimizing products and running them through simulations to ensure they meet requirements efficiently. This helps engineers eliminate bad choices earlier, giving them more time to explore additional choices and trade-offs between iterations, as well as more time to integrate disparate domains and optimize the product.
Generative design of the future

With the rise in artificial intelligence (AI), Generative AI has gained popularity, but generative design has been around much longer and isn’t the same thing. Generative AI defines a capability using a large language model (LLM) to produce an artifact – text, imagery, music, or code. Generative design is typically physics based, which allows it to have more engineering applications.
Generative AI is already being integrated with design tools through copilots and digital assistants, accelerating engineering processes by automating mundane tasks, such as data management, that keep engineers from the work of bringing their ideas into fruition. Marrying generative design tools with LLMs presents an opportunity to automate the complex. Generative AI combined with generative design will create even more powerful design tools with better human-machine interfaces.
Generative design now is largely confined to individual engineering domains, but as design tools improve, the generation types they can accomplish will grow. AI’s data management capabilities will help bridge engineering domains. AI will organize and transfer data across various tools and domains with more universal data models to facilitate far better connectivity, giving rise to an advanced form of multi-domain generative design.
The future is AI-driven generative design. By automating many tasks with generative design and AI, engineers can dedicate more time to critical thinking and high-level engineering. Human engineers will still make the big decisions and validate the final products.
A call to action
The time is now to invest in generative design. There are many ways to dramatically improve efficiency with the tools already available today. Companies investing now will see a quick return-on-investment and continue to reap the rewards as the technology evolves, ushering in new forms of engineering once confined to the realm of science-fiction.
Siemens Digital Industries SoftwareGet curated news on YOUR industry.
Enter your email to receive our newsletters.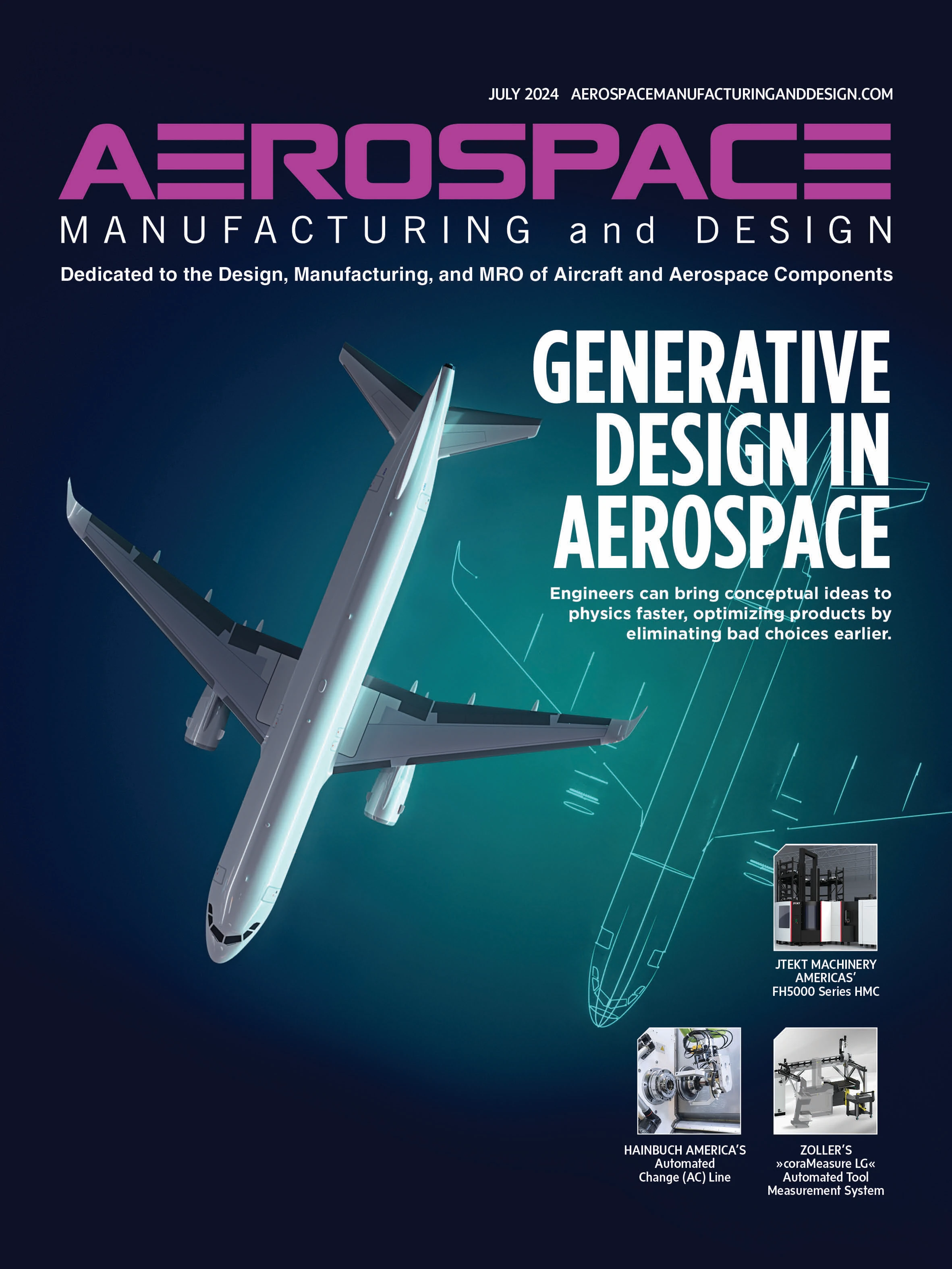
Explore the July 2024 Issue
Check out more from this issue and find your next story to read.
Latest from Aerospace Manufacturing and Design
- Cyient Group, Deutsche Aircraft finalize multi-year contract
- High surface quality at high speed
- #57 - Manufacturing Matters - Agile & Robust Supply Chain Management with Lisa Anderson
- Take control of your manufacturing business despite supply chain turmoil
- Strengthening the defense maritime industrial base for national security, economic resilience
- Register now to learn solutions for high-temperature aerospace machining challenges
- Expertise on machining, joining offered in April’s Manufacturing Lunch + Learn
- NASA offers free high school engineering program this summer