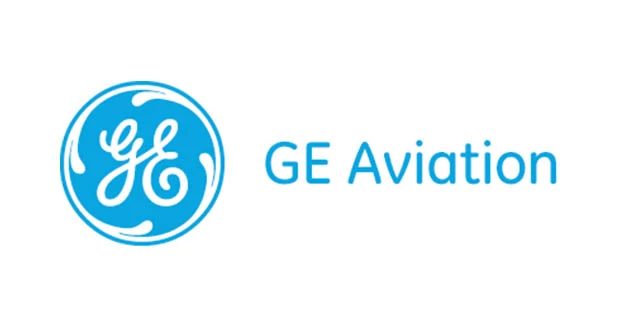
Asheville, North Carolina – GE Aviation, recently hosted a grand opening ceremony at the site of its new advanced composites factory near Asheville in Western North Carolina.
GE Aviation's Sanjay Correa, vice president, Ceramic Matrix Composite (CMC) Program, Colleen Athans, vice president, Supply Chain and Mike Kauffman, general manager, Composites Manufacturing, were joined by Gov. Pat McCrory, Congressman Mark Meadows, and officials from the Asheville Area Chamber, Buncombe County, City of Asheville, and N.C. Department of Commerce to commemorate the grand opening.
The new 170,000ft2 facility will be the first in the world to mass produce engine components made of advanced ceramic matrix composite (CMC) materials.
GE has begun hiring at the new CMC components plant. Within five years, the workforce at the plant is expected to grow to more than 340 people.
The existing workforce at GE Aviation's current machining operation in Asheville will gradually transition to the CMC components plant.
The introduction of CMC components into the hot section of GE jet engines represents a significant technology breakthrough for GE and the jet propulsion industry. CMCs are made of silicon carbide ceramic fibers and ceramic resin, manufactured through a highly sophisticated process and further enhanced with proprietary coatings. GE plans to introduce more CMC components into future engine development programs.
The specific CMC component to be built in the new Asheville facility is a high-pressure turbine shroud. More importantly, this CMC component will be on the LEAP jet engine, being developed by CFM International, a joint company of GE and Snecma (Safran) of France and will mark the first time CMCs are used for a commercial application. The LEAP engine, which will enter airline service in 2016, will power the new Airbus A320neo, Boeing 737 MAX and COMAC (China) C919 aircraft.
Remarkably, CFM to date has logged total orders and commitments for more than 7,700 LEAP engines. There will be 18 CMC turbine shrouds in every LEAP engine produced, thus setting the stage for high, long-term production volume at the Asheville plant.
Source: GE Aviation
Latest from Aerospace Manufacturing and Design
- Our first webinar of 2025 highlights additive manufacturing
- Pegasus Airlines orders up to 200 Boeing 737-10 airplanes
- ModuleWorks' 2024.12 software components
- Archer completes construction of high-volume manufacturing facility
- Curtiss-Wright’s NXP 16-Core Arm-based VPX single board computer
- Happy New Year
- 2024 Favorites: #1 Article –2024 Forecast
- 2024 Favorites: #1 News – Honeywell to expand Kansas aerospace manufacturing facility