A stretchable, flexible patch could make ultrasound imaging easier for odd-shaped structures, such as aircraft wings, engine parts, and turbines – objects that are difficult to examine using conventional ultrasound equipment.
The versatile patch is a more convenient tool to inspect
Today’s ultrasound devices are difficult to use on objects that don’t have perfectly flat surfaces. Probes with flat and rigid bases can’t maintain good contact when scanning across curved, wavy, angled, and other irregular surfaces.
“Elbows, corners, and other structural details are the most critical areas in terms of failure – they are
Gel, oil, or water is typically used to create better contact between the probe and the object’s surface. But too much of these substances can filter some of the signals. Conventional ultrasound probes are also bulky, making them impractical for inspecting hard-to-access parts.
The research team’s soft ultrasound probe does not require water, gel, or oil.
The probe is a thin patch of silicone elastomer patterned with an island-bridge structure – an array of small electronic parts (islands) each connected by spring-like structures (bridges). The islands contain electrodes and piezoelectric transducers that produce ultrasound waves when electricity passes through them. The spring-shaped, copper-wire bridges stretch and bend, allowing the patch to conform to nonplanar surfaces.
Researchers tested the device on an aluminum block with a wavy surface. The block contained defects 2cm to 6cm beneath the surface. Researchers placed the probe at various spots on the wavy surface, collected data, and reconstructed images using a customized data processing algorithm. The probe imaged the 2mm-wide holes and cracks inside the block.
“It would be neat to be able to stick this ultrasound probe onto an engine, airplane wing, or different parts of a bridge to continuously monitor for any cracks,” says Hongjie Hu, a materials science and engineering Ph.D. student at UC San Diego and co-first author of the study.
The device is still at the proof-of-concept stage, so it does not provide real-time imaging. It also needs to be connected to a power source and a computer to process data.
“In the future, we hope to integrate power and a data processing function into the soft ultrasound probe for wireless, real-time imaging and videoing,” says Sheng Xu, a professor of nanoengineering at the UC San Diego Jacobs School of Engineering and the study’s corresponding author.
University of California San Diego
http://ucsd.edu
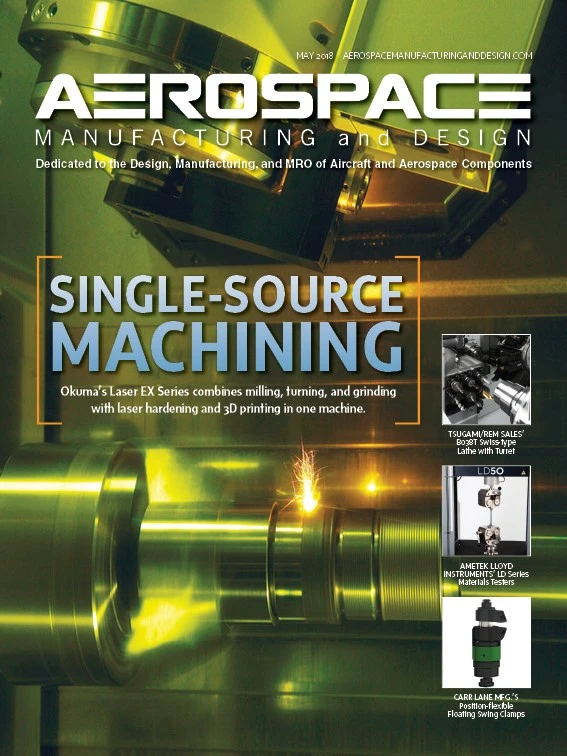
Explore the May 2018 Issue
Check out more from this issue and find your next story to read.
Latest from Aerospace Manufacturing and Design
- High surface quality at high speed
- #57 - Manufacturing Matters - Agile & Robust Supply Chain Management with Lisa Anderson
- Take control of your manufacturing business despite supply chain turmoil
- Strengthening the defense maritime industrial base for national security, economic resilience
- Register now to learn solutions for high-temperature aerospace machining challenges
- Expertise on machining, joining offered in April’s Manufacturing Lunch + Learn
- NASA offers free high school engineering program this summer
- Pemamak's PEMA Vision 3D software