
Version 8 of the flexible pallet container (FPC 8) provides easy and extendable automation for one to three CNC milling machines with 400mm to 1,000mm pallets. It integrates with horizontal machining centers and offers machine tool utilization up to 85%, short setup times, and high lights-out production capacity. The FPC 8 features an optional basic loading station (LSB) with pallet height adjustment for jobs with various fixture heights, to provide personalized work positions for each operator while clamping/unclamping workpieces. Systems with a single fixture height or few users can use Fastems’ standard option compact loading station (LSC).
IMTS 2022 Booth #339186
Gear making machines

The GE15HS gear hobbing machine produces gears with a maximum diameter of 150mm for robotic and automation applications.
The main cutting spindle’s high-speed, high-torque direct-drive motor provides a maximum spindle speed of 6,000rpm – 3x faster than previous models. The high-efficiency spindle holding the workpiece uses a special table providing high rigidity and high-speed rotation to handle the necessary thrust load. Cutting gears with super-hard cutting tools yields a surface roughness of less than Ra0.4*4; on par with gear grinding. The machine offers stable mass production with a maximum cutting speed of 1,500m/min.
IMTS 2022 Booth #237036
Machining cell and software solutions

OmniVance machining cell and software solutions offer greater flexibility and simplicity to sanding, polishing, cutting, and surface finishing.
The cell can perform up to eight different applications, while its intuitive machining software simplifies programming and reduces setup time up to 92%. The software calibrates tools and work objects automatically, reducing re-calibration time. The integrated path tuning function enables users to easily edit thousands of path points.
Non-programming experts can perform and monitor machining operations with an intuitive and user-friendly interface.
IMTS 2022 Booth #215110, #236520
Milling head-spindle combination

For high-volume material removal, the D27 milling head paired with the MFW-2714/20 HSK-100 spindle provides maximum stability and precision for 5-axis machining.
IMTS 2022 Booth# 237470
Ball-end cutter

The POW•R•ARC ball-end cutter is designed for contouring and chamfering at the fastest possible speed and feed rate in most materials. It cuts smoothly in workpieces with dissimilar materials – no digs, no handwork needed. Available with 6 or 8 flutes, the ball-end cutter features advanced geometries and next-generation coating for faster feed rates, greater lubricity, reliable chip ejection, and double the tool life over tested competitors.
It cuts and finishes in one pass in hardened metals up to 62HRc, aluminum, stainless steel, low carbon steel, and super alloys such as high nickel alloys, cobalt chrome, and titanium. It’s effective in low-speed, high-speed, and 5-axis machines. Order with long necks for working in deep pockets and easier maneuvering around mold guide pins.
IMTS 2022 Booth #431522
Surface, profile grinder

For complex shapes in demanding materials, including turbine blades and vanes, the Blohm Planomat XT machine series offers efficient surface and profile grinding operations. Available in five sizes with grinding ranges from 400mm x 800mm (15.7" x 31.5") to 600mm x 2,000mm (23.6" x 78.7"), the machines are suitable for applications from single parts to complex workpieces, with maximum 800kg (1,672 lb) workpiece weights.
With an available 24.5kW (32hp) spindle, the Planomat XT features an optional eight-pocket tool changer, precision linear guideways, and high-quality recirculating ball screws for precision operation. The machine performs surface and profile grinding applications ranging from creep feed to multi-part production in a single setup.
It accepts grinding wheels up to 400mm (15.75") in diameter by 160mm (6.3") in width. For optimal dressing, the table-mounted dressing device handles diamond profile rolls up to 200mm (7.87"). The articulating dressing attachment enables continuous-path dressing control using the machine’s axes and CNC operation of the dresser’s articulating axis.
United Grinding North America Inc.
IMTS 2022 Booth #236802
5-axis machining center

The MedCenter5AX is an ultra-high precision, 5-axis machining center offering accuracy and speed for expanded capability in the machining of highly complex small to medium, multi-sided parts in one setup. The unit is equipped with a 30,000rpm 18kW (24.5hp) direct drive, HSK-E40 spindle offering rigidity in construction and function while allowing for fine finish capabilities. For small diameter tools and hard milling, the machine offers a standard air-through spindle feature for dry cutting and is also equipped to handle up to 1000psi coolant through the spindle for deep-hole drilling. It features a newly designed and field expandable 24-station automatic pallet changer with a high- performance 120 tool ATC.
Kitamura Machinery of USA Inc.
IMTS 2022 Booth #339133
Get curated news on YOUR industry.
Enter your email to receive our newsletters.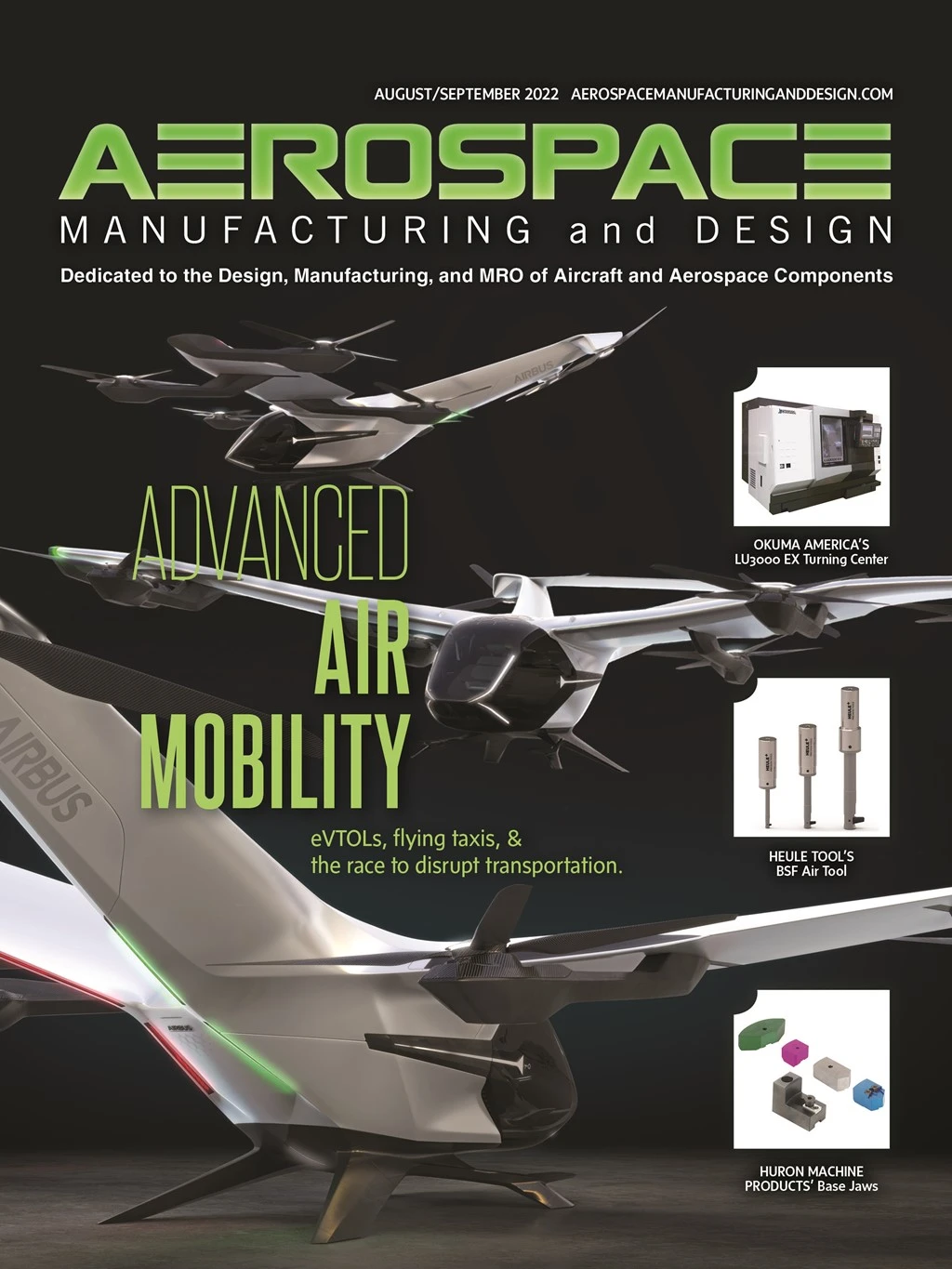
Explore the August September 2022 Issue
Check out more from this issue and find your next story to read.
Latest from Aerospace Manufacturing and Design
- Precision Aerospace Holdings acquires Clearwater Engineering
- CERATIZIT releases UP2DATE catalog
- #56 - Manufacturing Matters - How Robotics and Automation are Transforming Manufacturing
- Find out the latest developments in tool path strategies for machining
- Building, maintaining the Navy’s next generation of maritime platforms
- Address the challenges of machining high-temperature aerospace components
- Elevate your manufacturing operations with April’s Manufacturing Lunch + Learn
- America Makes announces IMPACT 3.0 Project Call worth $4.5M