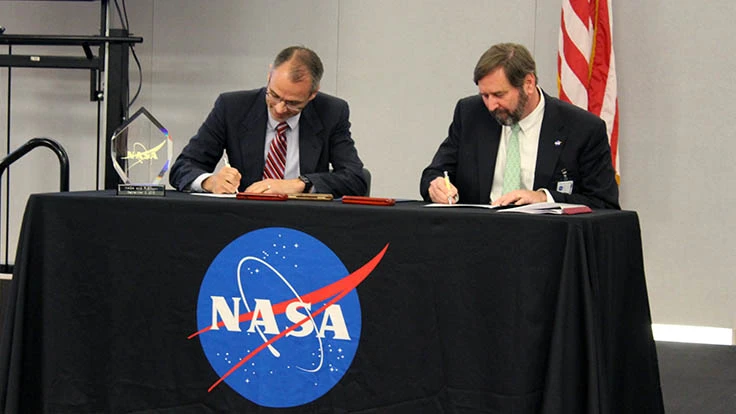
NASA Glenn Director Jim Free and Neil McDonough, FLEXcon president and CEO, sign agreement licensing polyimide aerogels.
Cleveland, Ohio – FLEXcon, a Spencer, Massachusetts-based adhesive coating and laminating producer, recently licensed NASA Glenn Research Center’s patent-pending polyimide (PI) aerogels. The exclusive license allows FLEXcon and its affiliate, Blueshift International Materials Inc., to manufacture and market Glenn’s polyimide aerogels for aerospace and other applications.
NASA Glenn Director Jim Free and FLEXcon President and CEO Neil McDonough participated in the licensing agreement signing ceremony at NASA’s Glenn Research Center in Cleveland, Ohio.
“At FLEXcon, we are excited about the business opportunities the polyimide aerogel technology affords us,” McDonough said. “As a supporter of U.S. manufacturing and innovation, FLEXcon is excited to be a manufacturing partner that can help NASA develop its ideas into commercial reality.”
Aerogels are highly porous solids made by drying a wet gel without shrinking. The small pore size of 10nm to 40nm makes for good insulation, which can be 2x to 4x better than fiberglass under ambient conditions and 10x to 15x better in a light vacuum – advantageous for space applications, according to NASA researchers.
Aerogels developed in the 1990s were silica-based and brittle, easily broken into dust by light finger pressure. The aerogel cube of smoke from the 1990s, “That’s your dad’s aerogel,” John Sankovic, Glenn’s director of technology incubation and innovation, told Aerospace Manufacturing and Design in an exclusive interview.
The new polyimide aerogels are stronger and lighter at similar densities – a small block of the material can support the weight of an automobile.
McDonough also told Aerospace Manufacturing and Design, “The ability to cut fine shapes, to make it fit into different things, for us to be able to laminate different materials to it, takes it from being a base material to making it work in different applications.”

Uses for the polyimide (PI) aerogel technology include insulation for cryotanks and spacesuits. For example, it will be one of the layers of the high-pressure extravehicular activity gloves designed by Final Frontier Design for a NASA Small Business Innovation Research contract. The goal is to develop advanced spacesuit gloves suitable for use in the Martian environment and other long-duration missions. FLEXcon will also provide additional materials for the glove.
Another potential PI aerogel application is use as an antenna substrate, due to its low dielectric properties, and in lightweight power and data cables.
“We’re all involved in trying to grow industry in America, and the best way to do that is by bringing more technology into what we’re making,” McDonough said. “That’s my real interest in understanding what NASA has developed in so many different areas. If we can add to our manufacturing base, it will add to the success of all of us.”
In addition to its spencer, Massachusetts, headquarters, FLEXcon has manufacturing and distribution centers in San Antonio, Texas; Columbus, Nebraska; Elkton, Kentucky; and Glenrothes, Scotland.
NASA was able to scale-up its PI aerogel in collaboration with help from the University of Akron’s National Polymer Innovation Center.
Additional information from FLEXcon, NASA GRC
Latest from Aerospace Manufacturing and Design
- Electra.aero to lead sustainable commercial airliner development
- SMW Autoblok's TMS-2G Quick-Change System
- IMTS 2024 Booth Tour: INDEX Corporation
- Inventory traceability and document management
- Oklahoma Aviation Academy breaks ground for new building
- MIDACO’s automatic 4-pallet changer with trunnion system
- IMTS 2024 Booth Tour: Tornos Technologies
- A Primer on Defense Contract Manufacturing