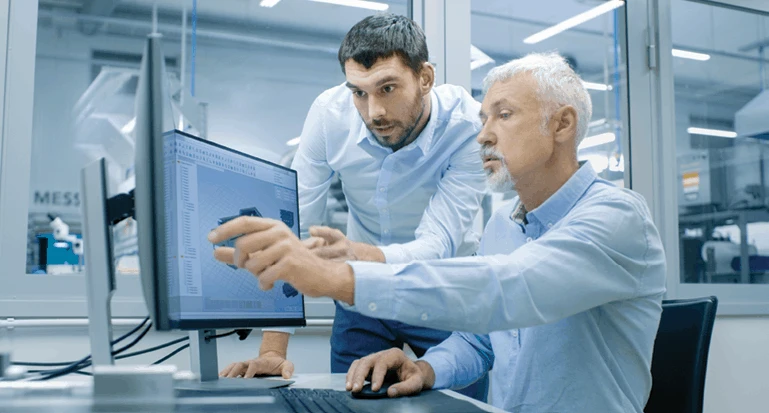
Delkin Devices

Technologies based on the Industrial Internet of Things (IIoT) are expanding exponentially, and Industry 4.0 has sparked a wave of transformation that is quickly changing the way aerospace manufacturers operate.
One challenge – managing massive amounts of data produced by aerospace IIoT systems. A jet can generate hundreds of gigabytes of data per minute. And data storage devices must function in extreme environments. For IIoT applications to capture, store, analyze, and share information, they require versatile storage devices that can withstand high and low temperatures, humidity, and vibration.
The rugged durability of industrial flash storage devices provides a solution for applications such as helicopter black box recordings, jet mission data collection, unmanned aircraft base station and flight data recording, and in-flight entertainment and WiFi services.

Industrial flash storage devices must be able to handle massive amounts of data and operate from -40°C to 85°C for prolonged time periods without fail. Ruggedized devices use single layer cell not-and (SLC NAND) architecture, since it’s more reliable for IIoT purposes.
Unfortunately, many aerospace manufacturers perceive flash memory as a commodity, and purchase commercial off-the-shelf (COTS) parts that meet type, memory capacity, and form factor specifications. They may overlook considerations such as workload (frequency of reading/writing large amounts of data), power management (dirty power, power cycling, power failure), and environmental conditions (temperature, vibration). These factors can corrupt data and cause other errors, reducing storage reliability and lifespan.
“Many aerospace manufacturers purchase flash storage devices over the Internet only to discover at the launch of the product there were unexpected issues due to inaccurate assumptions about the environment and workload requirements,” says Tony Diaz, product manager for Delkin Devices, a supplier of non-volatile flash solid state drives (SSD), cards, and modules.
In aerospace, this can lead to unexpected failure of mission-critical data and compromise safety features. Given the vital role of storing mission-critical data, Diaz says most industrial flash storage devices require some customization to meet real-world workload requirements.
Workload demands
All flash storage has a finite life, depending on how well it’s managed and workload requirements. To optimize and extend the life of a flash storage device, carefully consider how data is written to it.
New data cannot be saved to flash until old data is erased, and only a finite number of programming/erasing cycles can be performed before wear renders flash unreliable. Some flash media are not used evenly, further reducing a device’s life.
Options to extend flash device life include reducing unnecessary file copying or data downloading, consolidating writes, wear-leveling techniques, and selecting whether data are written sequentially or randomly.
“If an aerospace manufacturer misjudges or misunderstands the workload requirements, there are implications for the storage,” Diaz explains. “It could be as simple as unexplained errors in the field, or it could be a situation where they are wearing out the flash memory much faster than they realize.”
Environmental conditions
When customizing flash storage, consider mechanical ruggedness. Ask, is the application subjected to unusual amounts of vibration? Does the typical operating environment exceed standard industrial storage parameters?
Although designed to be rugged, each industrial flash storage application has different operating requirements. Customizing mechanical ruggedness can alleviate concerns about failures associated with operating conditions.
To ensure a storage device will work as expected, partner with a manufacturer who offers testing reliability services. At its manufacturing facility in San Diego, California, Delkin Devices offers design verification testing, ongoing reliability testing, and accelerated lift testing to simulate long-term operating conditions.

Power issues
Losing power during a write operation can cause data loss if data aren’t saved completely. Even a small amount of data loss during a power failure can cause significant ongoing problems, including fatal corruption of the entire system. It can also cause inefficient use of memory capacity, which can dramatically shorten the embedded flash storage lifespan.
Reducing external sources of power loss mitigates the risk of power fails. However, power failures can still occur, so internal protections are essential for reducing data loss risk. For flash memory systems that handle critical data, that means built-in power loss controls, including systems for monitoring power supply and the ability to recover data after losing power during a write operation.
Dirty power from outages, brownouts, surges, and power spikes is another concern. When direct current (DC) dips below the required threshold, errors can occur in equipment critical to airplane or spacecraft operation.

Operational issues
How a manufacturer sources parts, engages suppliers, and ensures that the sourced parts will be available throughout the product life cycle are important issues.
Bills of materials (BOM) of commercial-grade flash storage are often updated without warning. Although this helps consumer manufacturers maximize functionality while minimizing price, aerospace manufacturers need consistency and reliability.
Diaz says manufacturers can achieve a higher standard when component parts are controlled and configuration locked.
“Once qualified, the flash, controller, and firmware will not change as long as the part number is active. If anything needs to be changed, changing the part number essentially guarantees that the customer is notified and the BOM is updated,” Diaz explains.
Reducing risks
COTS flash storage may have the right specs and cost less than a customized part from a supplier, but there are always hidden costs and risks.
Diaz says manufacturers should engage a supplier from the beginning of the design process to ensure they get what they need for the product’s entire life cycle.
“Aerospace manufacturers may not spend much time considering flash storage,” Diaz adds. “But given the critical nature of data in today’s devices, there is too much risk to take industrial flash for granted.”
Get curated news on YOUR industry.
Enter your email to receive our newsletters.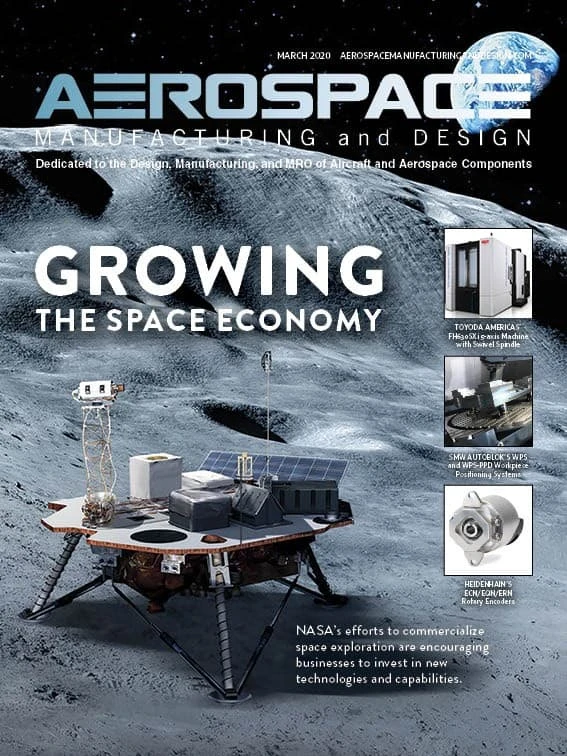
Explore the March 2020 Issue
Check out more from this issue and find your next story to read.
Latest from Aerospace Manufacturing and Design
- Ralliant to establish global headquarters in North Carolina
- Philatron MIL-DTL-3432 military cables
- Beyond Aero refines its hydrogen-electric light jet
- Americase's advanced protective solutions
- Social media - what are your thoughts
- GE Aerospace secures Air Force engine contract
- Thomson Industries' online sizing and selection tool
- #53 - Manufacturing Matters - 2024 Leaders in Manufacturing Roundtable