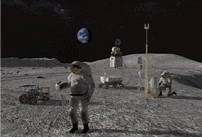
Taking the next giant leap in space exploration, NASA’s Artemis Program will land a woman and man on the moon by 2024. Critical to this mission will be supportive technologies and robotics to explore the lunar surface, including the Cold Operable Lunar Deployable Arm (COLDArm) robotic device that can function in extreme cold without the heating or insulation required on traditional space arms.
A collaboration between Motiv Space Systems and NASA’s Jet Propulsion Laboratory (JPL), the design benefits from Motiv’s motor control capability used for robotic applications, developed as part of a NASA SBIR effort. The SBIR technology demonstrated a path for avionics that can work at cryogenic temperatures without heaters. Meanwhile, JPL was working on actuation technology, specifically bulk metallic glass-based gears that can operate at cryogenic temperatures.
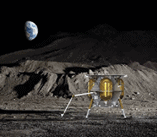
and NASA Jet Propulsion
Laboratory
“Several years ago, we talked about finding an application for each of those respective technologies because they interact in the real world on a regular basis,” says Tom McCarthy, VP of business development at Motiv Space Systems. “We had an opportunity to propose together to the NASA [space technology mission directorate] STMD office for a lunar technology, payload development. The solution was the fusion of bringing both of our technologies together to deliver more of a system application.”
Design components
A primary goal of the Artemis program is to deploy systems that can survive and operate during the lunar night when it gets extremely cold, and support the lunar habitats or laboratories intended to be built on the moon. That’s where the COLDArm comes into play. The technology being developed for the lander uses electronics and lubricant-free mechanical components that can function in environments as cold as -279°F. The design will reduce the power needed for a rover or lander’s operations, enabling robots equipped with the arm to extend missions. The robot arm is also adaptable, potentially supporting a variety of rovers and landers the space agency has planned for future missions, McCarthy explains.
The electronics and actuation system are core pieces of the robotic arm, and the team is exploring technologies to address a unique challenge for the arm’s interconnect hardware. In cold temperatures, harnesses tend to stiffen, making flexing and bending more difficult. There’s also some early testing on different approaches to ensure a compliant harnessing system to provide an interface with the instruments or any of the sensing devices that need to get information back to the computer.
The team is also paying attention to the environmental details throughout their design approach, considering how these factors may affect the robot’s thermal and mechanical cycling.
“There has to be compliance built into the system and the mechanical levels, as well as the electronic levels, or at least an understanding of how many thermal cycles these systems can survive in these early demonstrations,” McCarthy adds.
The hope is that knowledge gained from the testing phase will lead to more robust systems. For early missions, the robot will need to be operable for only a few days, but ultimately the team anticipates the device being functional for hundreds of cycles and many years of operation.
“That accumulated knowledge through the testing campaign, the analysis, and the design campaign, will give us great intuition about how to extend the life of these systems, and therefore, extend the missions themselves,” McCarthy says.
Capabilities
Once built, the team will test the completed system in a thermal vacuum chamber at cryogenic temperatures and take it through its paces – making sure it can turn on, start up, and go through all the robotic motions and perform functions such as scooping and manipulating payloads.
As McCarthy explains, scientists hope to use the COLDArm as a geotechnical survey instrumentation tool of the lunar regolith. Throughout testing, the team will determine the poses applicable for scooping materials and seeking out possible life-sustaining resources available on the surface. They’ll also look at other scientific instruments with a few different payload opportunities. The arm could be used as a pointing device to deliver a camera or a spectrometer application on the end of the arm. There’s also potential for the arm to be used as a utility tool for the lander itself.
“If there was a little rover or a small payload that resided on the lander but needed to get to the surface, depending on where it was stowed on the lander, the arm could pick up that item and deliver it to the surface,” McCarthy says. “It would be an aide to another payload provider. Each of those modes will be tested to give us confidence that the system will work when eventually it’s integrated into one of the landers and makes its journey to the moon.”
Deeper exploration
Robotics will continue to be key technologies as missions continue for finding new discoveries and habitable environments beyond Earth. As more environments are explored, with each posing unique challenges, these devices will allow people to safely and quickly collect significantly more data.
“For a lot of these cases, there aren’t habitable environments for humans to operate, or they’re too distant,” McCarthy says. “Robotics allows us to have that up-close and personal approach and feel to understand more about a planet’s creation.”
McCarthy predicts that robotics will take the lead in ensuring sustainable missions.
“It’s very exciting,” he concludes. “Robotics don’t just help us get there, but they help us, in some cases, return material from these foreign worlds back to our labs for study. There are great opportunities to learn and expand our knowledge, and robotics is the way to do it.”
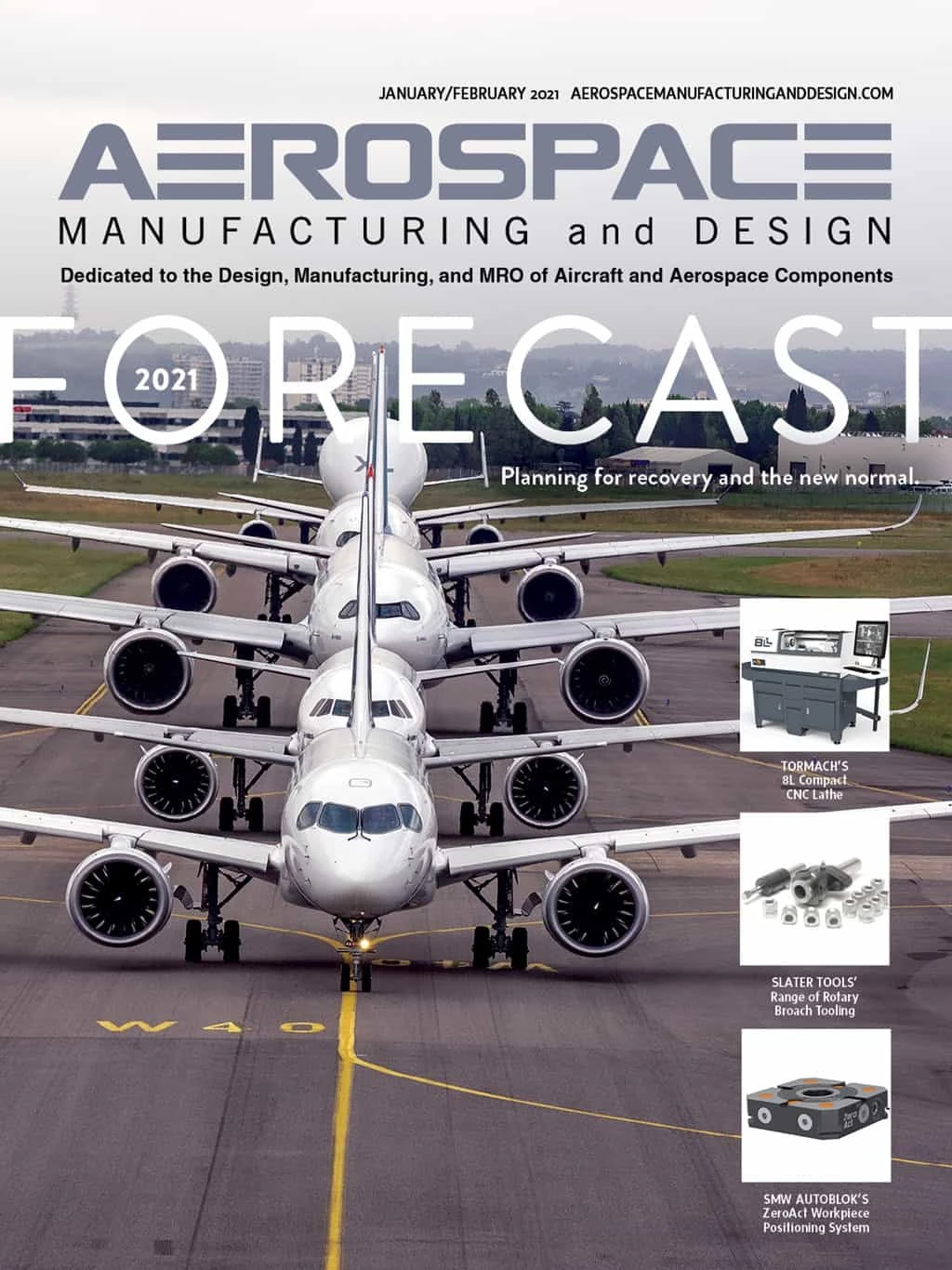
Explore the January February 2021 Issue
Check out more from this issue and find your next story to read.
Latest from Aerospace Manufacturing and Design
- Piper Aircraft receives its largest ever domestic trainer order
- Miniature, high force-to-size linear voice coil servo motor
- MagniX, Robinson to develop battery electric R66 helicopter
- Zero-point clamping modules
- Hartzell electric engine propeller earns FAA approval for AAM
- Thin profile flame and thermal barrier
- Guill Labs offer materials and extrusion testing
- High production vertical honing systems